The lighting brand Ilex Architectural Lighting was founded on a made-in-America premise “in order to maintain our company’s domestic manufacturing base,” says Ben Duggan, who is Vice President of Product Development of both Ilex and its parent company Norwell Lighting. Yet the East Taunton, Mass.-based executive also notes that Ilex had perhaps branded itself too well in the minds of specifiers. “Our customers have a clear understanding of our products. We do a lot of traditional-type light fixtures, in what I would call standard industry finishes.”
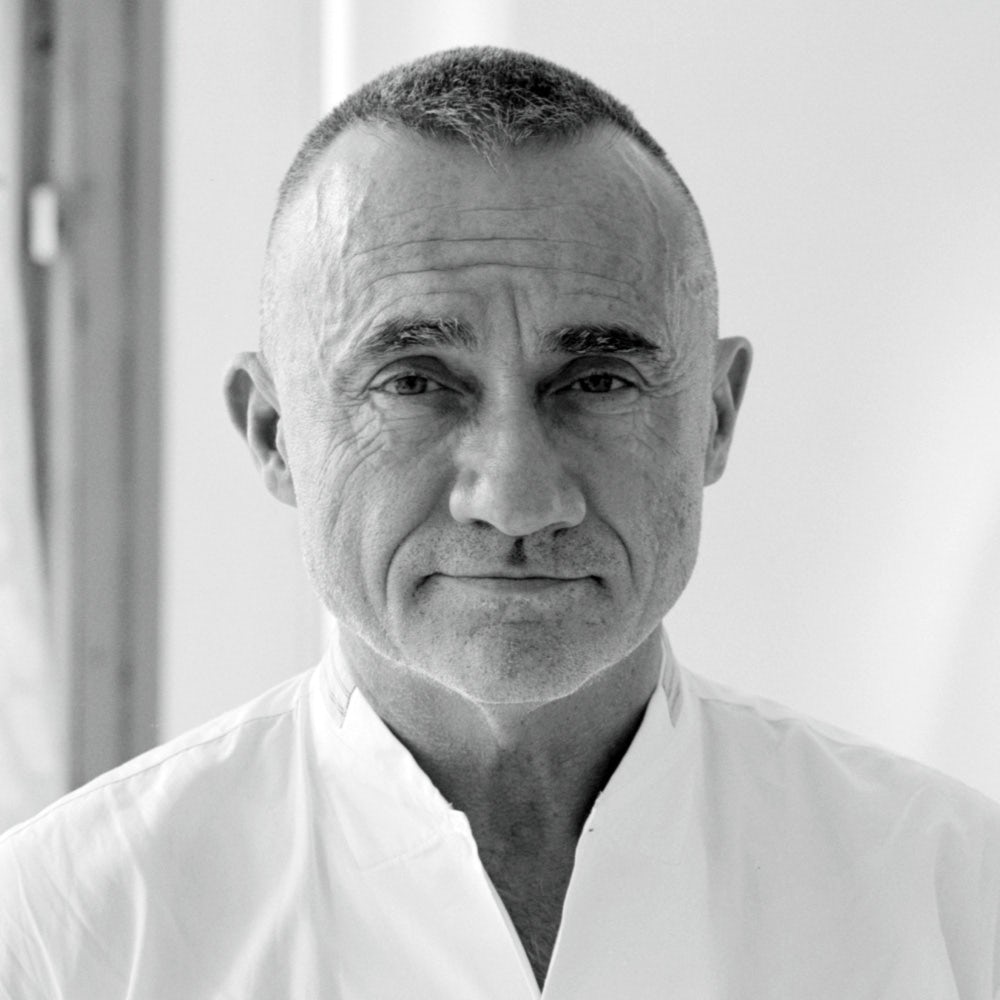
Kevin Walz
Launched a year ago, the Portfolio is, as Duggan puts it, “an attempt by Ilex to do something different and reinvigorate the brand. With this initiative, we wanted specifiers and interior designers to give us a second look, both through the fresh perspective of designers like Kevin, but also by using different materials and technology like LED.” Kevin refers to Kevin Walz, who is as known for creating furniture and products that suit any number of designers’ needs as he is for crafting interiors that can’t be replicated from catalogs. This month sees the addition of Walz’s Mercury and Vesuvius luminaires — biomorphic, ceiling- or wall-mounted discs made of spun polished aluminum, punctuated by hammered-metal baffles — to the Portfolio. To mark the occasion, designer and client spoke to Architizer about making a new business plan come to life.
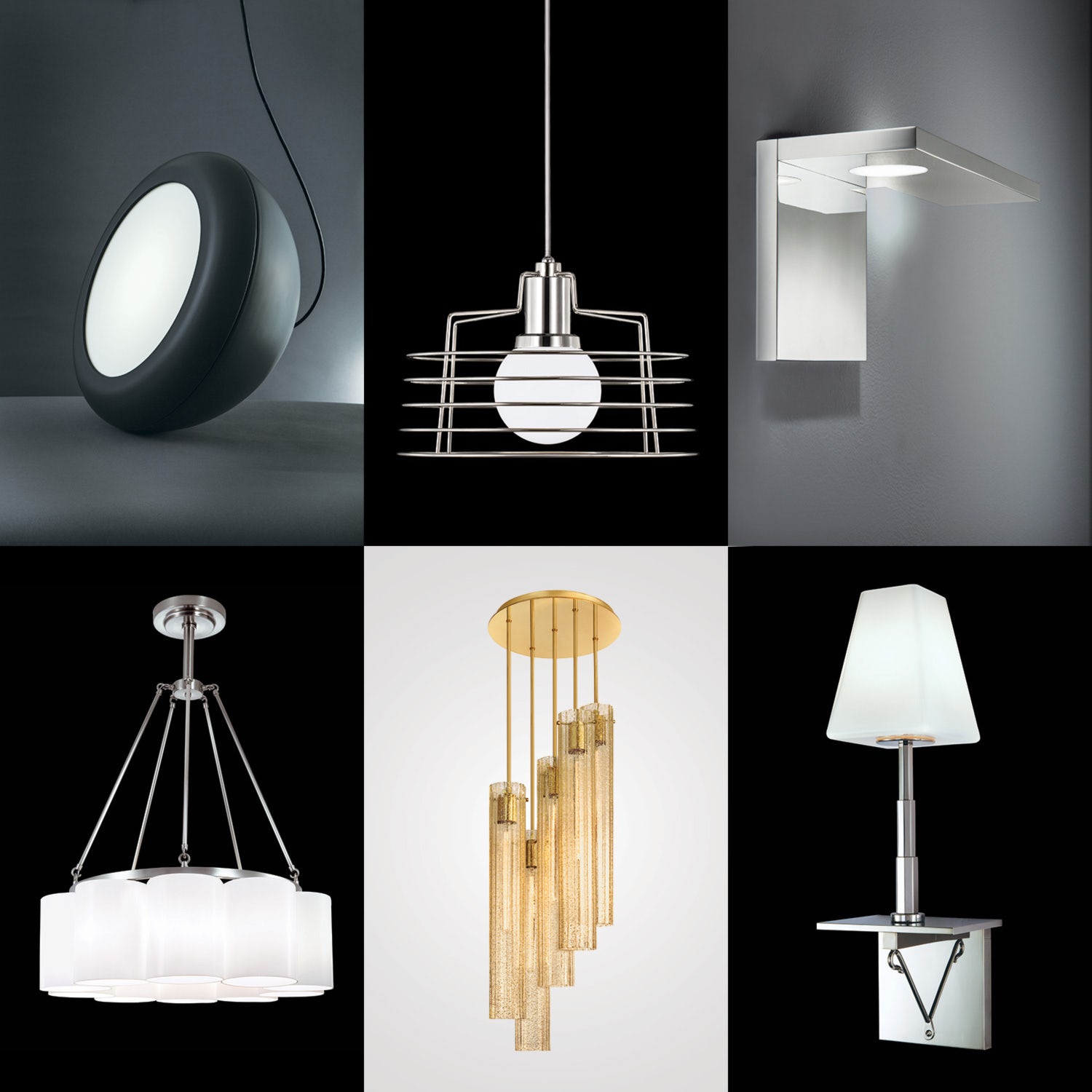
Selections from the Portfolio (clockwise from top left): Chroma by Christopher Poehlmann, La Cage by Mick Ricerto, Edge by Michael Wolk, Gala by Michael Graves, Libro by Laura Kirar, Tabletop by Michael Graves.
Architizer: To initiate this collaboration, who found whom?
Kevin Walz: They contacted me, though I guess I didn’t see the emails for awhile. Ilex is part of Norwell, in East Taunton, Massachusetts — it’s the new designer branch of the company. They were putting together a nice group of designers. But really I said yes because Ben said, “We have a shop, a factory of very skilled laborers who have been with us for decades, and we don’t want to give up on them; we don’t want to ship everything overseas.” I immediately came on board.
Ben, would you elaborate on this made-in-America premise?
Ben Duggan: Much of the residential lighting industry has outsourced manufacturing to countries like China. The Ilex brand focused on a higher-end market segment, which would support the cost of manufacturing in the U.S. Most of the people who work in our factory have worked in lighting and metal fabrication for more than 25 years. We felt that their unique skills had value, and that we should try and preserve those capabilities as a company. So far it has served us well.
Did the labor pool — its specialties, for instance, or the available equipment — inform the design concept?
KW: I’m an interior designer, but I am not a specifier. I design almost everything in almost every project. So I have a gazillion ideas about lighting and things. I start out with what kind of light I want to produce and what the light quality should be. So I came up with four ideas of lighting, and this first collection has two products whose intent was to create completely reflective light; all the light would bounce into a concave lens and be distributed that way.
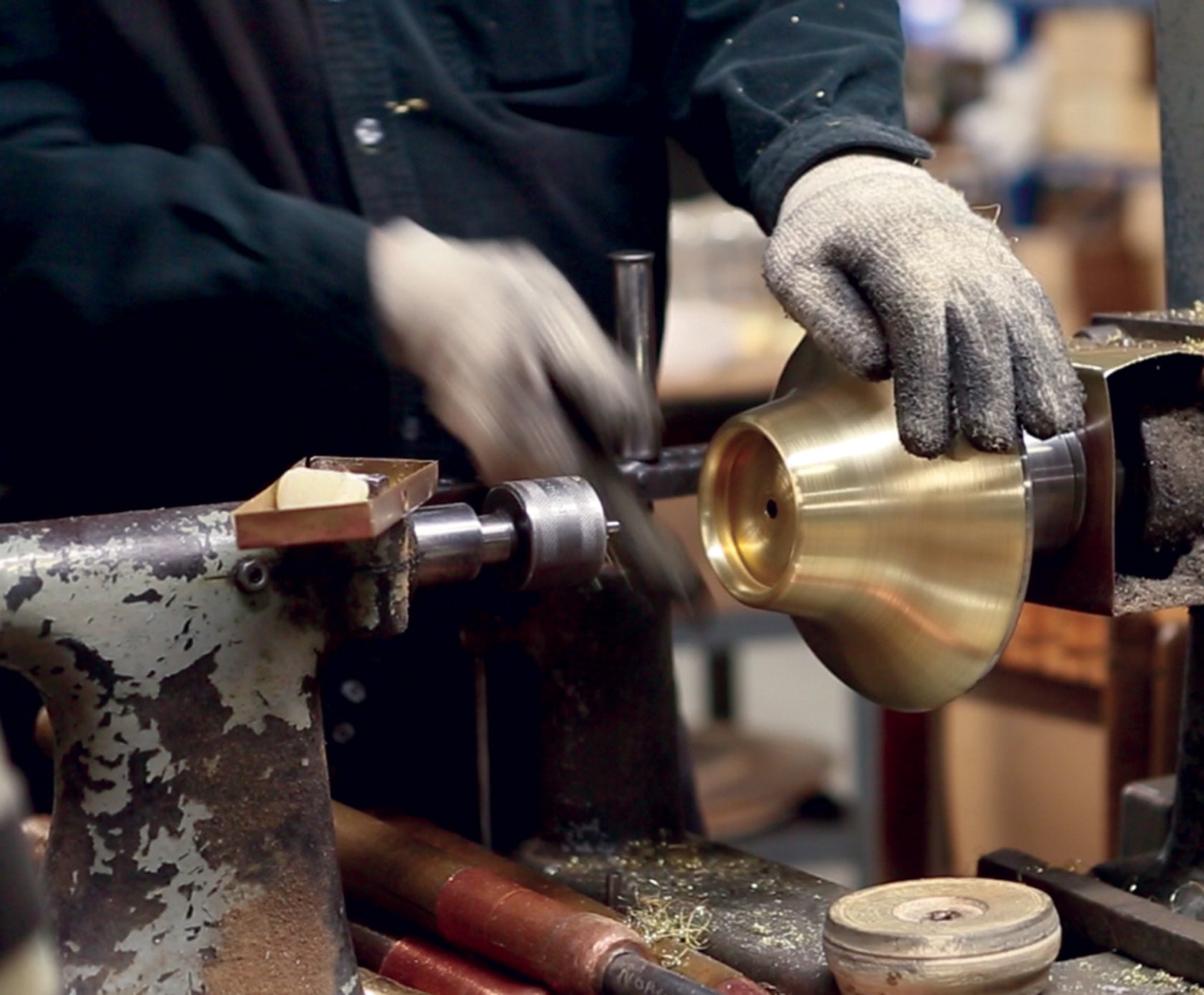
Spinning the Vesuvius.
In an era of illuminated screens, does this soft light have more relevance?
BD: I don’t know if it has more relevance, but it definitely has a place. The great thing about Kevin’s design is the way it contributes to the ambient light without overpowering you. This is especially appealing in a residential environment, I think.
KW: It’s the kind of light that is the least addressed. I think light that is bounced off a surface to illuminate a room is the most beautiful light. It always creates a sense of calm, and a sense of complexity and richness of color, as well as softness of shadow.
How different was the initial concept?
KW: The initial fixture was a 22-inch-round disc that was concave and recessed into a sheetrock ceiling. There would be no sense of it existing. The problem was that that entire hole has to be fire-protected. So we had to drop it down, and I created this shape that I wanted to be very liquid and highly polished. I had no idea this could be hand-spun in one piece of aluminum. The result reminds me of Anish Kapoor.
Was Kapoor your influence?
KW: Actually, the work was inspired by Breuer’s lobby lights at the Whitney. Also, I had designed a recessed light for a recent project on Central Park West, where there were some dropped ceilings in which you could insert discs; the fire rating was not required at the level of the dropped ceiling. They created such beautiful light. And we created a spherical baffle underneath the bulb so that light bounced up and around. In this case, I had a chance to think more about form, which is like a drop gaining some weight before it falls.
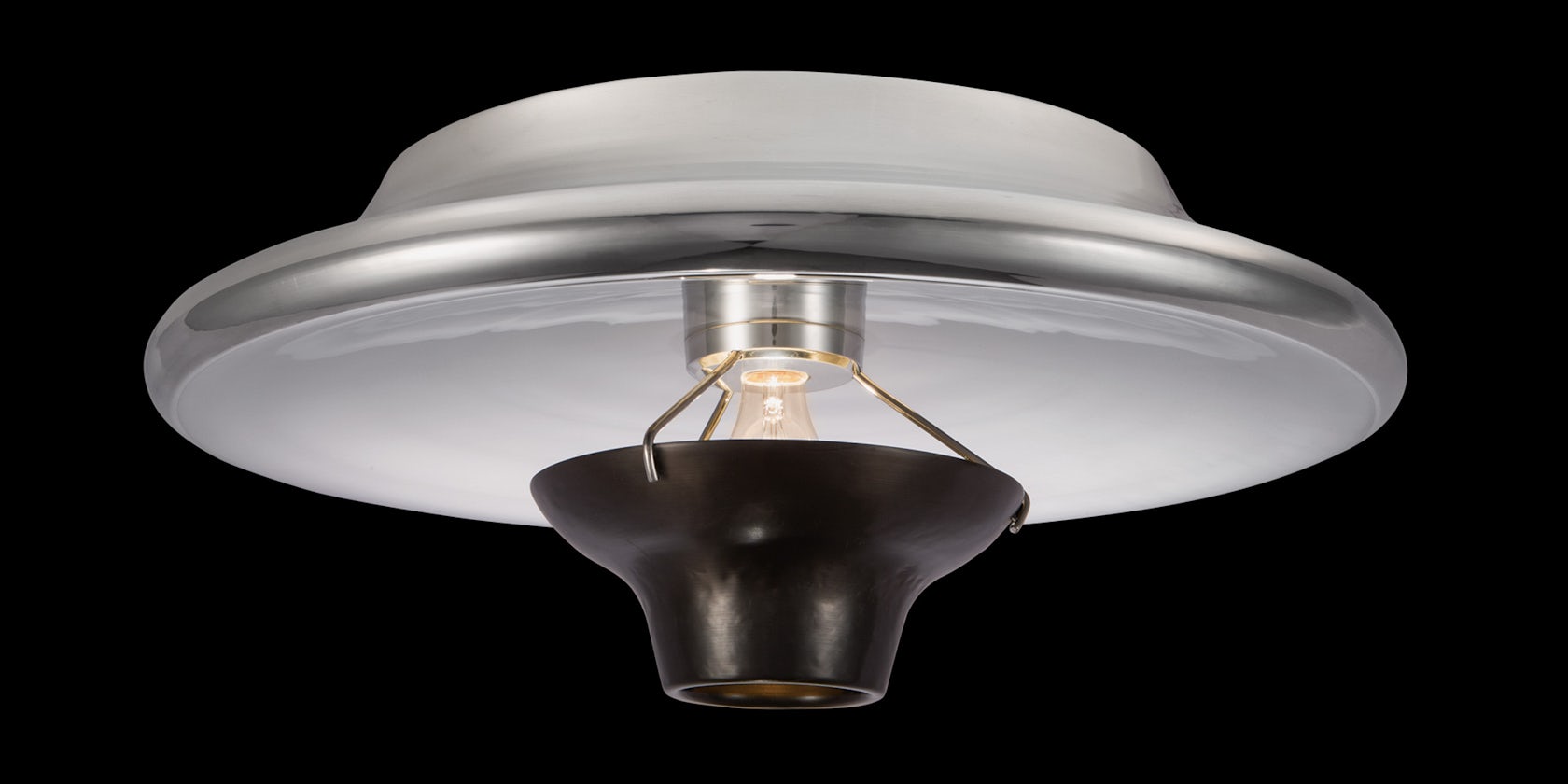
Vesuvius
How did the East Taunton workshop keep pace?
KW: Ben never showed any sweat; he never rolled his eyes. He was really enthusiastic about what we were doing and fought to make it happen. We tried a lot of different things.
For example, our first goal was to make the baffle of mercury glass so that some light would come through while still having a reflective quality like the polished aluminum. But we scoured the world for a source, and we just didn’t find anybody receptive to that. Then my metalsmith suggested hammering nickel-plated brass or stainless steel, and I really liked the beautiful relationship with the highly polished surface. Ilex was very excited because they could give that hammering work to one of their own guys.
BD: As we started fabricating component parts and working with our suppliers, we ran into barriers. The original design had a glass baffle that we ultimately had to abandon because none of our suppliers could produce it well. Fortunately, Kevin knows what design elements are worth fighting for and those that need to be reconsidered in order to move the design forward. It took much longer than expected, but everyone stayed committed to the goal.
Functionally and aesthetically speaking, how do Mercury and Vesuvius complement the other Ilex designs?
KW: I would say it’s broadening the range.
BD: In terms of the Ilex product line, these offer a very different approach to this type of light fixture, which often emphasizes high lumen output. And with the whole Portfolio series, our hope is that by working with designers and getting out of our comfort zone a bit, Ilex will be discovered by a whole new audience of people who appreciate unique, well-made light-fixture designs.
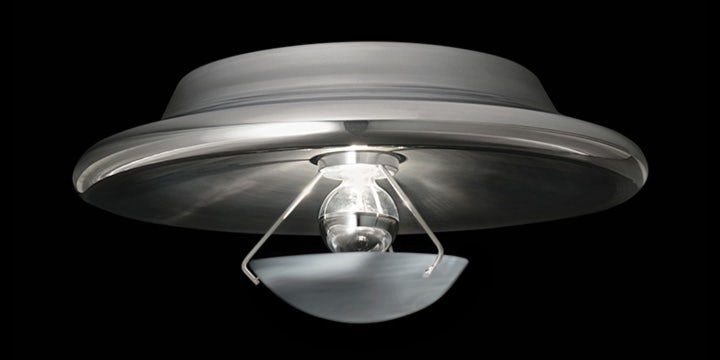
Mercury
What Ilex fixture sells best today, and what does that reveal about your buyer? The corollary question: how do you think these specifiers will react to Kevin’s work?
BD: It depends on the market we’re selling to, but you can never have enough ADA wall sconces for the contract lighting market. The Ilex Cube sconce series is very popular. It’s a very simple, clean design that incorporates real wood finishes. It suggests something slightly upscale, but it can be priced very competitively. I think that Kevin’s designs will have great appeal with people involved in higher-end projects, especially where there is a commitment and focus on really great design.
For what kinds of space will Mercury and Vesuvius be specified, do you think?
BD: For me, the shape of the large polished aluminum body has a sculptural appeal all by itself. I can see the Mercury fixture being specified in a variety of residential spaces. It could easily be specified in a boutique hotel setting, as well. Almost any hospitality environment that wants something more than a generic ceiling fixture would appreciate this design.
KW: The design’s abstraction is nice. So, a client of mine with a 1700s-era house in Litchfield wants this over his dining table, and friends who live across the street from the Brooklyn Museum want this in their entry. I think it’s timeless; it looks like old Futurism.