The Extended Entry Deadline for Architizer's 2025 A+Product Awards is Friday, February 21st. Get your brand in front of the AEC industry’s most renowned designers by submitting today.
As architects and designers, our relationship with plastics is a complex one. Plastics have a bad reputation right now. Humanity’s overconsumption of polymer materials in the last century has resulted in the harrowing images we are now seeing on a daily basis — our seas brimming with bottles, sidewalks strewn with bags and animals caught up in cables. These heartbreaking photographs add fuel to the fire in public campaigns demanding that the use of plastic be either banned, or heavily restricted.
In this context, many architects and designers are afraid they will be seen as “unsustainable” if they propose it. However, it’s not plastic, as a material, that is the problem. It’s how we choose to use it. Many companies have developed innovative and exciting strategies to allow us to use plastic in sustainable ways, with a huge variety helping to reduce the level of plastic waste currently in the world.
Bolon
Over the past 70 years, Bolon has gone from a small family business to an internationally renowned design brand. Still a family business — now run by sisters Annica and Marie Eklund — Bolon started with a way to reuse textile waste by making rag rugs from the offcuts. Today Bolon’s goals are the same, but rather than reducing textile waste, they are innovators in reducing plastic waste.
Flow was Bolon’s first recycled flooring collection. The company adopted a process that takes old bits of flooring and grinds them into granules that can then be bound and reshaped into a new material that starts the cycle over. They also accept waste products from other manufacturers, getting rid of dangerous substances and recycling materials worldwide. Their process is low emission and their materials absent of phthalates making the flooring they offer non-hazardous and giving them an incredible life span of 10-15 years. At this point, they can be recycled into new material.
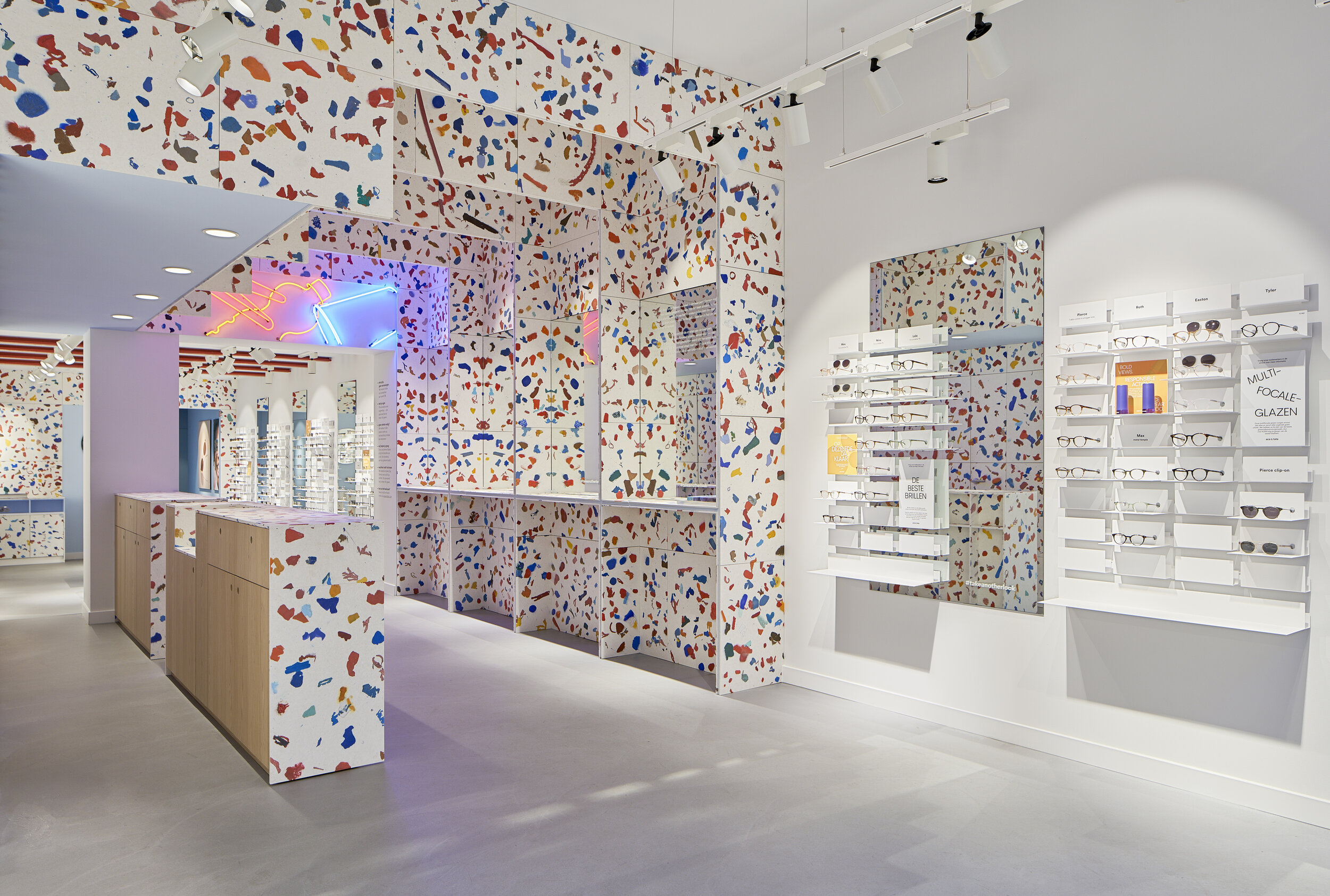
Ace And Tate store designed by Plasticiet with Ace And Tate, made by Teamwork. Photography by Lennart Wiedemuth
Plasticiet
Plasticiet is a relatively new material. It was conceived and manufactured in the Netherlands in 2018 by Marten van Middelkoop & Joost Dingemans, who tired of the problem created by mass-produced, single-use plastics. Plasticiet is a collection of high-end, design-led, fully recycled surface materials.
Created with reuse and repurpose in mind, Plasticiet uses raw ingredients that are easy to recycle and have sizeable, consistent waste streams. Each surface uses a singular material like fully recycled polystyrene or polycarbonate so every panel can have a circular lifespan and is never wasted. With the ability to process large volumes of otherwise unwanted or contaminated plastic destined for landfill or incineration, Plasticiet captures and transforms it into a material for furniture, fixtures, architecture and design.
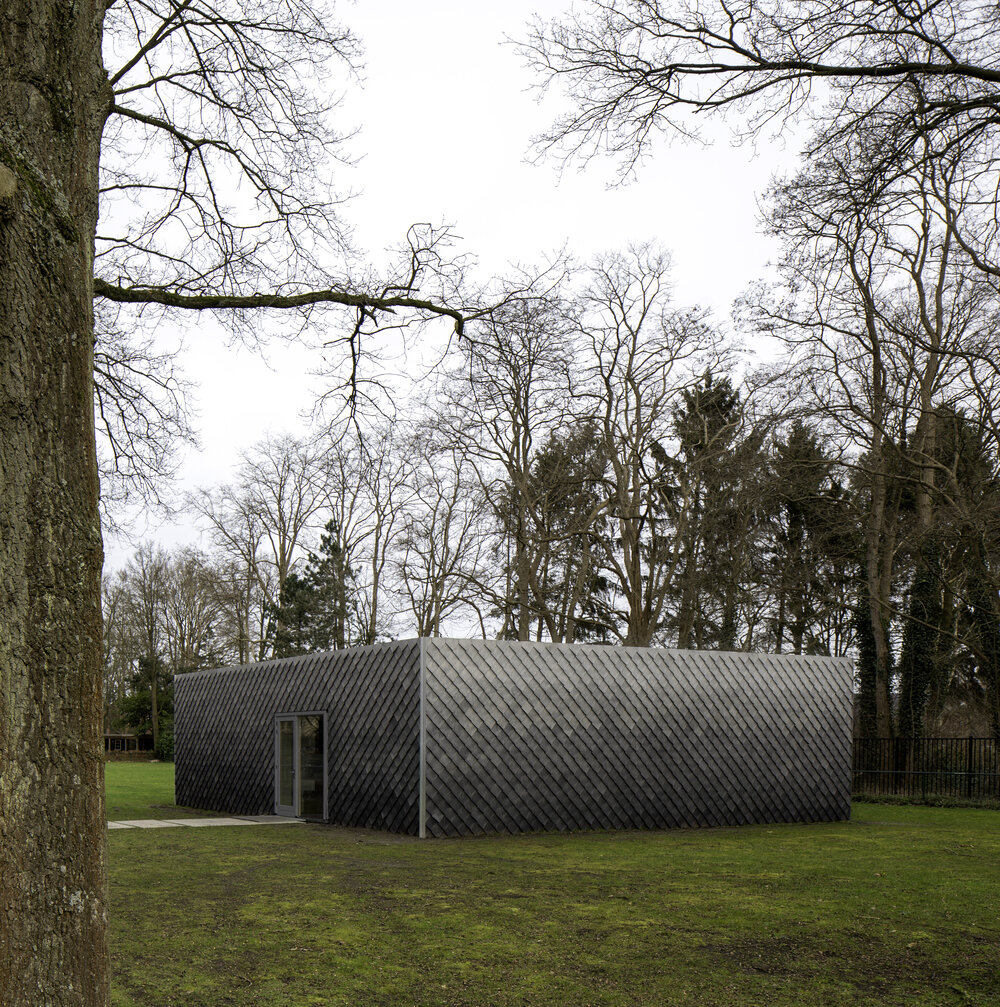
Sint-Oelbert Gymnasium School by Grosfeld Bekkers van der Velde Architecten, Ooserhout, Netherlands
Pretty Plastic
Pretty Plastic is the brainchild of architects Peter van Assche of Bureau SLA and Reinder Bakker and Hester van Dijk of Overtreders W. Inspired by household waste and determined to contribute to a circular economy, the Dutch team developed the first recognized facade material made from 100 percent upcycled plastic waste.
Pretty Plastic design and manufacture facade shingles. The tiles were initially developed for the People’s Pavilion, a temporary auditorium constructed at Dutch Design Week in Eindhoven in 2017. The pavilion demonstrated how the principles of the circular economy could be applied to architecture, with every component designed to be used again once the structure was decommissioned. The pavilion was clad in 9,000 bespoke molded plastic shingles made of waste collected from local residents.
After years of development and testing, the team now has a fully certified cladding material. Each tile is made from waste plastic collected from building sites across the Netherlands before being sorted and shredded. After being cut up, they are shipped to Belgium, where they are transformed into shingles by Govaplast. The Sint-Oelbert Gymnasium school at Oosterhout in the Netherlands is the first permanent structure to be clad in the shingles.
Camira
Camira is a well-established brand synonymous with fantastic quality and beautifully designed fabrics. In 2020 they pledged to do more to support the planet by developing and introducing their first fabric made from sea waste. Partnering up with SEAQUAL, Camira launched Oceanic.
The new product is created entirely from post-consumer recycled plastic, including debris discarded into the seas and bottles thrown away and destined for landfill. Oceanic is a strong and durable upholstery fabric in a range of usable and contemporary hues. Delicately dyed using cationic yarn, the multi-tonal textile contrasts a light warp with a darker weft. This visual detail creates a subtle pattern with an intricate twill weave, enhancing both the considered color and careful construction of the fabric.
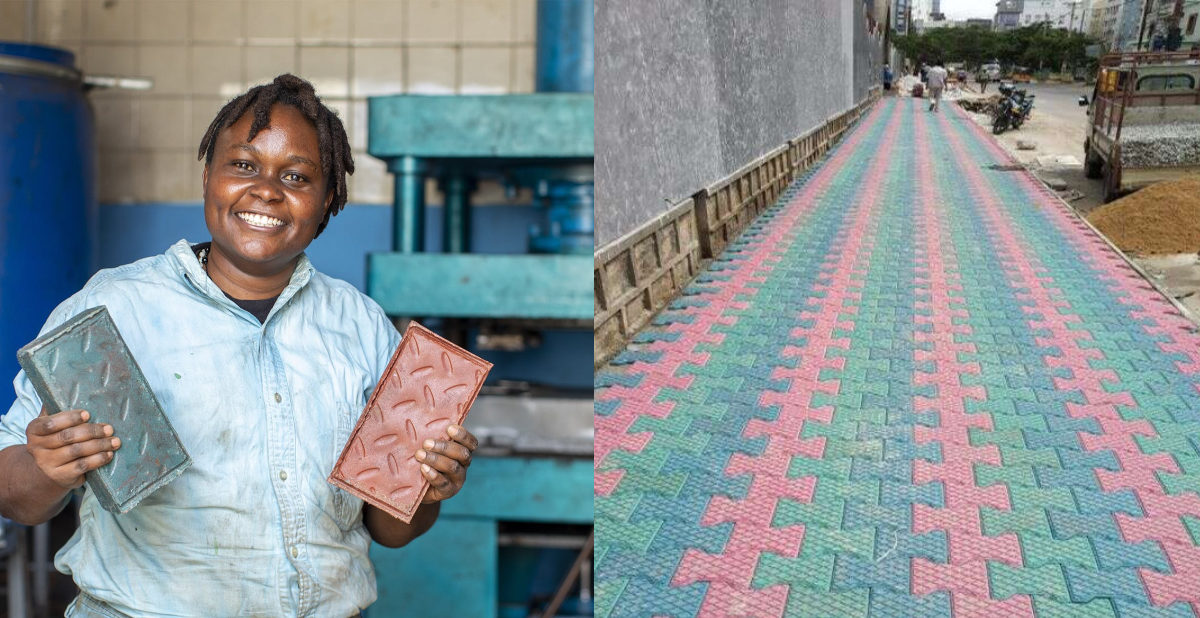
Nzambi Matee innovator and owner of Gjenge Makers
Gjenge Makers
The self-professed new kid on the block, Gjenge Makers is a social enterprise whose aim is to address the need for sustainable and affordable alternative construction materials in Kenya. When entrepreneur Nzambi Matee decided to start Gjenge Makers, her objective was to think of solutions to the plastic pollution problem. A material science major, Nzambi worked as an engineer in Kenya’s oil industry; then, in 2017, she left her job and began manufacturing recycled bricks. She understood which plastics would bind better together, working with a combination of the high-density polyethylene used in milk and shampoo bottles, the low-density polyethylene found in sandwich and cereal bags, and the polypropylene used in ropes and buckets and then created the machinery that would allow her to mass-produce them.
Now, Nzambi employs 112 people from marginalized communities as plastic pickers, providing jobs to women and young people who otherwise would not have the opportunity to work. The Nairobi-based factory can produce 1,500 bricks and recycle about 500 kilograms of waste plastic a day.
Gjenge paving bricks come in an array of colors. They are strong, tested to hold twice the weight threshold of concrete blocks and are far more durable under stress and are lighter to transport. They produce different bricks ranging from heavy-duty paving for roads and parking areas to light-duty paving for footpaths and household compounds in areas.
The Extended Entry Deadline for Architizer's 2025 A+Product Awards is Friday, February 21st. Get your brand in front of the AEC industry’s most renowned designers by submitting today.