Find the perfect concrete, wood or aluminum products for your next project through Architizer’s new community marketplace for building-products. Click here for more information. It’s free for architects. Are you a building-product manufacturer looking to connect with architects? Click here.
Rios Clementi Hale Studios is a practice exploring the boundaries of design. Making a name for themselves since their founding in 1985, RCH recently moved to a new home in the West Adams neighborhood of Los Angeles, California, to house the firm’s rapidly growing staff. A multi-disciplinary design firm, RCH prides itself on the idea that design is everything when it comes to the built environment.
Embracing trans-disciplinary practice, the firm has expanded to encompass architecture, landscape, urban planning, interior design, signage, exhibition spaces and product design. Grounding these disciplines is a rich understanding of materials and construction fundamentals. Architizer sat down with Andy Lantz, an architect and Senior Associate at Rios Clementi Hale Studios, to discuss his favorite materials and specification processes.
Beginning with one of his favorite materials, Lantz began by discussing concrete and its application in some of RCH’s recent work. “There is something poetic and surreal about building with precast concrete,” said Lantz. “When working on the design of our mixed-use tower at Sacramento’s Downtown Commons (DOCO) — a rejuvenating project that has helped to reimagine development in downtown Sacramento — we mocked up various formliner designs for a precast exterior panel that tested the integration of texture to activate the surface within the overall breadth of the large façade.
“We relied on milled MDF to understand pattern, scale, intervaling pattern, and final visual effect. It wasn’t until we were able to visit the manufacturer during production outside Sacramento that the full impact of the material and the geometric patterning was realized. The color and aggregate captured the natural light and produced an experience that extended the surrounding environmental colors in a way that allows the building to camouflage itself by absorbing the dynamic saturation found in California sunsets, with a slight textural repetition.”
Beyond concrete, Lantz discussed the beauty of wood joinery and how custom fabrication partnerships could produce exciting possibilities for the design process. He touched on the large amount of commercial work created in Southern California and Austin, Texas, and how these investigation have driven a forte for collaborating with talented fabricators to create signature, custom projects and installations of all sizes. “When working on a custom reception desk and conference tables for Steelhouse in Culver City, we teamed up with Machine Histories, an LA-based machine shop and fabricator, to work through the complexities of building out a geode in oriented strand board (OSB),” said Lantz.
“One of the biggest dilemmas with OSB is that it is extremely vulnerable to dual axis movement and renders adhesive failure with complex chipping and broken flakes. Our design was made up of 32 unique faces that intersected, on average, at 8 edges each with unique angular relationships from one piece to another. In an effort to maintain the minimal tolerances that would keep the edges from bearing weight on each other, a complex system of rigging was used.
“Ball hinges and bolt connections balanced each plane in its geometric relationship with its corresponding adjacent planes. This process of manipulating a difficult material brought about a surprising discovery: we applied a high brow detail typically reserved for precious stones to the low brow application that geometrically balances an off-the-shelf material for construction.”
Lantz also finds innate beauty in the aluminum, reveling in the material’s malleability. Though it is not typically used for structural applications, Lantz has worked with aluminum to explore its strength and aesthetic. “When working on the Hollywood Bowl Box Office Plaza, we developed a custom canopy installation with an aluminum span of thirty-six feet without the aid of secondary bracing,” explained Lantz. “We couldn’t afford the switch to steel due to complex soils, so we consulted our structural engineer for possible solutions.
“We discovered a way to make aluminum structural by folding it into a three-dimensional profile with water cut voids to reduce weight and preserve the flow of forces. Provided with the exact parameters — minimum requirements for opacity limits, tolerances for water cutting, and general principles for offsets adjacent to folds to maintain strength — we were able to script design studies with various perforations, allowing sunlight to cast pattern throughout the plaza and rendering the final installation light and airy.”
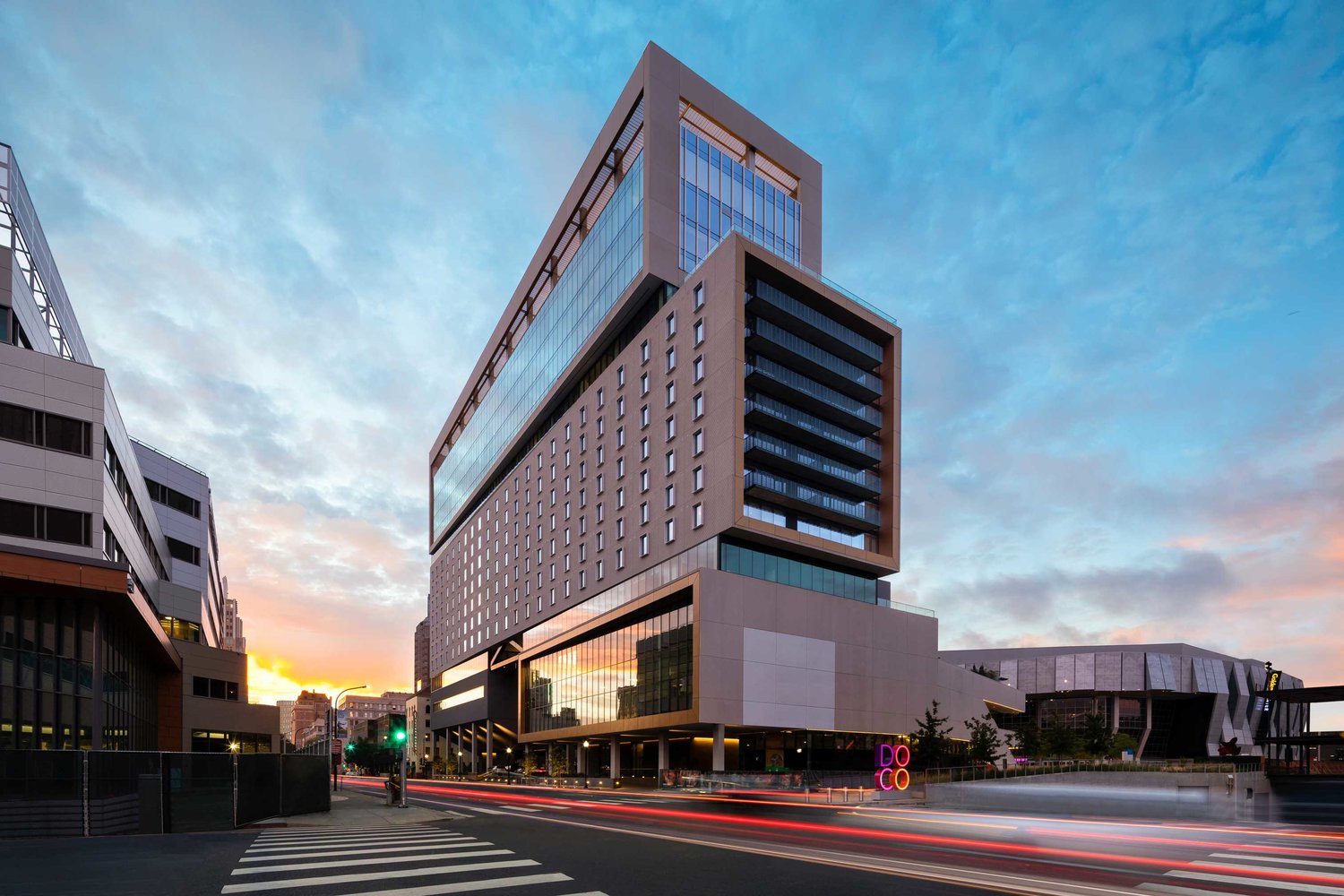
Sacramento ESC by Rios Clementi Hale Studios, Sacramento, Calif.
Recognizing the challenges that come with specification, Andy stated the difficulty in finding the right fit. Through a belief in high levels of customization, Andy explores projects and research that have led to alternatives to specifying specific products. These are seen most readily in the opportunities found in the maker culture of Los Angeles and adapted work flows that preferences local fabrication. Andy acknowledged the advantages to designing and building in a local market to avoid delays and international expenses.
Lantz believes that when developing projects, building material manufacturers should carefully consider customization. “This term used to be met with trepidation for clients, whereas the pay offs are now deterring the fears,” said Lantz. “Our clients desire spaces that convey who they are and that express their unique attributes, so why should we always feel the need to fill it with off-the-shelf commodities? We have found tremendous collaborations when we have worked directly with manufacturers to customize their lines — altering everything from the way their product is fabricated to their actual designs — to bring a uniqueness to the application within the spaces we design.”
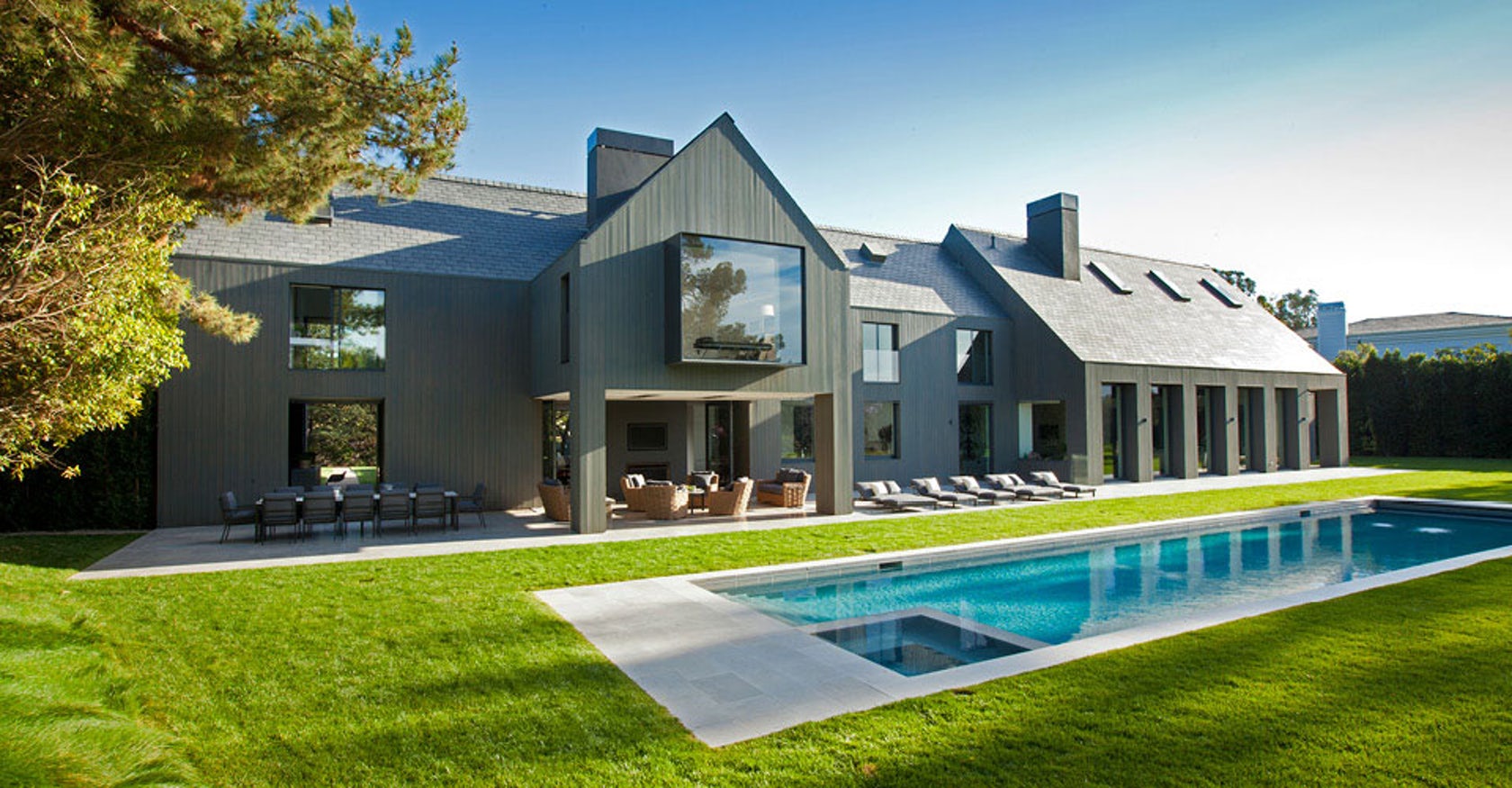
Modern Barn by Rios Clementi Hale Studios, Santa Monica, Calif.
When asked what his favorite application of a material was in a project by one of his peers, Lantz turned to Eric and Meejin at Höweler + Yoon. “Their work hones in on a handmade aesthetic and an understanding of material properties culminating in an expertise in composure and material honesty,” said Lantz. “For instance, at the Collier Memorial at MIT they’ve composed granite and gravity into a five-way arching vault that conveys a whispered mastery over the material. It is absolutely stunning, and when combined with the narrative of the project, it forces you to applaud their skills.”
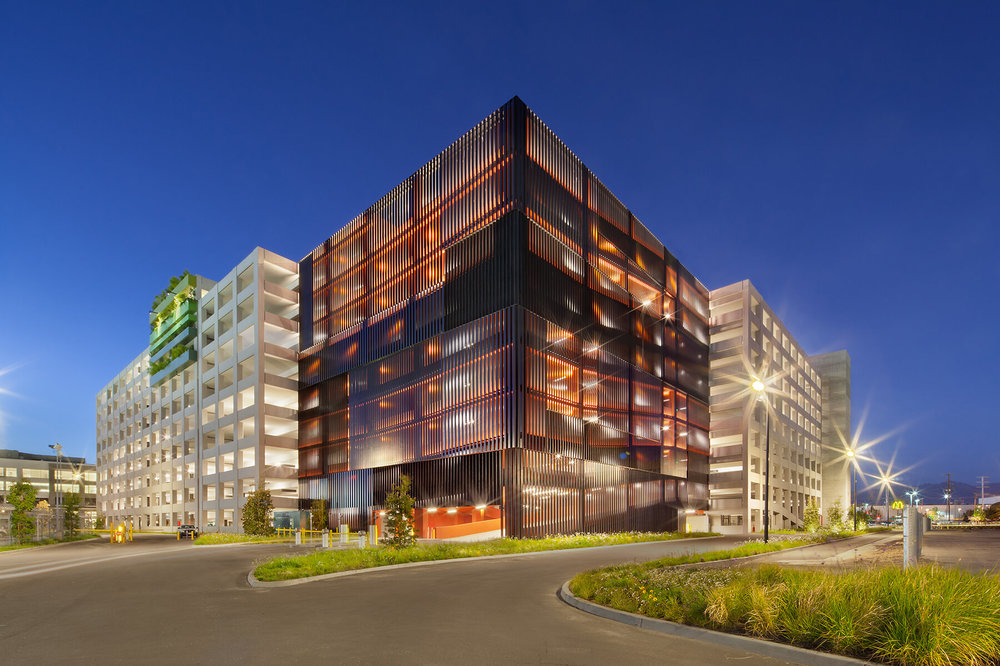
ROW DTLA by Rios Clementi Hale Studios, Los Angeles, Calif.
Lantz had three key pieces of advice for young architects specifying a project for the first time:
- Why buy it when you can invent it: Always remember that we are designers and every local market has artisans, fabricators and inventors ready to explore with you.
- When you have to buy it, learn how to be a better shopper: Trends come and go, but finding timeless things is hard. Curate your strategy for reinventing the timeless in your designs.
- Don’t be afraid of specifications: One of the most impactful moments of my professional development came when I grasped an understanding for how specifications work. Trust me, they are empowering.
Discover more of Lantz’s work and the exciting projects happening at Rios Clementi Hale Studios through their firm profile.
Search for the perfect architectural materials through Architizer’s new community marketplace for building-products. Click here to sign up now. Are you a building-product manufacturer looking to connect with architects? Click here.