The jury and the public have had their say — feast your eyes on the winners of Architizer's 12th Annual A+Awards. Subscribe to our Awards Newsletter to receive future program updates.
Construction has begun on the first two-story 3D-printed structure in the United States. Located in Houston, the 4000-square-foot home will soon become one of the world’s largest and tallest printed buildings, showcasing the rapidly expanding possibilities of 3D printing technology and mass customization in the field of architecture.
The project caps off a two-year collaborative effort between HANNAH, an experimental design firm and research studio based in Ithaca, PERI 3D, an international 3D construction printing provider, and CIVE, the leading engineering service and general contractor in Houston. The design uses a hybridized construction method that will combine printed concrete modules with wood framing, making it one of the first 3D printed to use wood and concrete in an integrative manner.
Spearheaded by Leslie Lok and Sasa Zivkovic, assistant professors at the College of Architecture, Art, and Planning at Cornell University and principals at HANNAH, the project began with the objective of developing a 3D printed construction system that could be scalable and applicable for multi-family housing the future — not an easy feat given the additional structural challenges when printing beyond a single story. As such, Lok explains that it was necessary to develop the design in relationship to the material and construction process.
“Every aspect of the project, from the overall spatial configuration to the scale architectural detailing — such as how we create shelving and openings — was informed by the unique fabrication logic of 3D printed concrete,” Lok said. “With the structural engineering expertise from CIVE and the extensive printing knowledge of PERI 3D, we were able to develop an approach to 3D print the second story.”
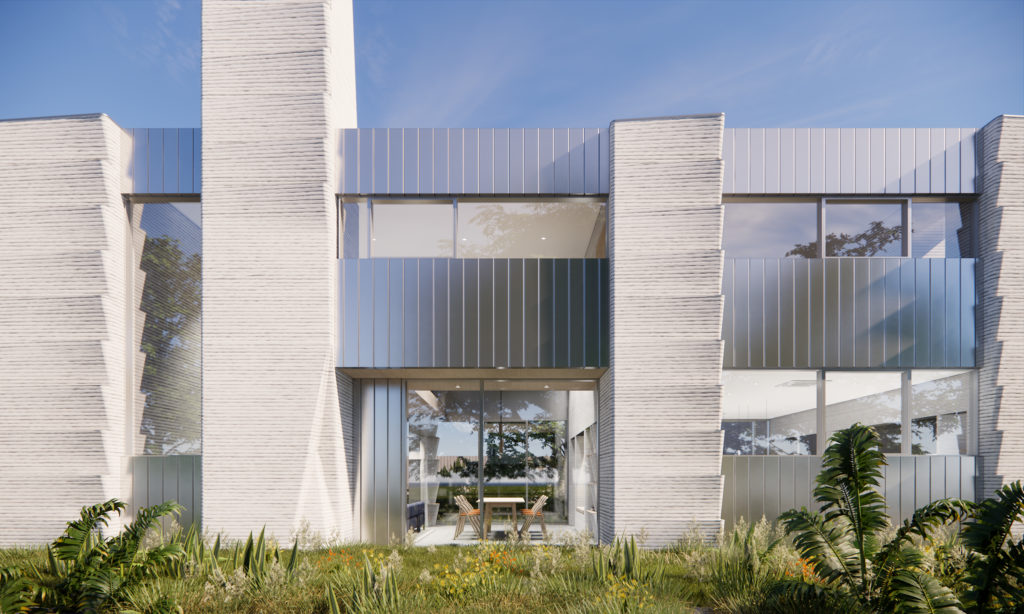
Once completed, the project will alternate between concrete modules and glazed wooden frames; rendering by HANNAH
Though a handful of 3D printed multi-story projects have been built abroad, mostly in Europe, HANNAH’s design stands out for its adaptation to the American construction culture of wood framing. Whereas the use of precast concrete components for floors and ceilings has long been a European norm, wood framing as a construction technique is much more prevalent in North America, though their integration in 3D printed construction has so far been limited. In response to this, HANNAH sought to create a design that would be more easily applicable to the U.S. market. The final result is a house that alternates between wood and printed concrete volumes, a strategy that combines the best of both materials, the pair explain.
“What is unique about our modular design is that the printed concrete and the wood framing work hand in hand and we use them where they’re best performing,” Zivkovic said. “It’s not about printing concrete everywhere because you could, but where it makes sense.”
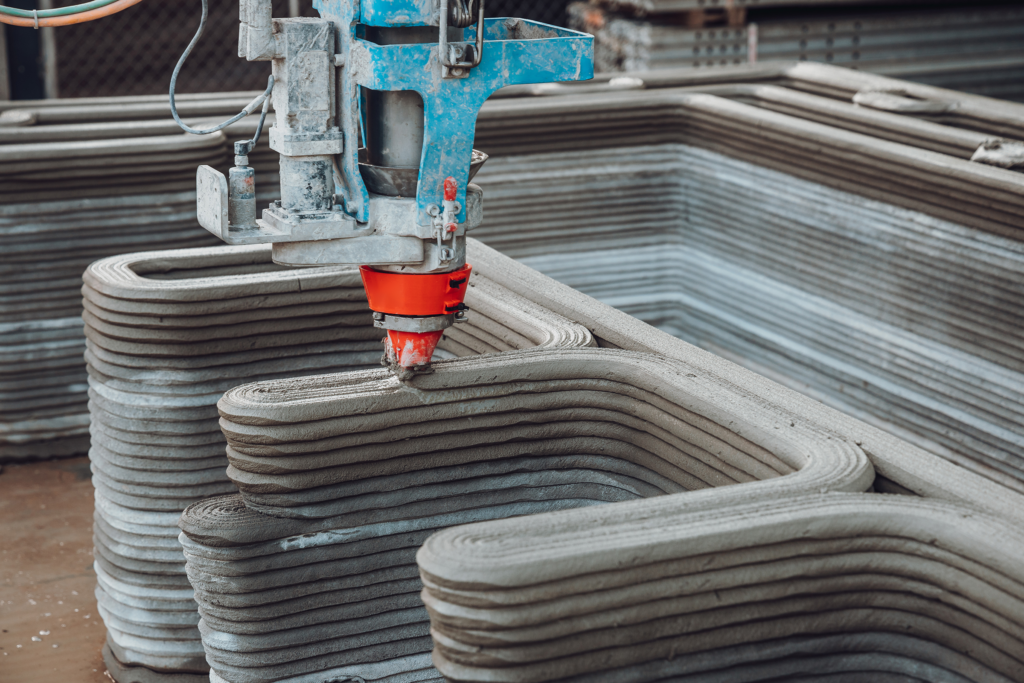
Photos by Anthony Vu via HANNAH
In part, the project is showcasing the usefulness of 3D printing for the future construction industry. The modular 3D printer — a COBOD BOD2 gantry printer — takes only one day to set up, and the printing can run 24/7. Although a handful of people are still needed on the worksite to supervise the machine, the printer does virtually all the heavy lifting.
Achieving the right printing mixture for the concrete was one challenge that necessitated the help of other industry partners. The PERI 3D printing team worked with engineers at Quikrete, a manufacturer of packed concrete, to achieve improved printability for their new generation of printing mixture at the specific site in Houston. The team conducted test prints on site earlier this summer to dial in the various printing parameters.
Designing the 3D printed house was another demanding part of the project, since unlike (human) contractors, 3D printing machines don’t read architectural plans but lines of code. The architects at HANNAH used special software to manually design the path that the printing machine uses to pour one continuous line of concrete for the new house; a meticulous process known as the ‘toolpath’ that equally comprises structural and aesthetic considerations, leaving no room for error.
Far from letting this complex process limit their design, HANNAH used the printing toolpath as an opportunity to push the design possibilities of 3D-printed structures. The repeated use of incremental cantilevers within the concrete modules serves as an architectural motif that is both ornamental and functional. Paired with the distinct horizontal layers of printed concrete, HANNAH creates a bold stylistic statement about 3D printed architecture; hinting at the opportunities of new design language for printed projects.
More broadly, the project is offering a glimpse of a future where 3D printing could become a major force in the construction industry; where automated construction could address a variety of pressing issues, from alleviating workforce shortages to constructing affordable housing. Still, much work lies ahead. For this project, the team hope to use the project as a learning opportunity to streamline the construction process, as well as to optimize material usage and cost for 3D printing buildings — all necessary steps that need to be undertaken if 3D printed architecture is to attain newer heights.
The jury and the public have had their say — feast your eyes on the winners of Architizer's 12th Annual A+Awards. Subscribe to our Awards Newsletter to receive future program updates.