Structural connections needn’t just be functional in architecture today: Thanks to companies like New York–, San Francisco–, and Toronto-based Cast Connex, they can also make for edgy or elegant details. In just nine short years, Cast Connex has grown quickly from startup status to the largest North American supplier of steel castings for architecturally exposed structural connections in buildings and bridges.
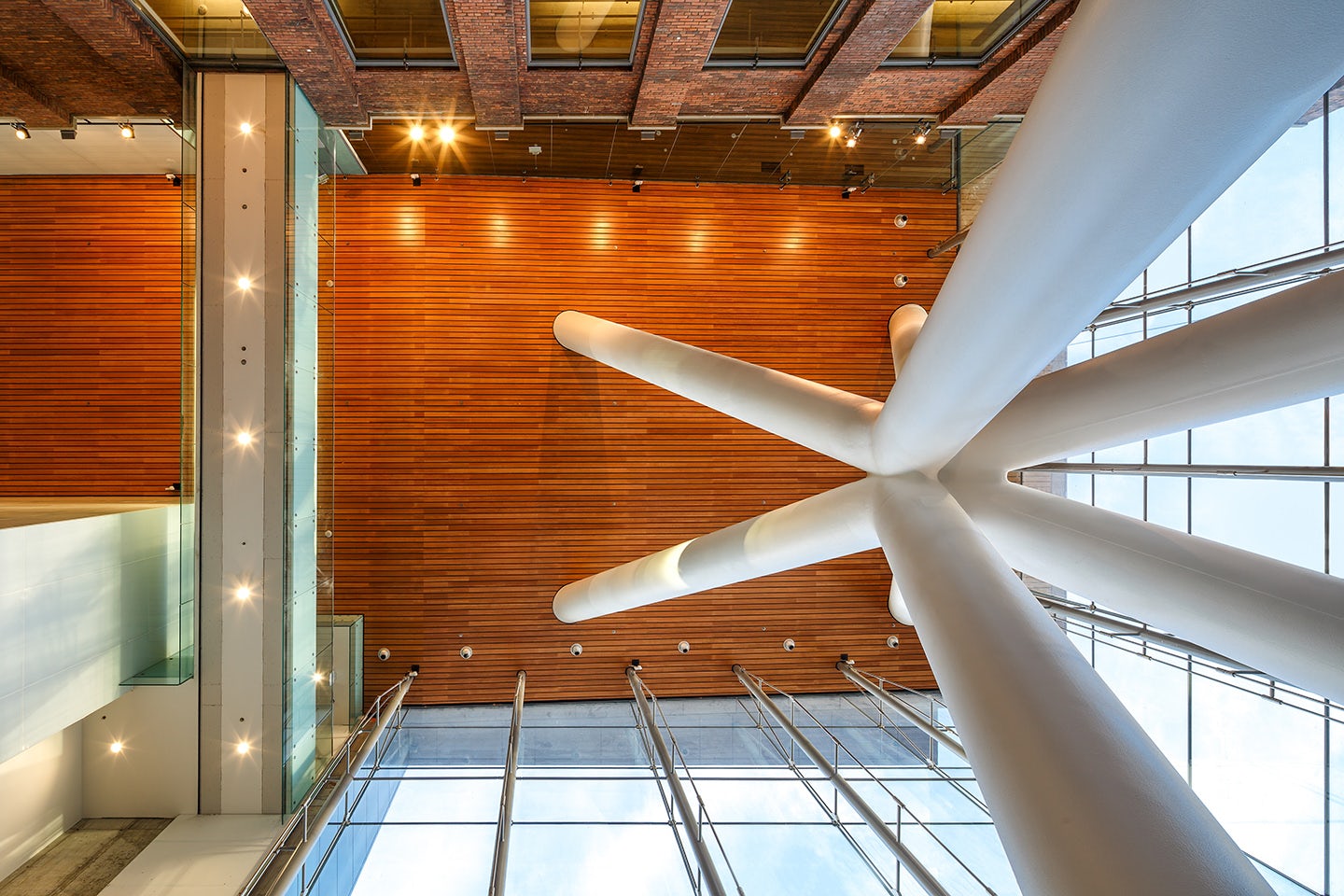
QRC West by Sweeny & Co Architects Inc.; photo by doublespace photography
“With our expertise in the industrial design and engineering of steel castings, we enable architects to leverage the manufacturing method to create free-form structural steel components. This provides architects with a new outlet for creativity in design for exposed structural connections,” says Carlos de Oliveira, president and co-founder of the firm. Cast Connex collaborates with architects and engineers to develop casting designs that simultaneously meet the aesthetic and functional demands of any project. They then engineer and detail the components, oversee their production and deliver the castings to the contractors building the structure. “Whether asking us to custom-design connections for a project or simply calling for the use of our standardized components, we work with architects and structural engineers to integrate our products into their designs.”
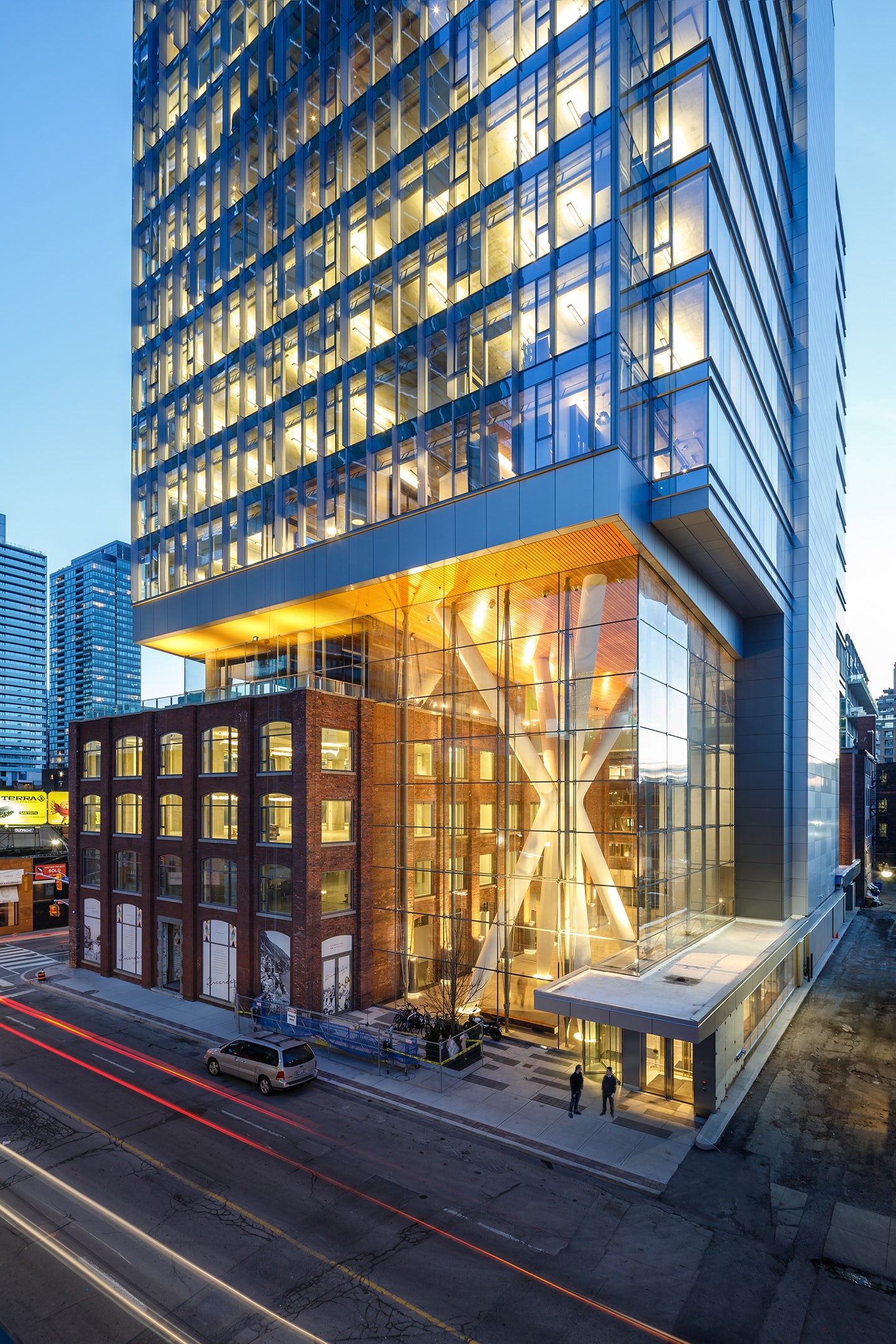
QRC West by Sweeny & Co Architects Inc.; photo by doublespace photography
He and Dr. Michael Gray, executive vice president and co-founder, spun their company off from the University of Toronto, and, as a result, its technology is firmly grounded in academic research. “We have been designing and destroying full-scale steel castings in the lab for nearly 15 years — first as part of our master’s and doctoral work and after via Cast Connex’s research and development initiatives,” he explains. “That experience, as related to casting use in building structures, is quite unique in the world.”
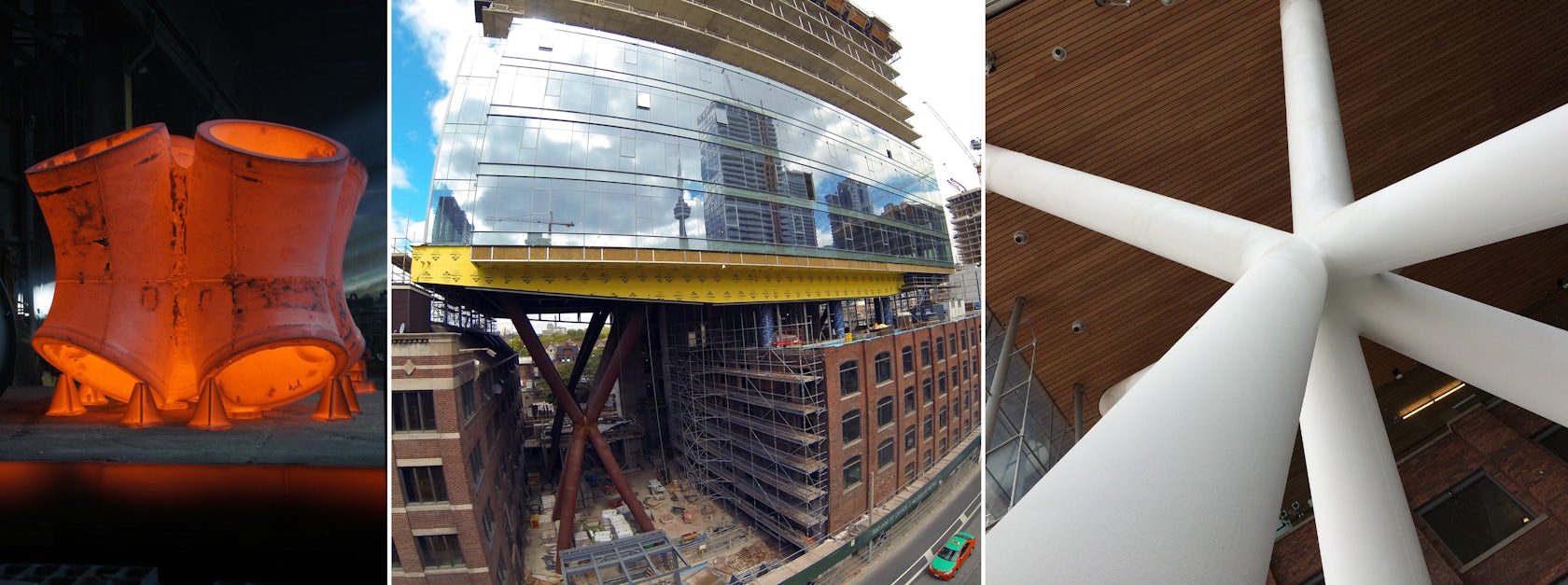
QRC West by Sweeny & Co Architects Inc.
One of the first buildings to leverage the steel casting manufacturing technique was the Centre Georges Pompidou in Paris, designed in 1971 by then-unknown Renzo Piano and Richard Rogers. It was considered a groundbreaking use of the technology, and it quickly resulted in a growing demand for steel castings in architecture across Europe and Asia — and now in North America.
Piano and Rogers have gone on to use castings often in their practice, with Piano recently collaborating with Cast Connex on his Whitney Museum of American Art, which opened last year in New York City. The project employs the company’s standardized Universal Pin Connectors in the building’s feature X-braces, which appear to float in the air thanks to Piano’s creative orientation of the connectors in the frames. Another recent New York project, this one featuring custom-designed steel castings, is the new retractable roof over Arthur Ashe Stadium at the USTA Tennis Center (home of the U.S. Open) in Flushing Meadows-Corona Park.
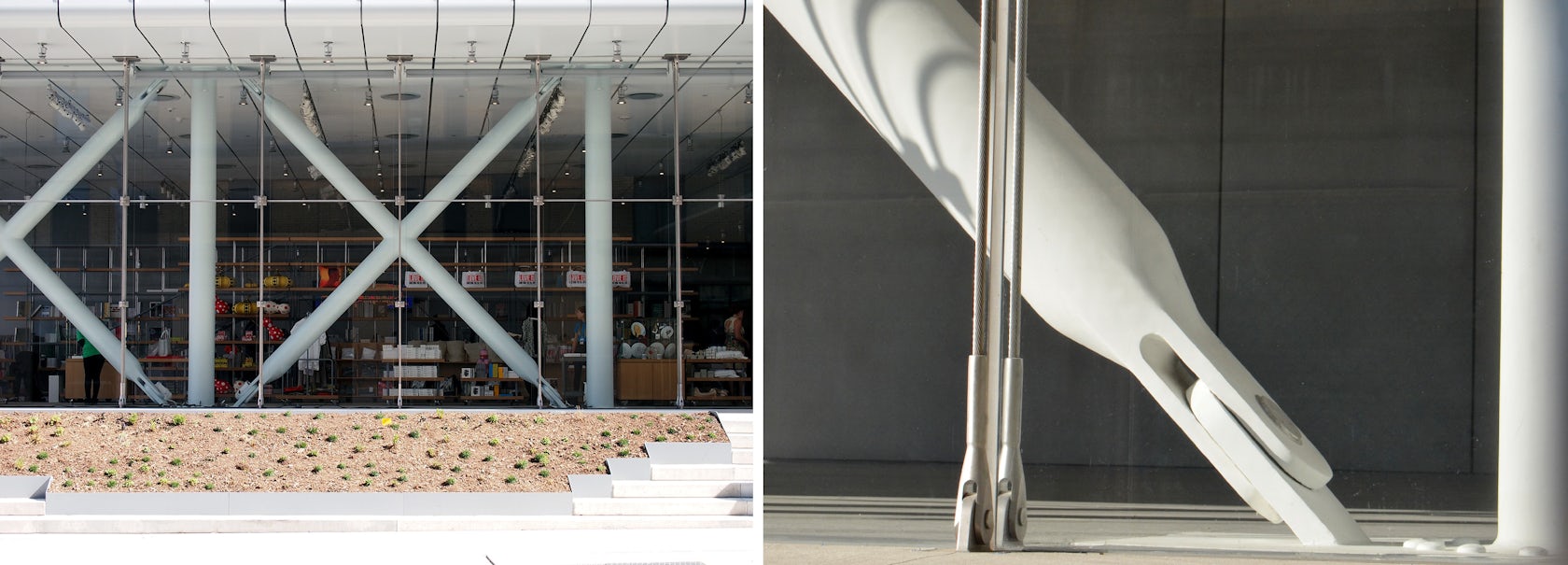
Whitney Museum of American Art by Renzo Piano Building Workshop
There, Cast Connex was engaged by Canam’s structural-heavy steel construction division to engineer and supply 16 architecturally exposed, structural steel brace-end connectors. Each of the 3.9-ton cast steel connectors was used at the bottom-side brace connection for the 38-inch-diameter steel braces that support the entirety of the new roof above Ashe stadium. Working closely with the project’s architects, Rossetti, Cast Connex developed the connectors’ shapes to meet the architect’s vision while meeting the stringent structural requirements.
In yet another high-profile project, Cast Connex was engaged to provide engineering and administrative services for the architecturally exposed structural cast steel nodes in the Transbay Transit Center in San Francisco designed by Pelli Clarke Pelli Architects. The project utilizes more than 300 custom cast steel components ranging in weight from 5,000 pounds to 45,000 pounds each. The cast steel nodes required for this development are critical elements of both the gravity- and earthquake-resisting systems of the transit center and are of critical architectural significance. Cast nodes are also featured heavily in the building’s “Light Column,” one of the terminal’s main architectural features.
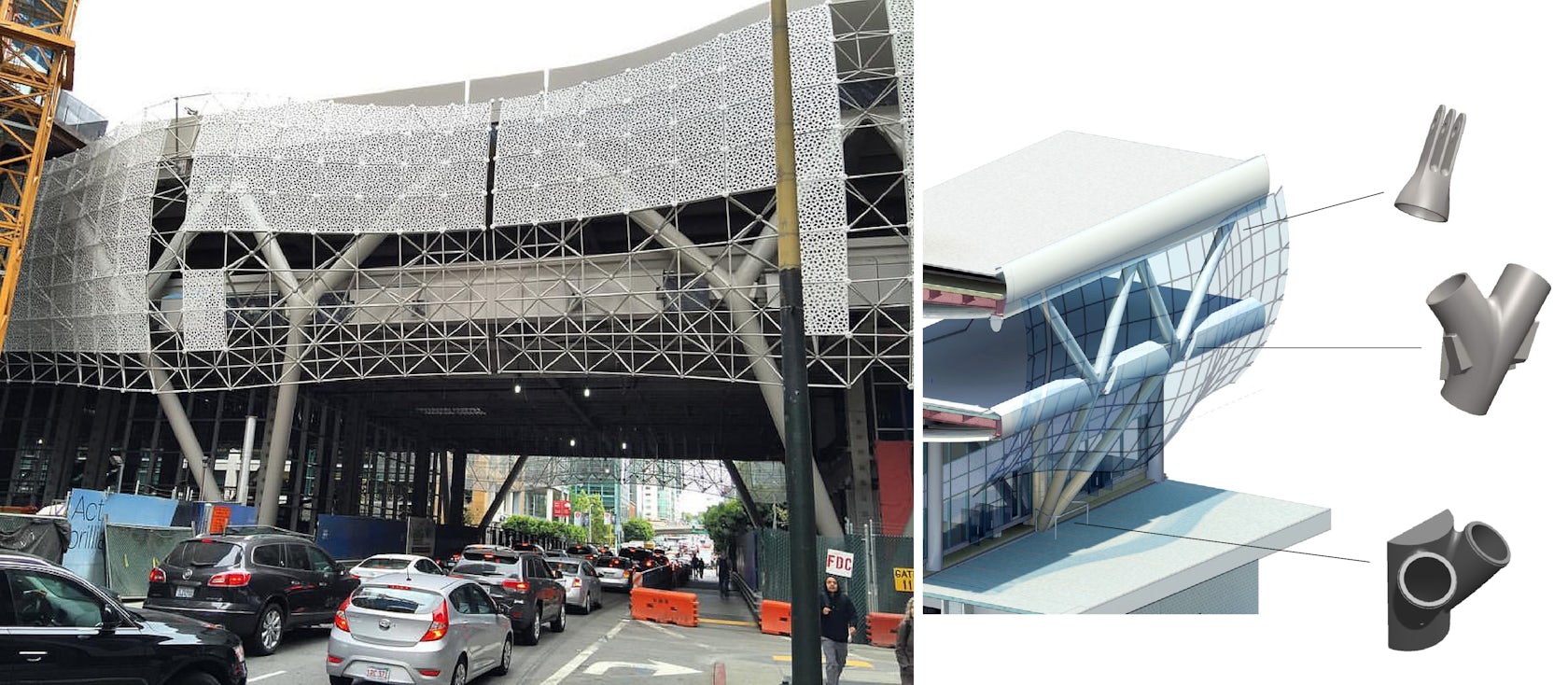
Transbay Transit Center by Pelli Clarke Pelli Architects
The firm’s components are not just for steel buildings, but can be used in concrete and wood structures, too. Steel castings can be designed to carry gravity, wind and earthquake loading, all the while enhancing structural aesthetics. “Steel casting manufacturing is similar to 3D printing in its geometric capabilities; the primary difference being that casting manufacturing is available today and has been vetted and used in many projects,” Oliveira says. “We make tooling using CNC manufacturing, make the molds from sand, pour molten steel into the molds and can thereby create virtually any practical geometry in sound structural steel.”
While many of the firm’s collaborations leveraging custom castings are related to high-end projects, they commonly take on smaller projects like libraries and community centers — even residential projects — when designers leverage their standardized, off-the-shelf, pre-engineered products.
“Our standardized products are used in every type of building you can imagine,” he says. “From stadiums, arenas and airports to custom homes.”
Cast Connex is the industry leader in the use of cast steel structural components in the design and construction of building and bridge structures. Its products include pre-engineered connectors that simplify the design and enhance the performances of structures. The company also offers design-build services for custom cast steel nodes and components.
To learn more about the company and its products, visit them on Architizer or on their website at castconnex.com.