4300 Wilson– A series of dramatic, research-supported moves propel a once-vanilla building out of precast anonymity and into the lead role in an emerging urban corridor. 4300 Wilson serves as an exemplary model of a repositioning. It helps to redefine the Ballston, Va., market through a unique amenity experience, enticing both visitors and future tenants into a completely novel workplace journey.
Architizer chatted with Mariela Buendia-Corrochano,
Architizer: What inspired the initial concept for your design?
Mariela Buendia-Corrochano (: As a mid-rise office building located in a somewhat suburban Northern Virginia setting, 4300 Wilson Boulevard needed street presence and a defining character to stand out. Our team was tasked with helping the building’s tenants attract talented young workers by enlivening 4300’s amenity spaces and enhancing the building experience. In doing so, the effort would also help reshape the fabric of Northern Virginia’s Ballston corridor — which is aiming to become more urbanized — by creating buzz in the marketplace.
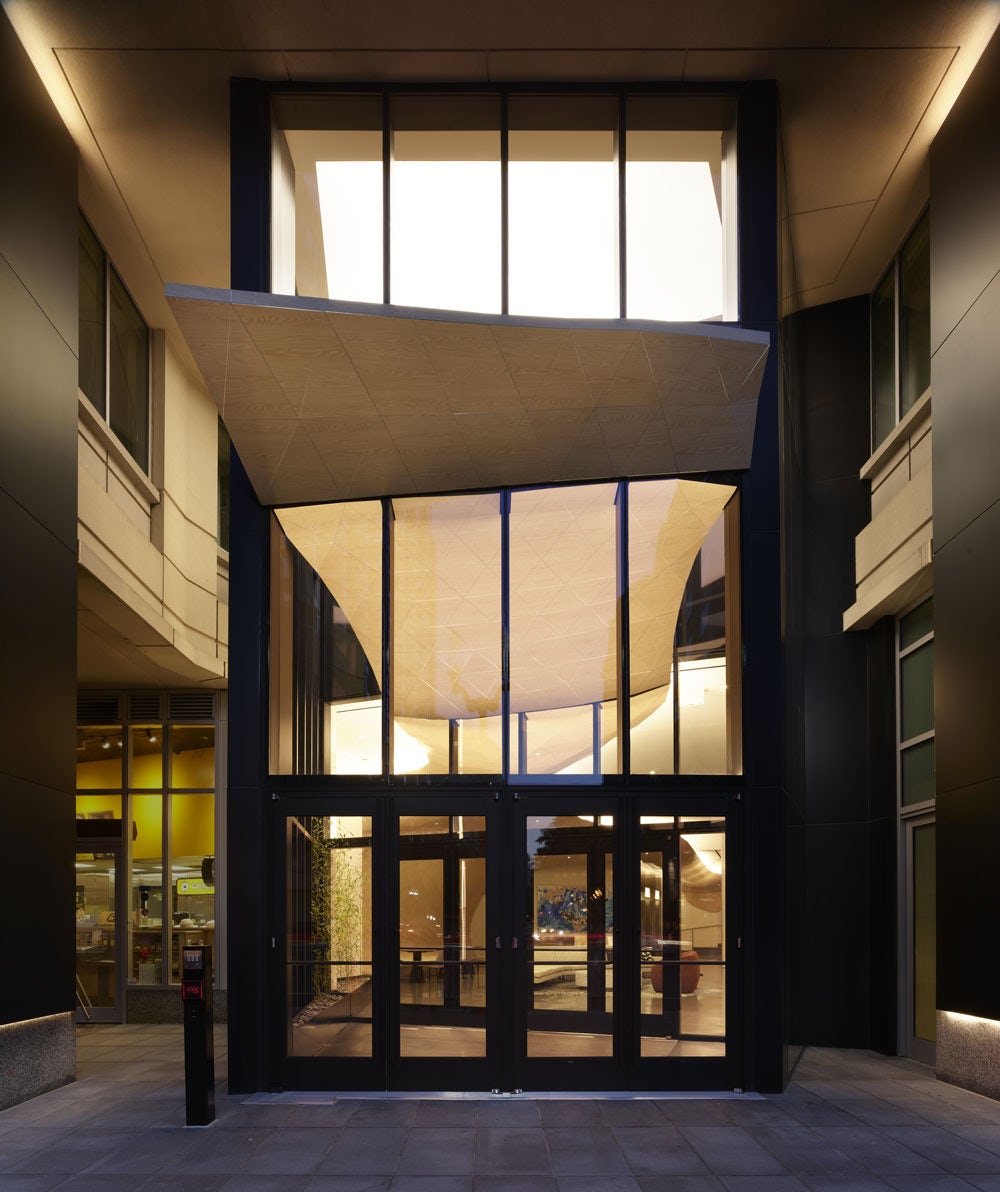
© James John Jetel
Giulio Masotti (WOOD-SKIN): WOOD-SKIN enables teams from all over the world to bring to life and to the indoors those very shapes that nature has mastered for millions of years, forms, and functions that today’s technologies are not yet capable of building efficiently. We work as an extension of the firm’s team, in this case, the initial concept has been developed by the Gensler Team; WOOD-SKIN participated in the early stage of the design by re-modeling suggestions from the original concept and engineering such suggestions with our bio-mimicry knowledge and software. Together, the two firms found the perfect balance between the initial intent, its feasibility, and the exploitation of WOOD-SKIN technology which allows for these amazing creations to be built efficiently.
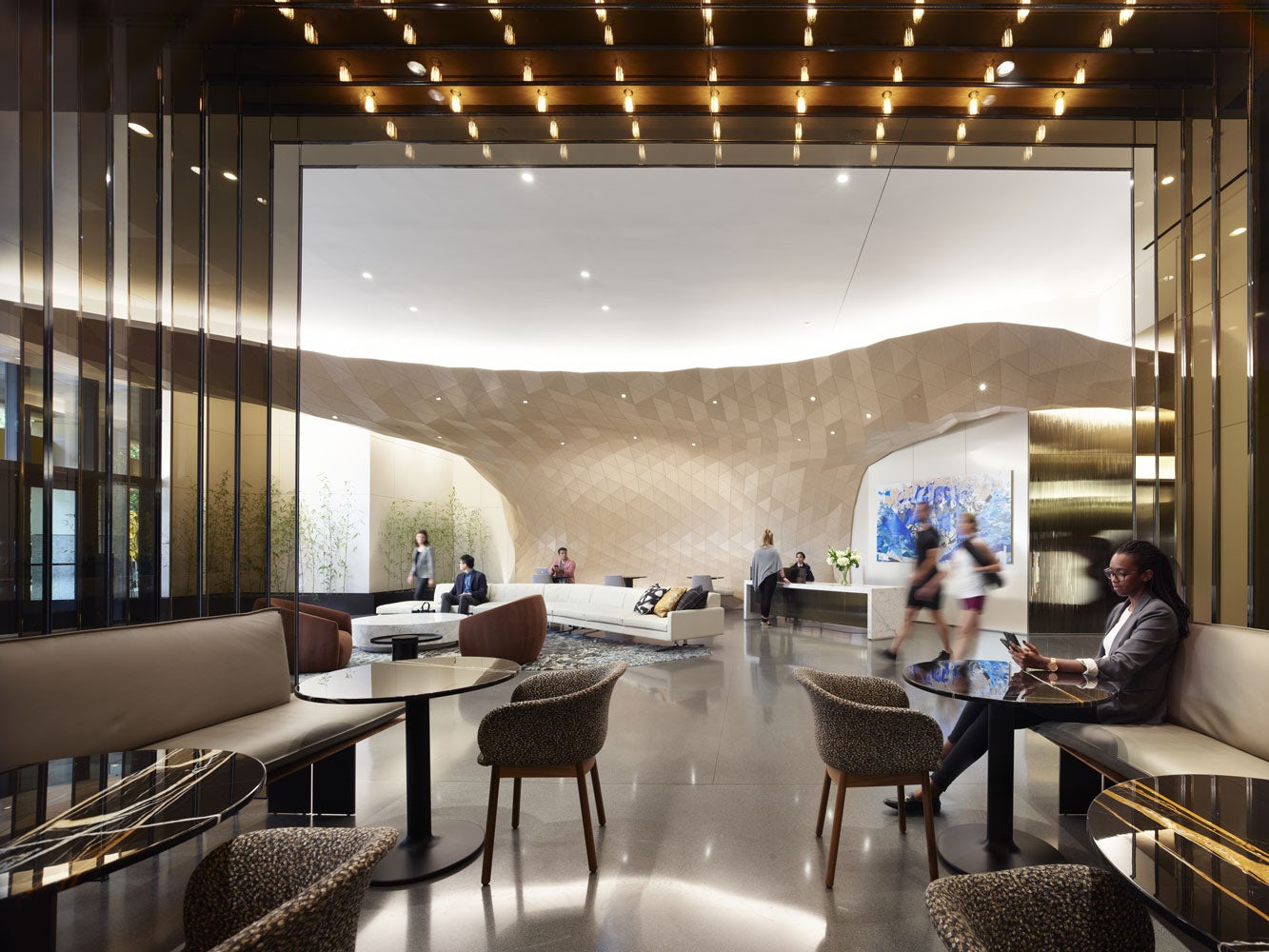
© James John Jetel
What do you believe is the most unique or ‘standout’ component of the project?
Mariela Buendia-Corrochano (: A semi-organic, sculptural feature overhead invites the visitor into the space through the entryway and continues once inside, touching down within the reception area as a bench feature adjacent to the front desk. This element breaks up the previously wide-open corridor and gives the lobby a sense of place with a connection leading all the way to the elevator and amenity space.
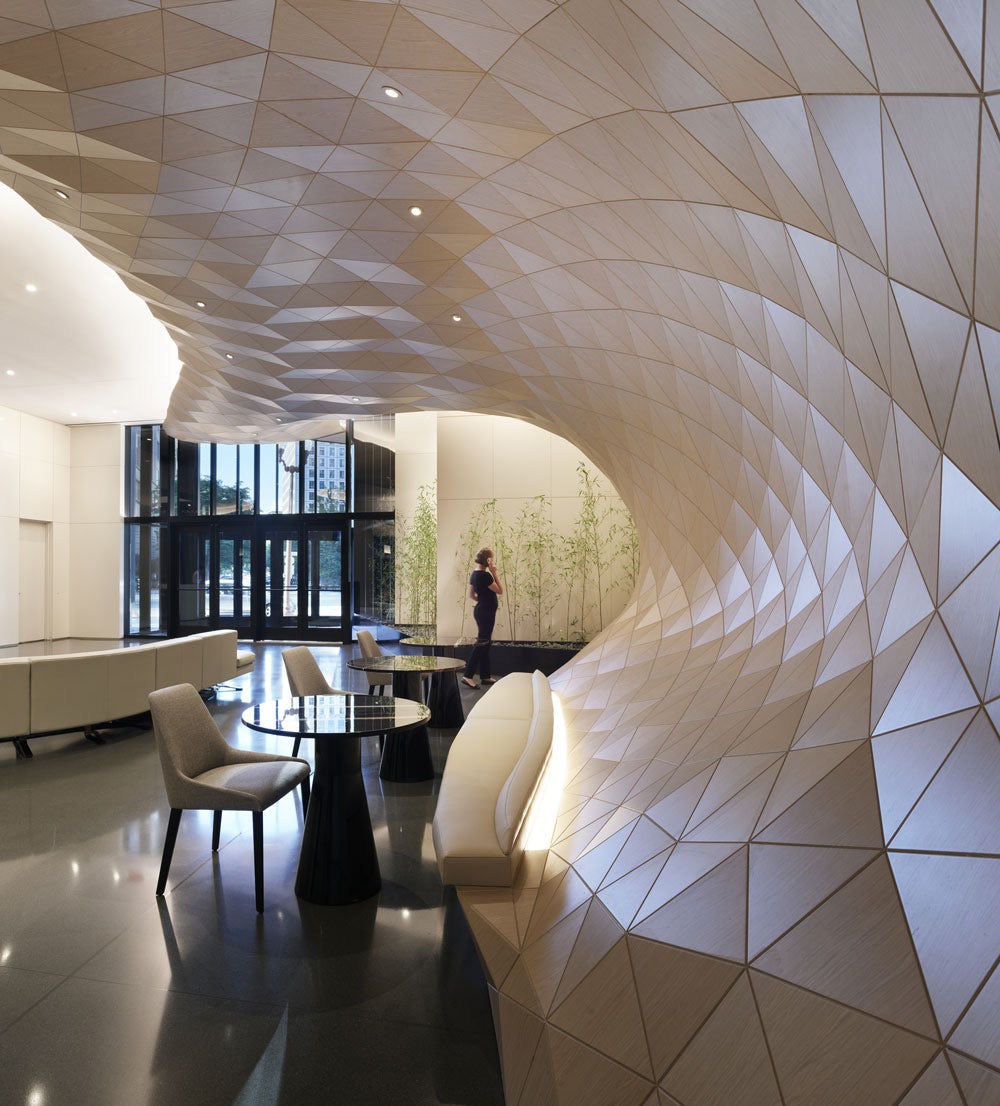
© James John Jetel
What was the greatest design challenge you faced during the project, and how did you navigate it?
Mariela Buendia-Corrochano (Gensler): Our challenge was to transform 4300 Wilson into a magnet for young-minded, creative collaborators. In short, a place for all the different sides of life that collide in this lively urban corridor emerging in the midst of a high-density residential area. The team made it a priority to conduct walking tours of the Ballston market at the project’s outset, enabling them to develop a great understanding of the local neighborhood and ultimately create a space that will suit the identity of future tenants.
Andrea Tellatin (WOOD-SKIN): As with all great and forward-thinking projects, challenges were at its core. This is the very reason WOOD-SKIN started its entrepreneurial journey, as designers and engineers we have experienced the pain and challenges of creating complex shapes and next-level acoustic surfaces before finding a solution. To name a few, maintaining the correct veneer alignment along the whole element is a usual challenge that we solved by implementing custom scripts and techniques for subdividing the surface into smaller clusters for their manufacturing. The maximal material optimization had to be taken into consideration too as a value engineering and sustainability factor. Moreover, all the hidden supporting structures had to be designed and engineered from scratch. The error tolerance allowed was utterly low, but thanks to the HITT team and laser-scan technologies, funneled into our parametric process, all major deviations between project drawings and as-built conditions were rapidly incorporated into the CAD 3D model, from which all information was retrievable (unrolling the geometry for flat-sheet CNC manufacturing, substructures, hanging points, lighting predispositions, etc).
How did the context of your project — environmental, social or cultural — influence your design?
Mariela Buendia-Corrochano (Gensler): At the project’s outset, the design team prioritized touring the surrounding Ballston market to deepen their understanding of the local community and create a space that will suit the identity of future tenants and their employees. Wanting to encourage a sense of community, the design team commissioned local artists to create murals for the connection point between the fitness center and conference area, integrating the community feel into the hospitality-like atmosphere created by the entry and lobby spaces.
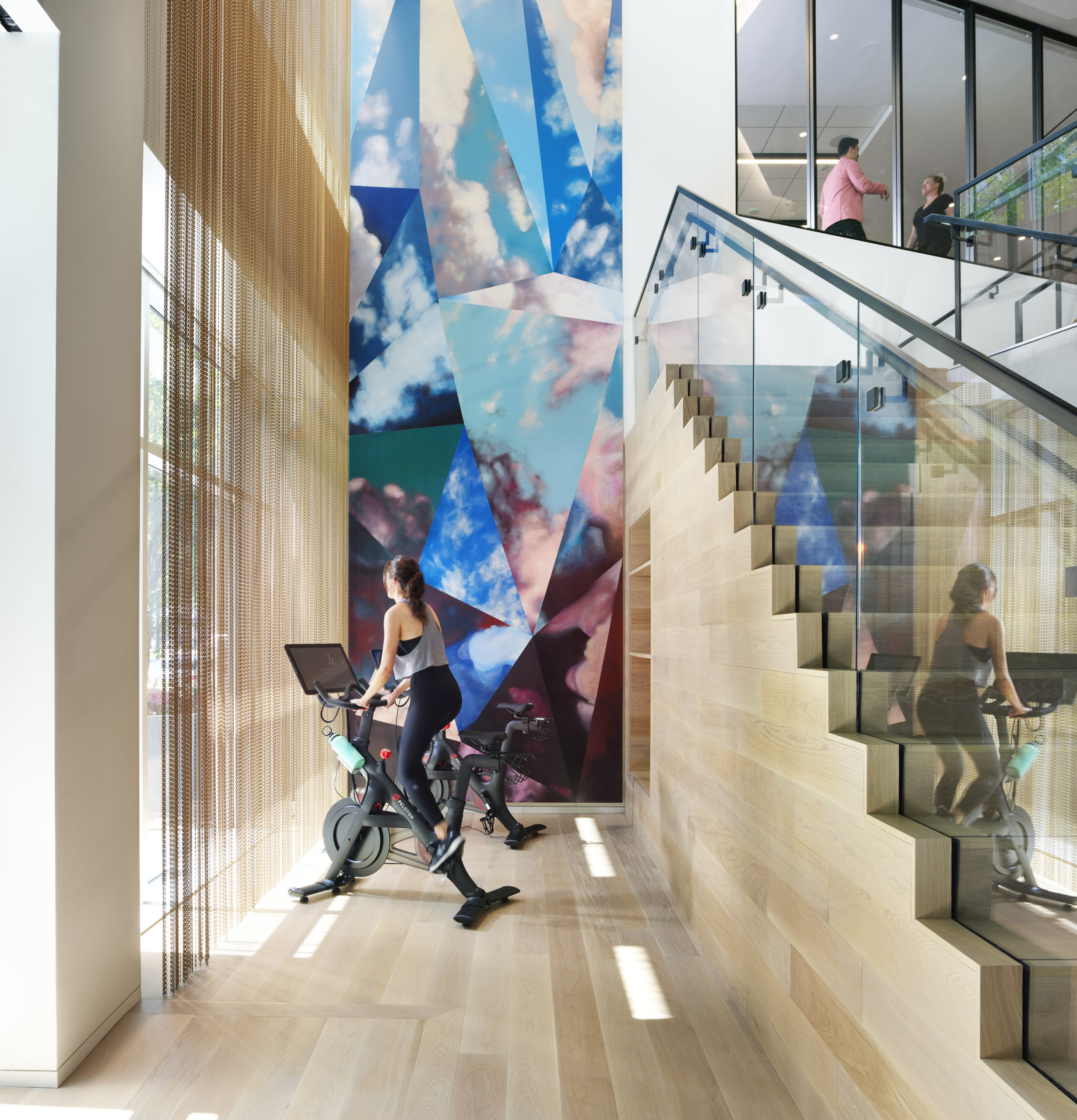
James John Jetel
Giulio Masotti (WOOD-SKIN): As an international team of designers based in Milan, Italy, we were keen to integrate our unique workflow into someone else project management style. We intend to offer our expertise and technology as a plug-in that firms can switch on when in need of a one-stop-shop solution for complex surfaces. Still, it is always a challenge to adapt and interact with international teams, especially during a pandemic. Let’s not forget this project was conceived and delivered during the pandemic. The bright side is that it stressed testing the limits of a truly file-to-machine approach where all parties involved work remotely. On the practical side, even the installation was carried out by a local contractor that seamlessly coordinated with the team remotely. A truly global effort that represents the potential and results of cutting-edge products like WOOD-SKIN, where traditional crafts from all over the world merge into a new malleable technology that can serve professionals globally. A product and a technology that carries traditions into the digital era to evolve them instead of abandoning them. Inlays, glass blowing, traditional carpentry, and so on… all coming together, digitalized to speak seamlessly with today’s design practices.
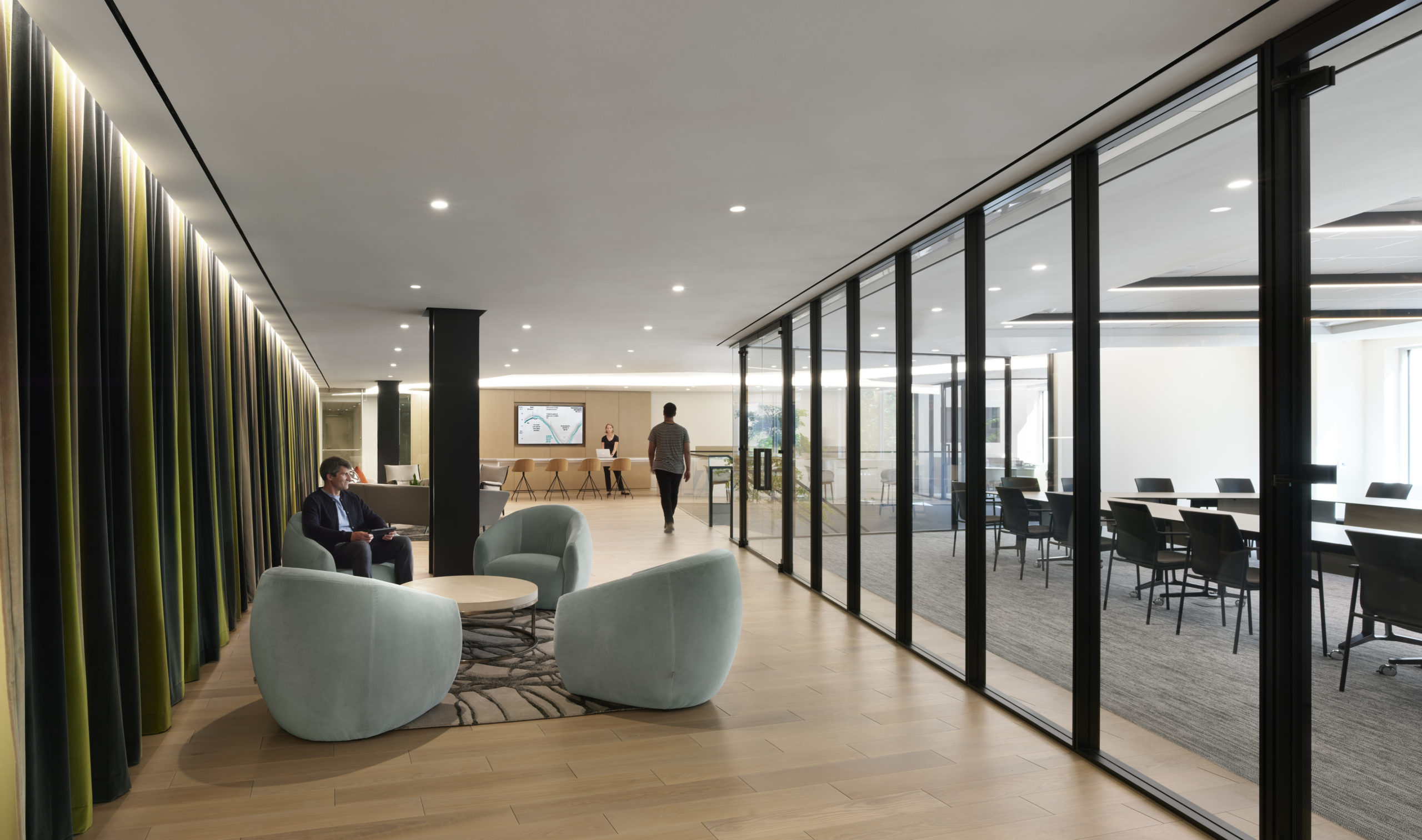
James John Jetel
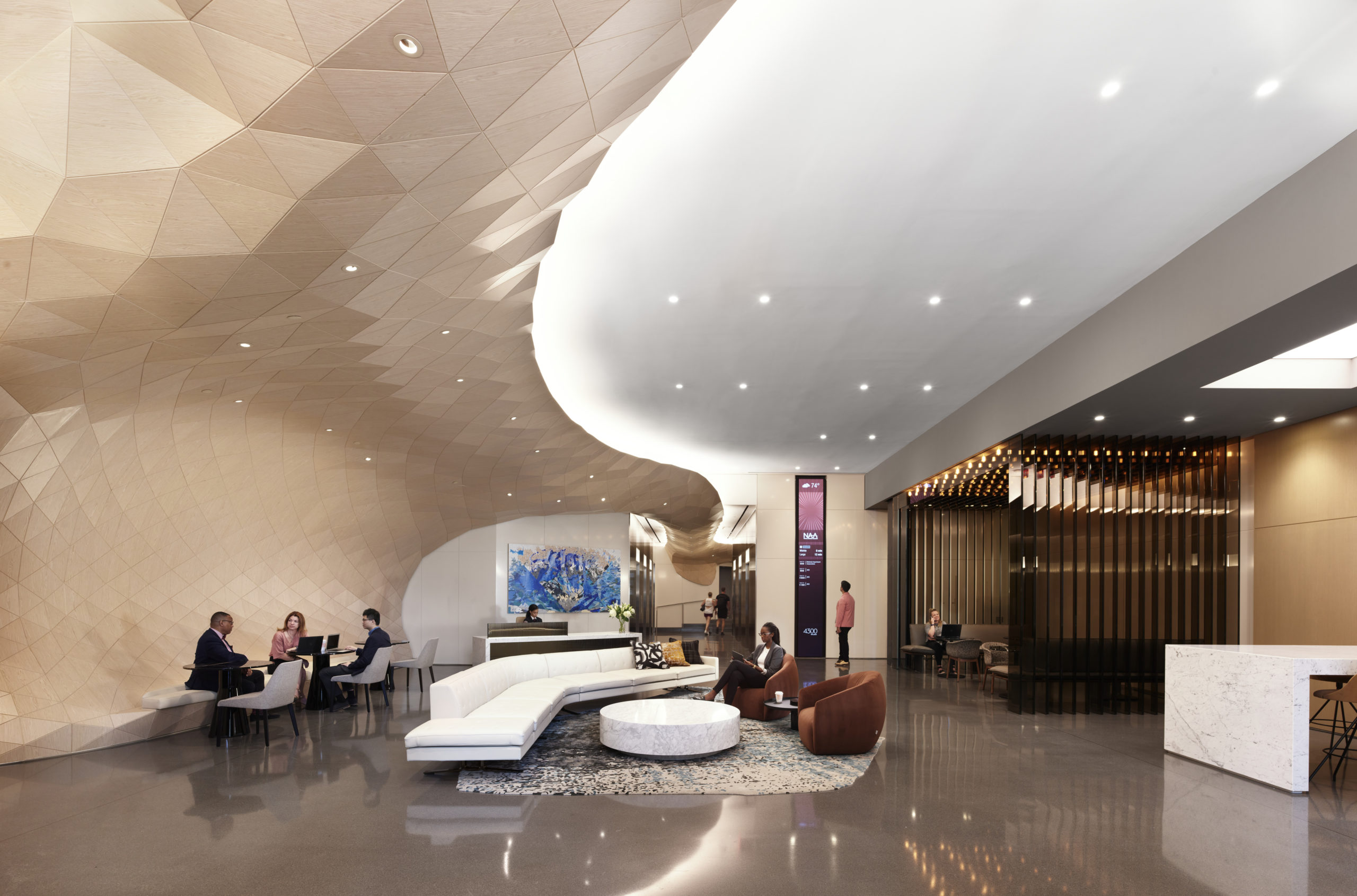
James John Jetel
What drove the selection of materials used in the project?
Mariela Buendia-Corrochano (Gensler): Using a non-linear design process, the design team was able to focus on creating a design narrative through an exploratory process of drawings, model-making, and 2-dimensional concepts. A semi-organic, sculptural feature overhead invites the visitor into the space through the entryway and continues once inside, touching down within the reception area as a bench feature adjacent to the front desk. A hospitality vibe is felt throughout through design and materials, including a seating area with a jewel box effect and a sliding partition that leads into a retail space.
Andrea Tellatin (WOOD-SKIN): The selection was made in the end by the Gensler team, we have worked alongside the firm and provided curated various material composite solutions, where aesthetics, durability, maintenance, stability, sustainability, and cost all went into consideration.
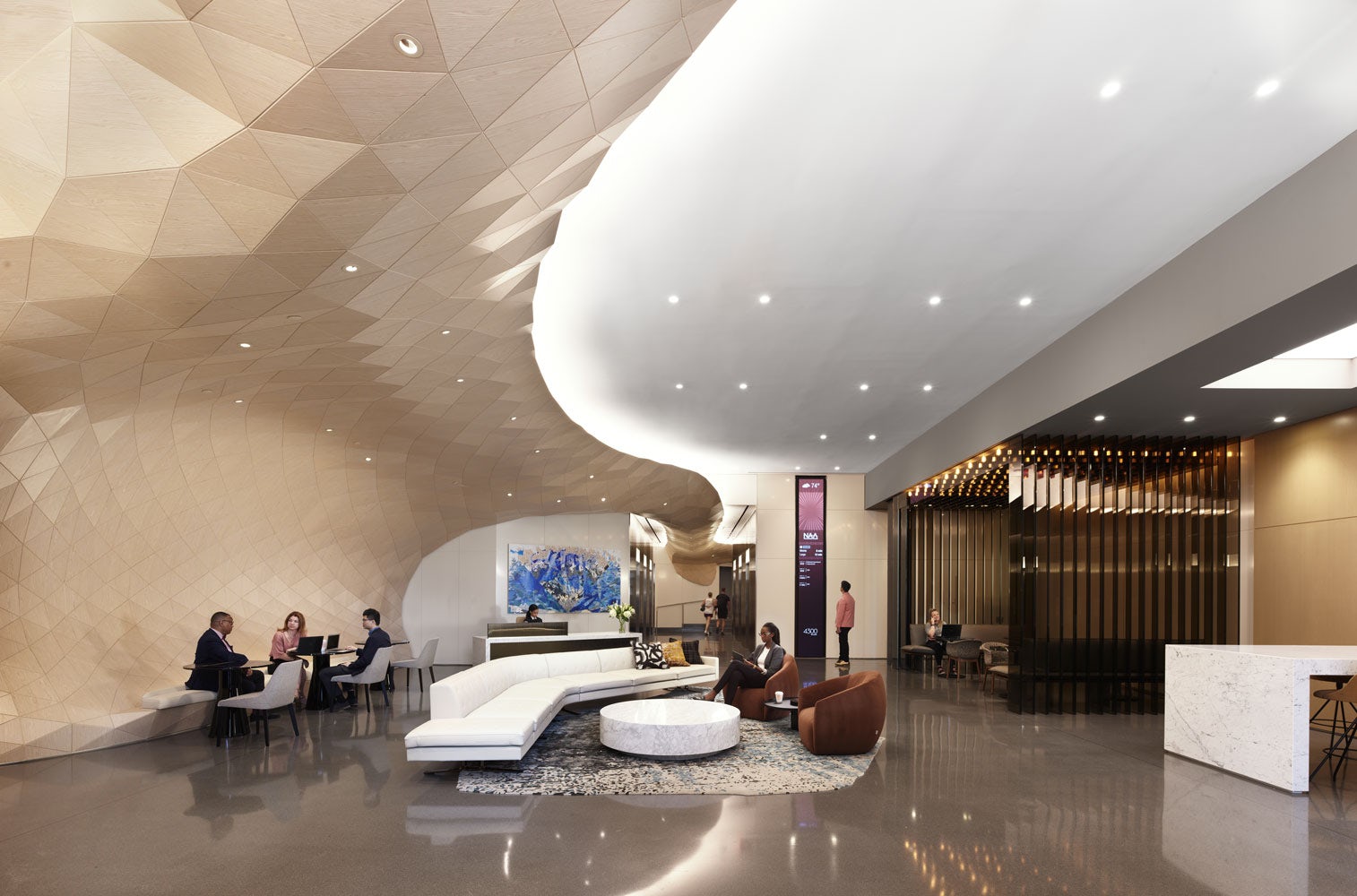
© James John Jetel
What is your favorite detail in the project and why?
Andrea Tellatin (WOOD-SKIN): My favorite detail is the large-scale plasticity that wood earns in this project. The union of the grained wood finish with the wave-like free-form aspect of the whole shape makes for a perfect combination of nature and technology.
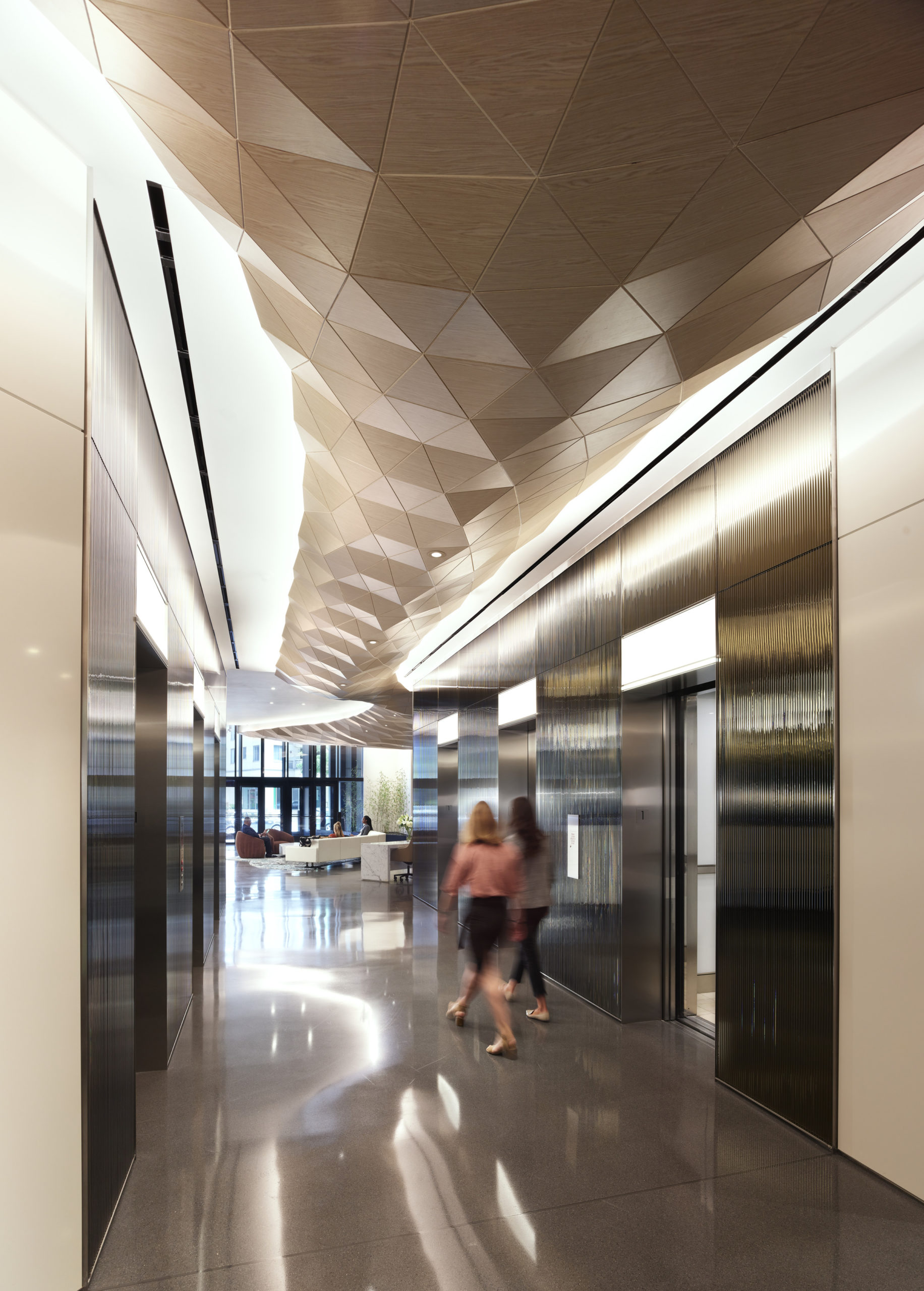
James John Jetel
How important was sustainability as a design criteria as you worked on this project?
Mariela Buendia-Corrochano (Gensler): As a repositioning project, there is an inherent resilience component–the idea of bringing new life to a tired building through a strategic intervention rather than a larger reskin or even new building.
Andrea Tellatin (WOOD-SKIN): It surely was for Gensler in the first place and this is one of the reasons they specified WOOD-SKIN as the material and solution for the project. On our end, in all the work we do, sustainability is at the heart of the process. Our technology allows the optimization of the necessary material quantities for manufacturing and the reduction of scrap material thanks to the intelligent nesting solutions we apply. Moreover, all wood-based materials we use come from strictly FSC-certified facilities and suppliers. In addition, we are constantly analyzing the market proposal in the search of the best sustainable materials, whether fully recyclable or coming from environmentally responsible realities.
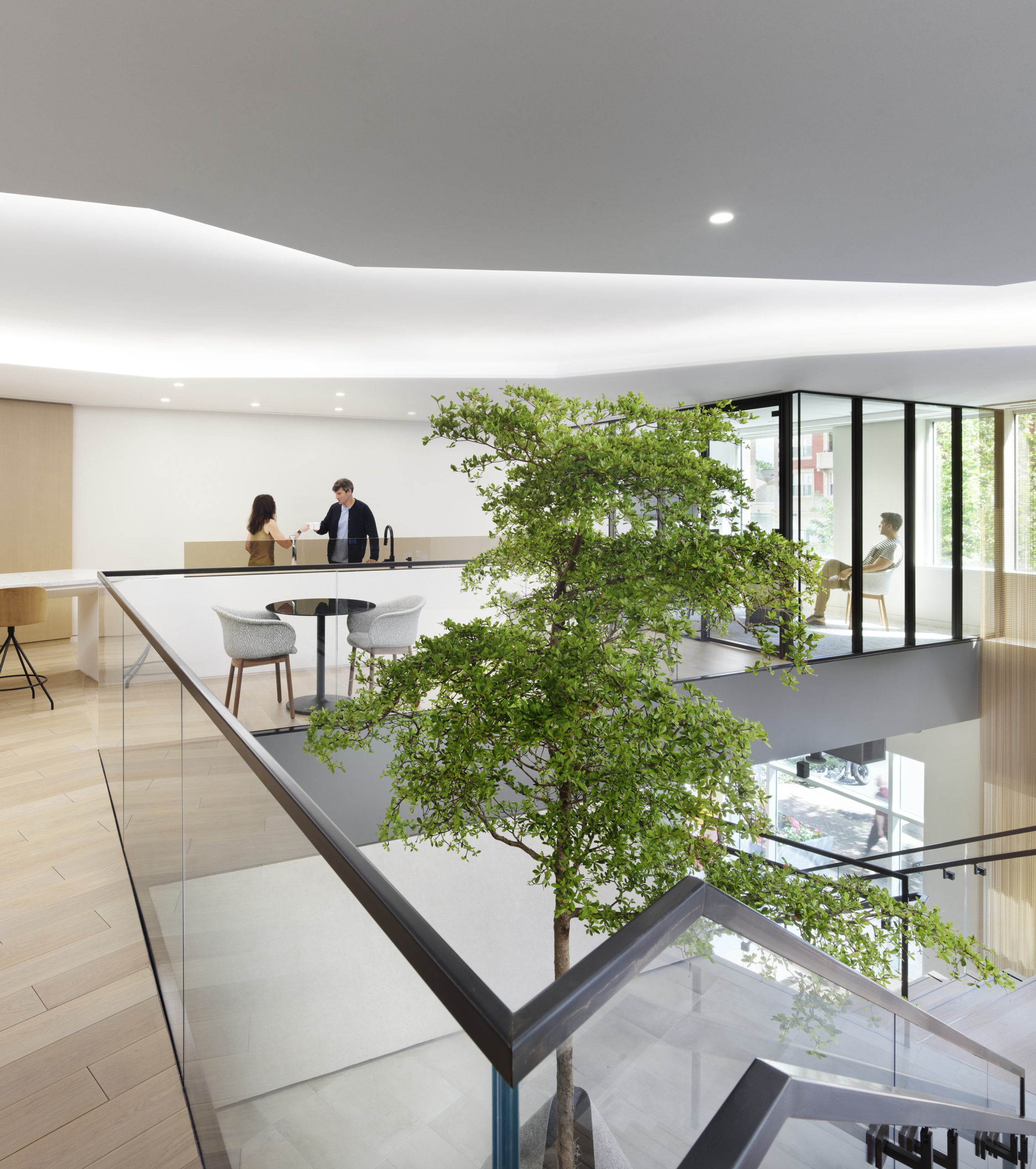
James John Jetel
In what ways did you collaborate with others, and how did that add value to the project?
Mariela Buendia-Corrochano (Gensler): The project was incredibly collaborative–from the project team and partners to the community engagement to ensure the building met the needs of the neighborhood and users.
Andrea Tellatin (WOOD-SKIN): I was in the position of leading the internal design & engineering team at WOOD-SKIN, coming up with technical and aesthetic solutions, guiding each challenge we faced to the best possible outcome, and, along with my colleagues, kept constant and active communication with architects, the GC, and each stakeholder, in order to make the whole process as smooth and efficient as possible.
Collaboration was the key to this wonderful experience since all major and minor details had to be shared and coordinated thoroughly; doing this way, it’s been a win-win for everybody involved, and the final piece installation went like a breeze.
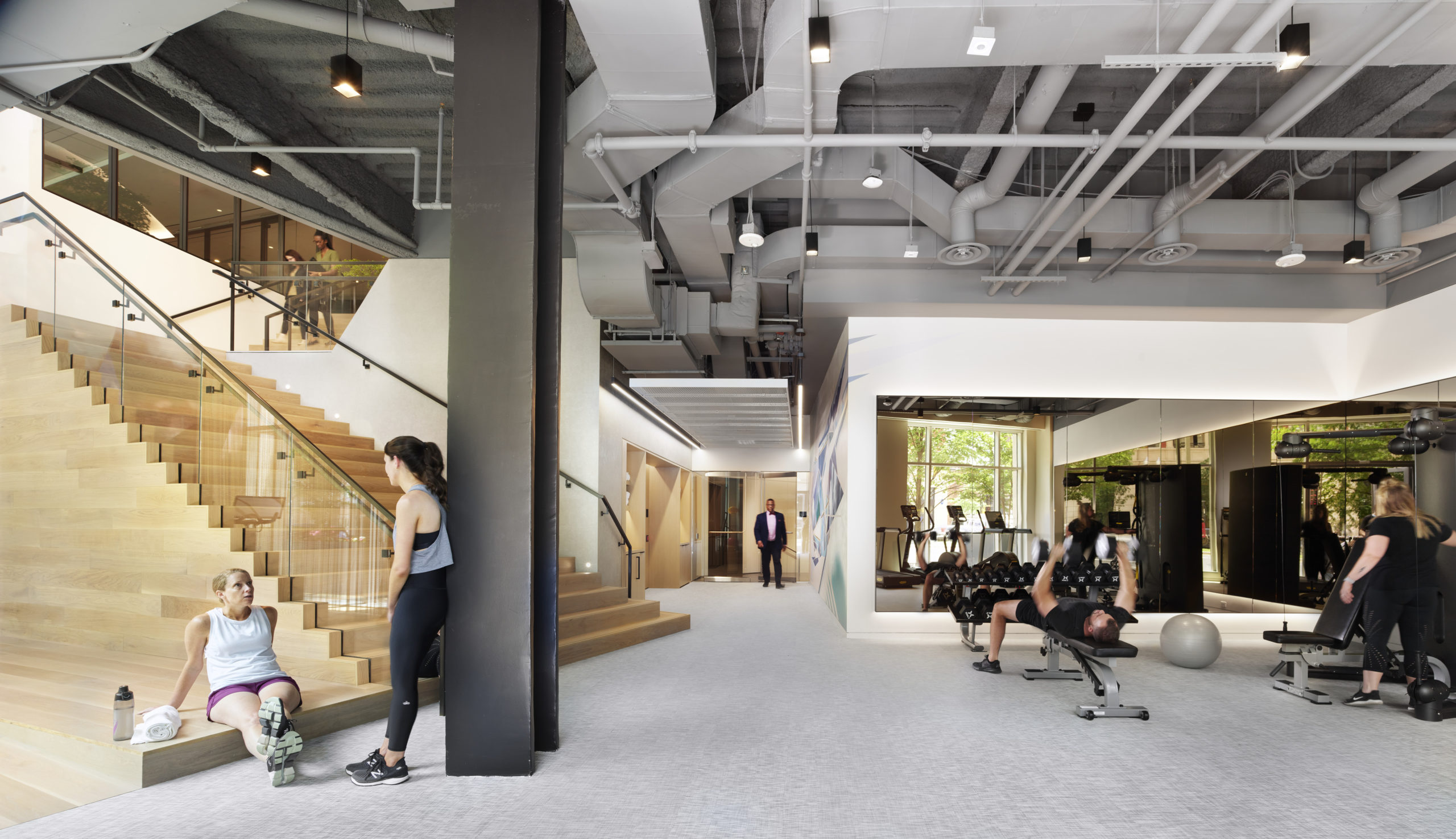
James John Jetel
How have your clients responded to the finished project?
Andrea Tellatin (WOOD-SKIN): I am happy to say that all stakeholders involved in the project were truly amazed. In a recent interview within Gensler’s podcast, Robert Pinkard, Founder and Principal at The Pinkard Group said “When we said hospitality we didn’t think Gensler would go as far as they did”.
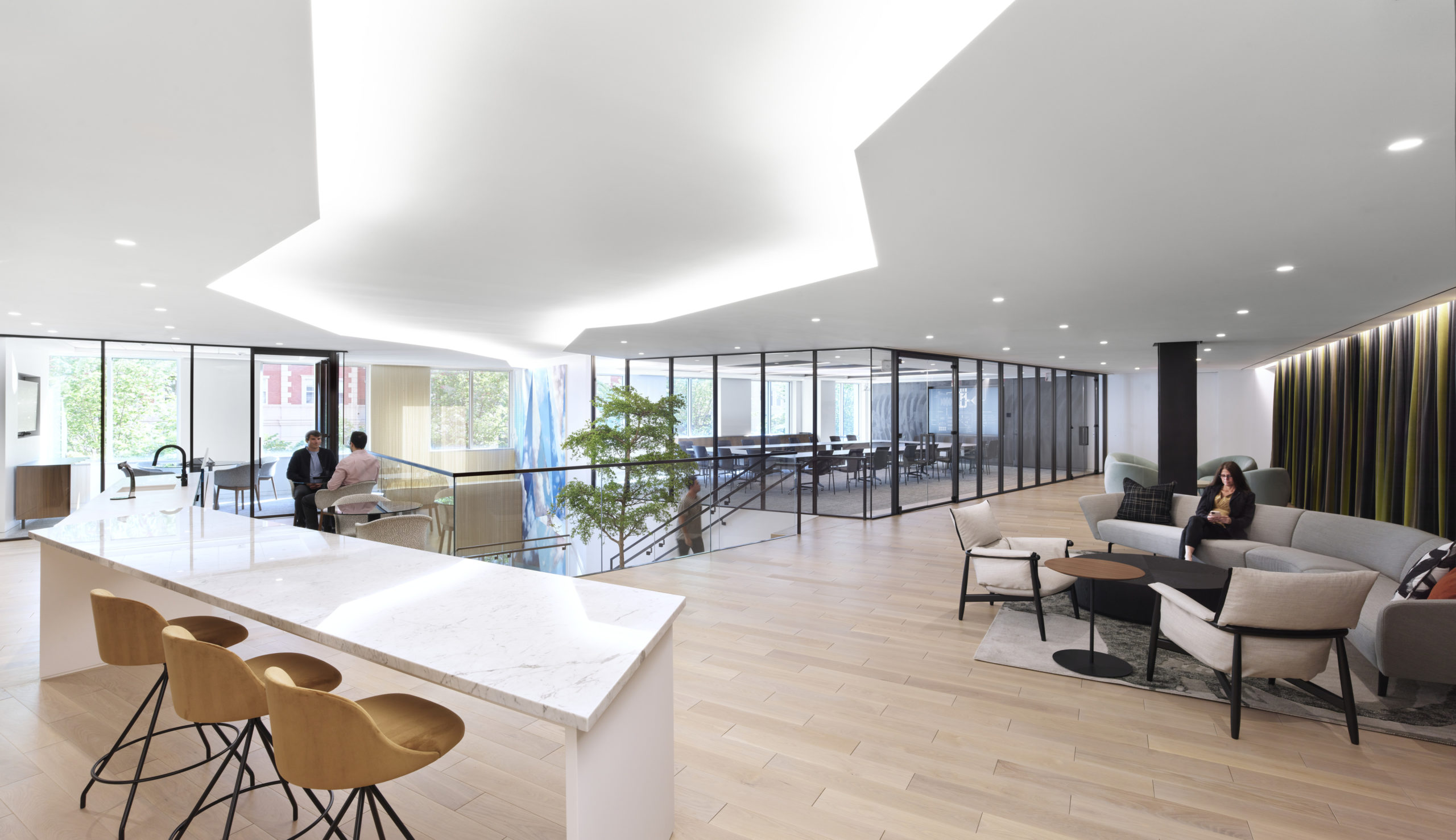
James John Jetel
How do you believe this project represents you or your firm as a whole?
Mariela Buendia-Corrochano (Gensler): Design excellence was at the heart of this project–infusing fresh design into a tired building, breathing new life into the space.
Andrea Tellatin (WOOD-SKIN): I may sound repetitive here, but this project is really the perfect example of what can be achieved with the WOOD-SKIN® technology: its key purpose is precisely to allow for these wonderful innovations, both in shape and function, to be brought to life, bridging the gap between digital representation and the built environment. Allowing the complexity that is increasingly easy to design with software to be built fast and cost-effectively, truly represents the paradigm shift of industry 4.0 and the file-to-machine workflows.
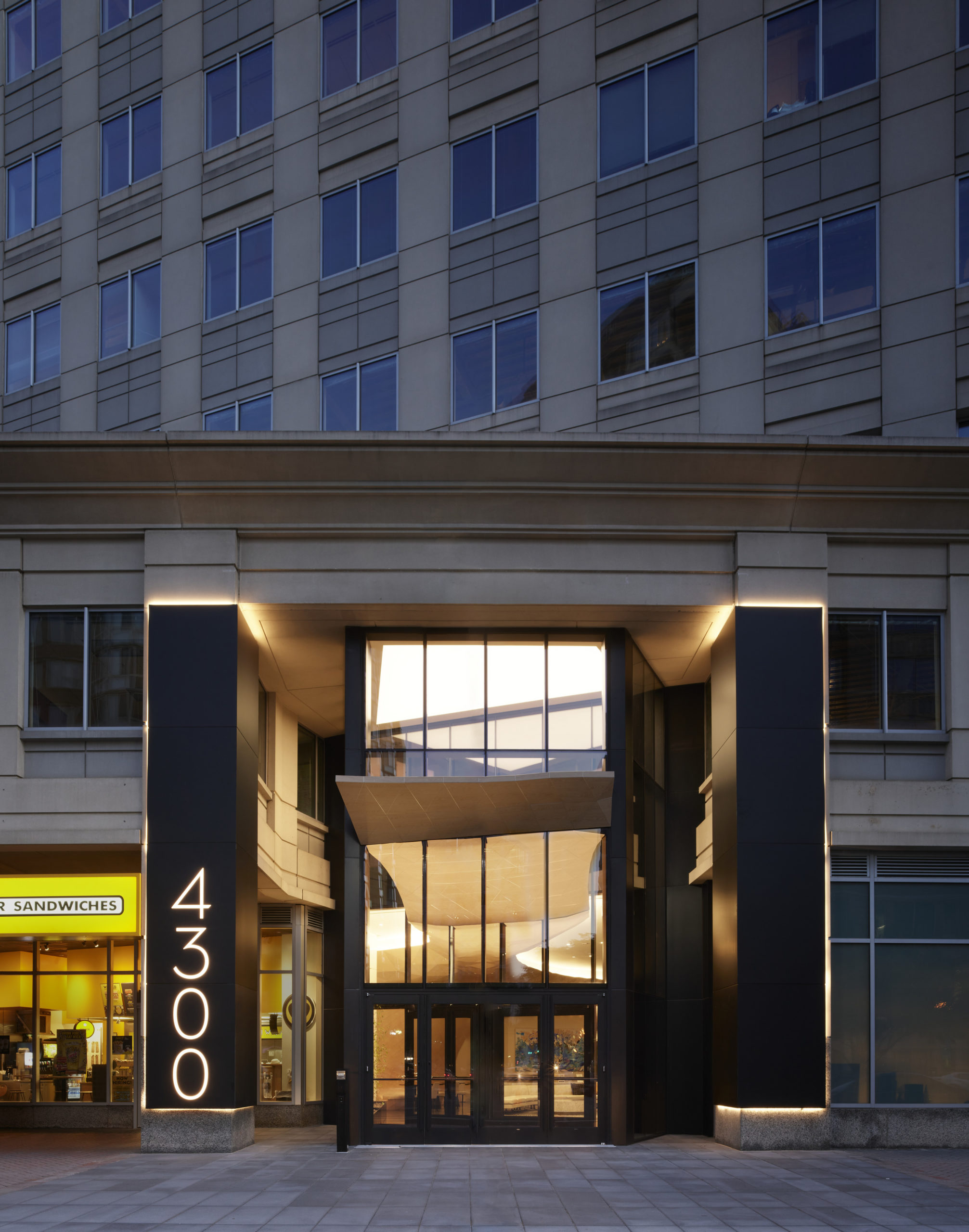
James John Jetel
How do you imagine this project influencing your work in the future?
Credits
DESIGN : Gensler
CONTRACT : HITT Contracting
PARTNERSHIP : Washington Woodworking
METAL SURFACE BY : pure+freeform
PHOTO CREDITS: James John Jetel
Team Members – Gensler
Kimberly Sullivan, Mariela Buendia-Corrochano, John Thomann, Kate Kirkpatrick, Michelle Denyer, Stephen Ramos, Claire Navin, Kelly Umutoni, Leah Ijjas
Team Members – WOOD-SKIN
Vera Irawan (vera@wood-skin.com), Sirio Carone (sirio@wood-skin.com), Massimo Romanato, Carol Sichel (carol@wood-skin.com)
Consultants
HITT Contracting, Cerami & Associates, Girard Engineering, Lighting Workshop, SK&A Associates, LandDesign, Washington Woodworking
Products / Materials
WOOD-SKIN® – 3D PARAMETRIC SURFACE Pure+freeform – aluminum surface
For more on 4300 Wilson, please visit the in-depth project page on Architizer.