Architects: Want to have your project featured? Showcase your work through Architizer and sign up for our inspirational newsletters.
Amidst the drafting tables and rolls of blueprints of the 1980s, the first whispers of computer-aided design began to emerge from those in the know. To the casual observer, they were just machines, cold, impersonal and unable to replicate the creative workflow of the skilled draftsperson. Yet to the visionary architect, CAD represented uncharted territory — a brave new world where design was limited only by your imagination, where time had been liberated from sketching and scratching. A world where changes were welcomed with the mere click of a mouse. (In hindsight, that might not have been the win we thought it was, she says, bypassing revision request nine hundred and sixty-seven.)
Today, the once-revolutionary CAD is ubiquitous, the cornerstone of tens of thousands of design practices around the globe. The technology we all use (and love?) has paved the way for multiple new industries. Each of these blossoming industries has harnessed CAD technology in ways previously thought unimaginable, ultimately furnishing the architectural sector with tools like 3D printers, CNC machines and robots of many shapes and sizes. These technologies are fast becoming the trusted allies of architects. But where is digital fabrication headed, and can we keep up?
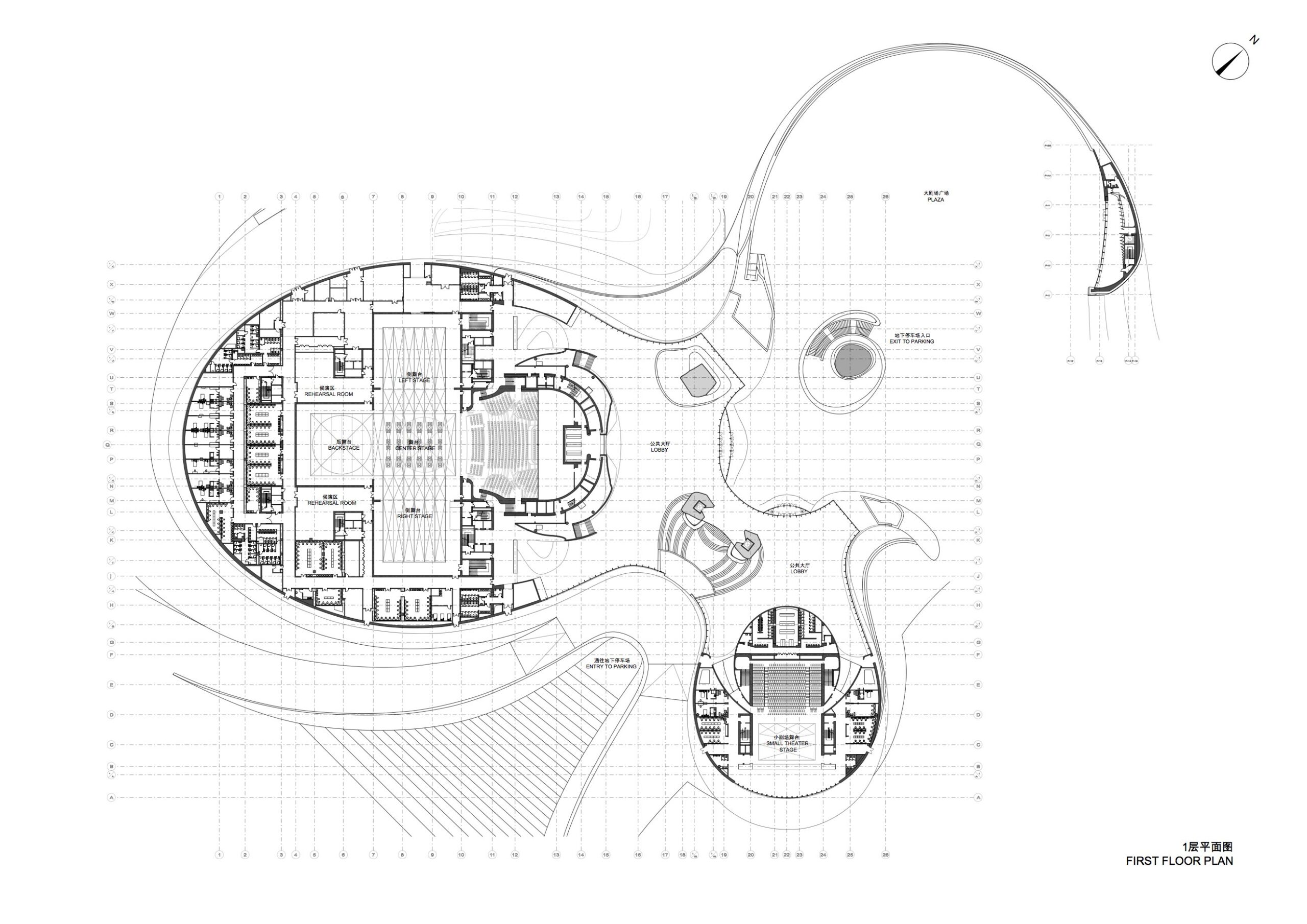
Harbin Opera House by MAD Architects, Heilongjiang, China. Designed over ten years ago, the impressive cultural landmark was, at its time, the pinnacle of architectural and engineering skill. The music venue set a benchmark for architecture moving forward. Today we can see many buildings that have been inspired by the iconic structure
Digital fabrication is a fusion of technology and creativity, where computer-controlled design and manufacturing processes are employed to transform the way architects and designers approach exploration, prototyping, mass production and construction.
Yes, it all started with CAD, but we’ve come a long way in the last forty years. Traditionally, design was passive — a designer used their knowledge and intuition to create designs with the help of a computer-aided design program to put it “on paper.” We had shifted from the drafting board to the keyboard, but the process was much the same.
However, as technology has advanced at a rate I doubt many of us can actually believe, we have moved on from the “traditional” CAD design that is restricted by the designer’s available time, resources or skill. We are no longer satisfied by this manual drafting method and its limits to the number of design options that can be considered. Architecture as a practice is becoming more advanced, and so must our tools.
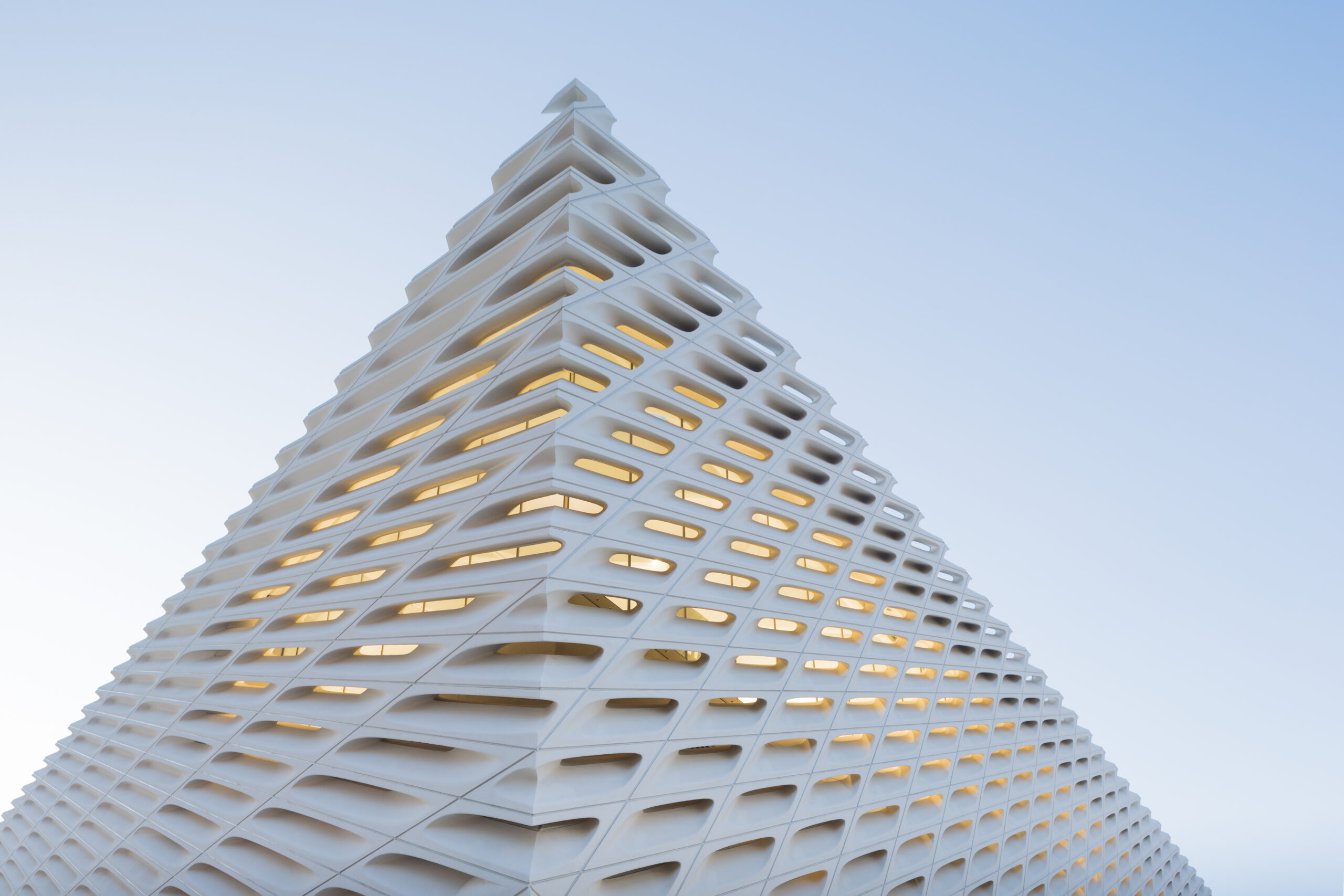
The Broad by Diller Scofidio + Renfro, Los Angeles, California, has a distinctive exterior facade made up of glass fiber-reinforced concrete panels that are supported by a steel frame, delivering a porous, white veil-like screen. The screen was designed using a computational process that generated thousands of possible design variations, which were analyzed for their performance characteristics before final selection. Photographs by Iwan Baan
Today, computational design and generative design are leading the way. These design methods use a combination of algorithms and parameters to solve design problems with advanced computer processing, allowing for many iterations and adjustments — options upon options, tests and more tests, with little time wasted. Every step of the process is translated into repeatable and replicable coded computer language. The software uses this information alongside project-specific parameters to create algorithms that generate digital models and complete design analyses, allowing designers to adjust any number of factors. Almost any feature can be adjusted and altered to optimize the design, from energy efficiency and structural integrity to materiality and aesthetics.
Computational design and generative design also allow us to break a design down into components or parts that can be duplicated, a process that aids later during a project’s manufacturing and construction phases. It is a style of designing that has revolutionized prefabrication. Computational design and generative design increase our ability to explore and push boundaries exponentially, much as the first CAD did for the draftspeople of the 80s.
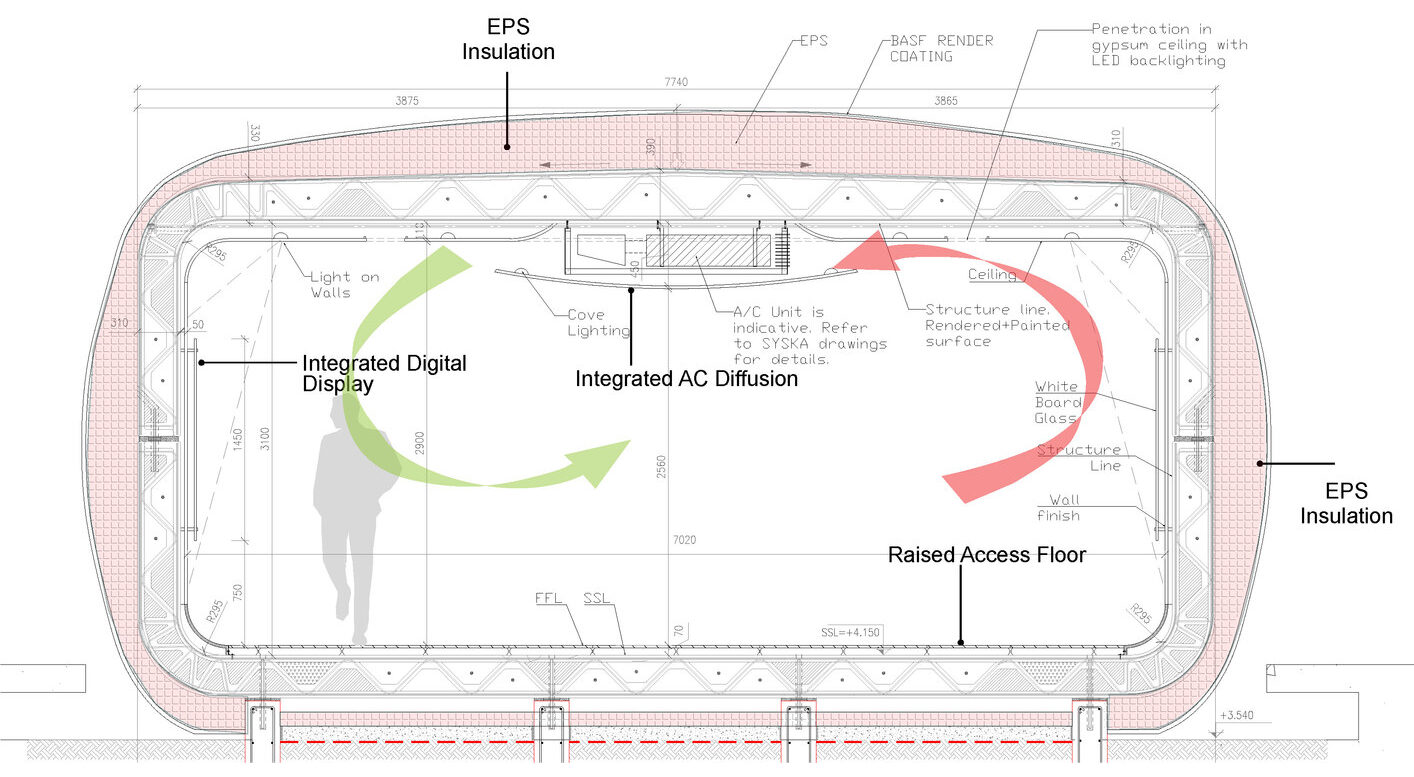
Office of the Future by Killa Design is a 3D-printed building in Dubai, United Arab Emirates. The building was constructed using a massive 3D printer, which was 20 feet tall, 120 feet long, and 40 feet wide. The printer used a special blend of concreteand the building was constructed 17 days. Photograph by WAM
There are many facets to the Digital Fabrication industry, and they typically fall into two main categories: additive and subtractive. One of the most commonly acknowledged additive styles is 3D printing. Once a niche pursuit of creatives, it fills up our newsreels from construction sites worldwide, becoming a game-changer in architectural fabrication. 3D printing is being used for many applications in architecture. On a smaller scale, it is used for models, prototypes, or to manufacture building components, but its applications are vast and growing. The ability to craft intricate designs, previously deemed too complex or costly, is now within reach as architects commission the printing of materials at the exact sizes, shapes and densities they desire. We are no longer limited by manufacturer specifications.
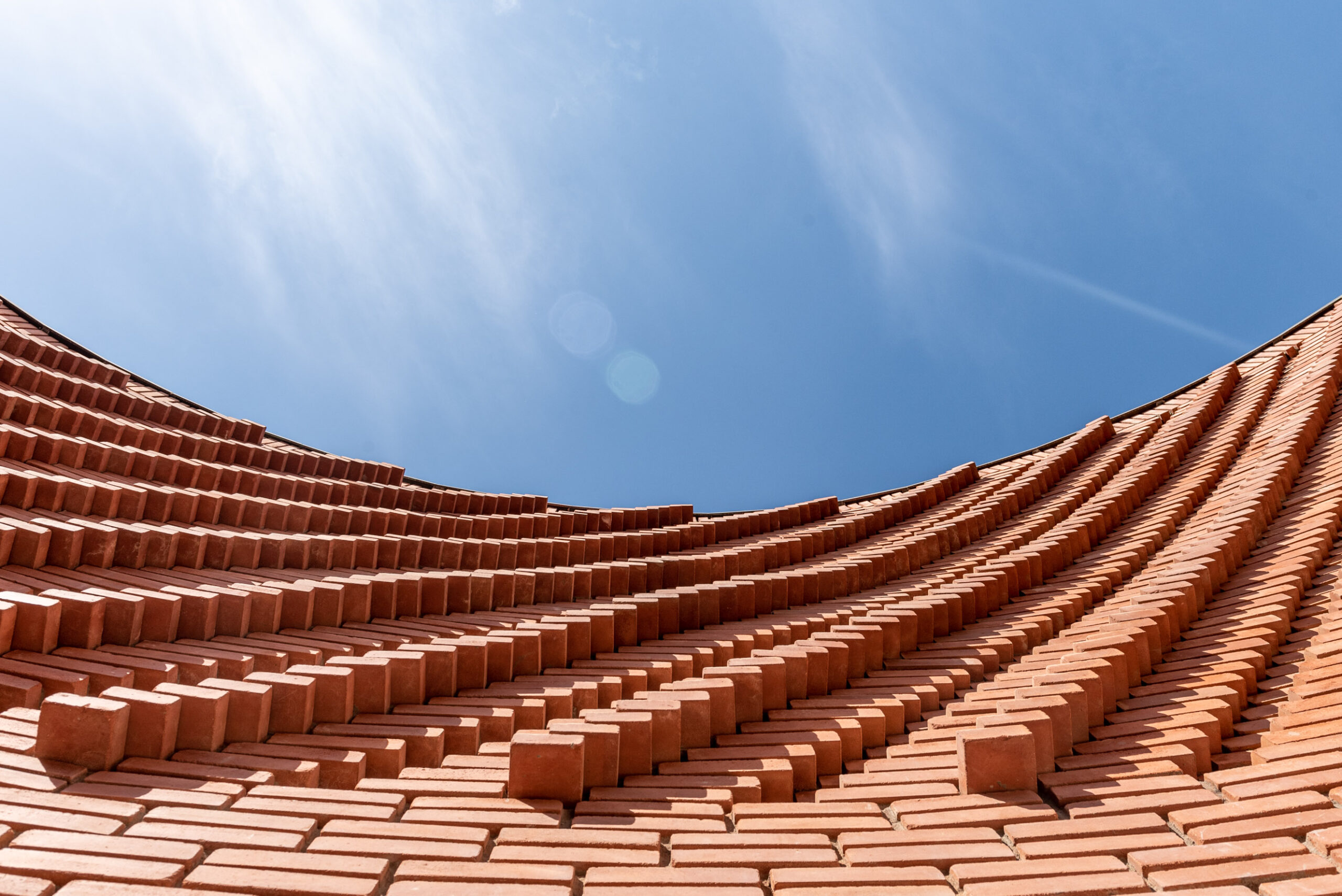
Yves Saint Laurent Museum by Studio KO, Marrakech, Morocco features a façade made up of highly intricate interlocking bricks. The bricks were fabricated using a custom-designed CNarchitizer.com/…/yves-saint-laurent-museum-marrakechC machine that milled each brick to precise specifications. The bricks were then hand-assembled to create the façade, which creates a striking play of light and shadow during the day. Photographs by studio hcrbzkrt
Another pivotal aspect of the Digital Fabrication realm is subtractive digital fabrication. While 3D printing adds material layer by layer, subtractive fabrication starts with an excess and whittles it down to perfection, ensuring that every millimeter is accounted for. CNC milling, laser cutting and similar technologies fall under this category. Once reserved for high-end manufacturing, these techniques are now making significant inroads into architectural fabrication.
Subtractive digital fabrication is often adopted for precision tasks in architecture. Whether it’s carving, etching or pairing intricate details into a facade or forming precise joints to connect structural components, these methods offer unparalleled accuracy time and time again.
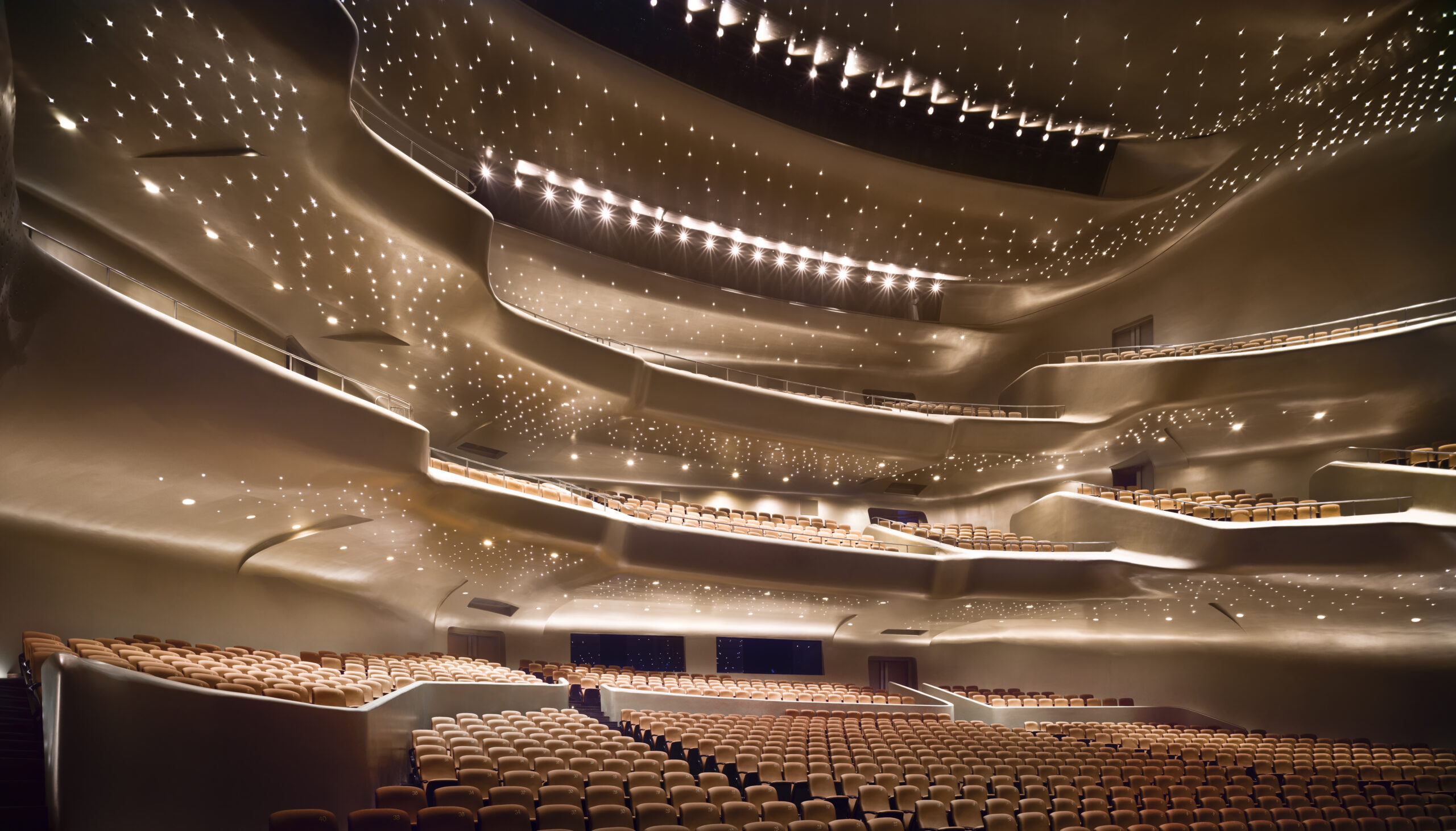
Guangzhou Opera House by Zaha Hadid Architects is a marvel of digital fabrication. The building’s sculptural design was generated using multiple advanced 3D modeling tools to optimize the building’s performance. The technology enabled the architects to achieve precise acoustic conditions for music and opera performances while the exterior facade of the building was wrapped in a series of triangular glass panels that allow natural light to filter into the building.
Materials play a central role in this process. Different tools and techniques are optimized for various materials, from hardwoods to metals and types of stone and as with 3D printing, digital simulations and testing can be undertaken before any material is wasted. The blend of traditional craftsmanship with modern technology is leading us to a resurgence of architectural detailing in design, with subtractive digital fabrication facilitating intricate designs at a fraction of the time and cost.
As the narrative of Digital Fabrication continues to evolve, the integration of robotics and artificial intelligence emerges as a significant chapter. Robotics, once primarily associated with industrial manufacturing, are now finding their place in the architectural domain. These machines, characterized by their precision and efficiency, are being deployed in various stages of the design and construction process, ensuring accuracy and consistency like never before.
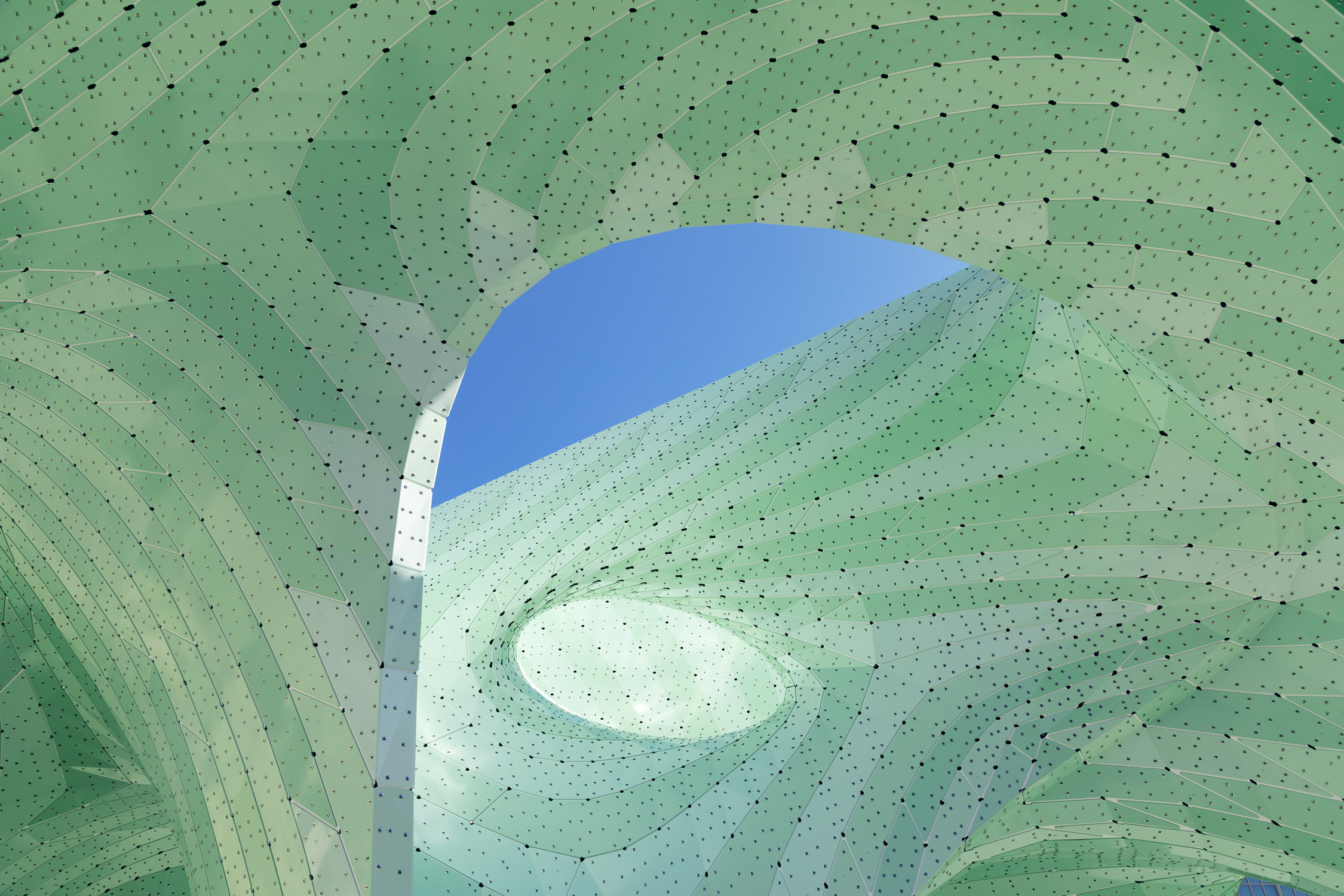
Zephyr by MARC FORNES / THEVERYMANY, Lubbock, TX, United States, is a highly curated system of computationally finessed protocols perfected by robotic intervention to create a seemingly impossible structural skin. The hollow-bodied structure harnesses flowing trajectories in diagonalized stripes of intense curvature, which shear out from an articulated base and meeting space.
However, the true potential of these robotic systems is realized when complemented by artificial intelligence. Unlike traditional machinery, AI-driven robots are not merely executors of pre-defined tasks. They can analyze, adapt and optimize their actions based on real-time data and feedback. For instance, during a fabrication process, if an anomaly in the material is detected, the AI can instantaneously adjust the robot’s operations to account for it, ensuring the integrity of the final product, saving time and reducing waste, all while maintaining stringent quality standards.
As with most things in architecture at this time, sustainability sits at the forefront of the digital fabrication conversation, and thankfully, it finds a natural ally there. Each of the technologies that are being rapidly advanced ensure accuracy, offer drastically reduced waste and support a designer’s ability to create structures that are harmonious with their environments while responding to the needs of their inhabitants. In learning and adopting these new strategies, architects and designers can guarantee a thoughtful approach to both design and construction in the future.
Architects: Want to have your project featured? Showcase your work through Architizer and sign up for our inspirational newsletters.