The ability to 3D-print objects in exceptionally strong materials like Kevlar, fiberglass, and for the first time, carbon fiber, means one thing: “No more Yoda heads,” according to MarkForged creative director Jeff Klein.
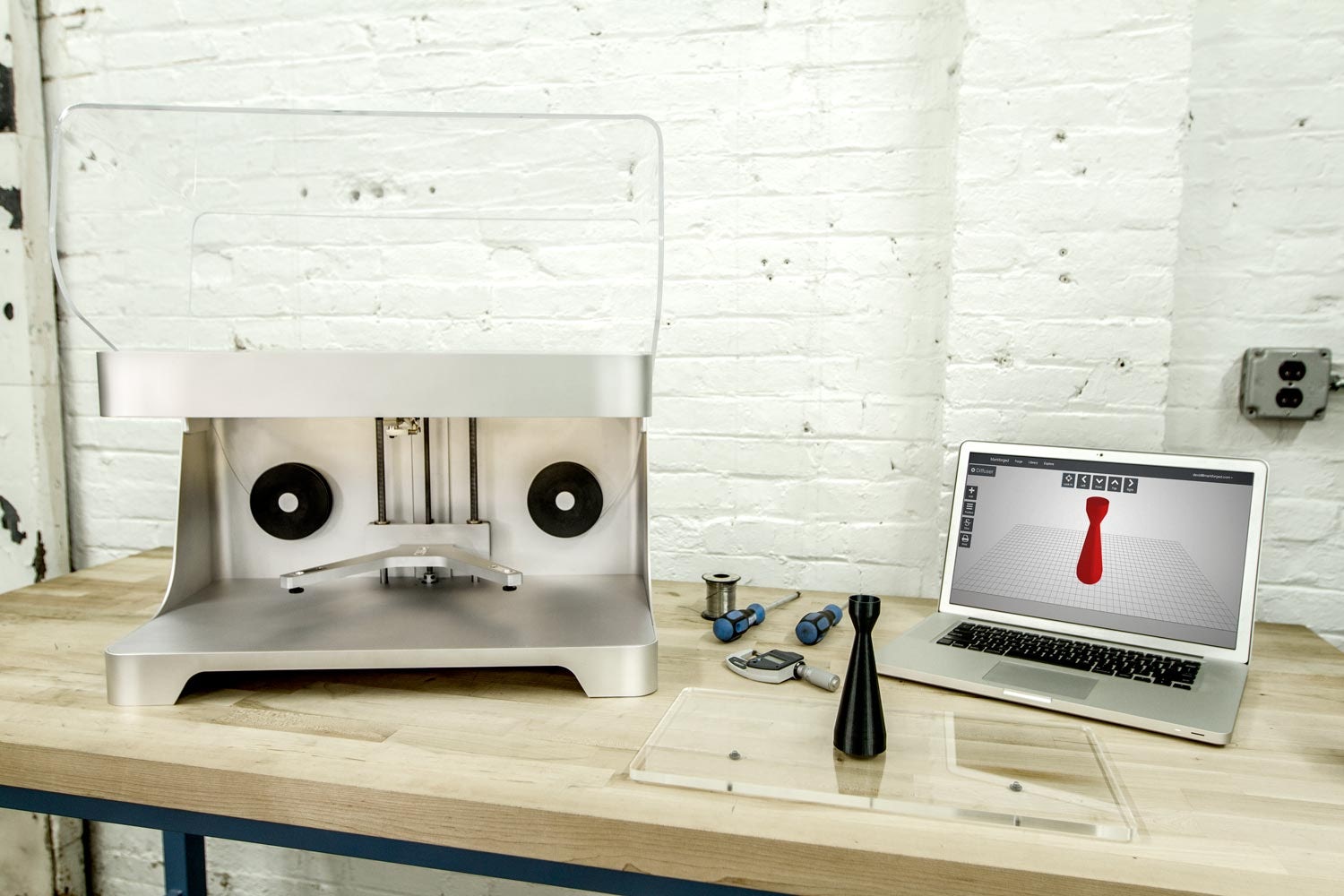
MarkForged (stylized as MARKFORG3D) is the Boston-area startup behind the Mark One, a 3D printer that launched in its current form in September and is billed as the world’s first to extrude carbon fiber. The advantages of this material — typically used in the production of airplanes, spaceships, racecars, bicycles, and military vehicles — are myriad: it’s thin, light, heat-tolerant, and hardier than the average 3D printer filament.
“It’s 20 times stiffer than ABS, five times stronger than ABS, and has a higher strength-to-weight ratio than 6061-T6 Aluminum,” Klein told Architizer during day one of the Consumer Electronics Show in Las Vegas, which makes Mark One suitable for printing industrial-strength parts — as opposed to the tchotchkes that home 3D printers are usually limited to (Star Wars-themed or otherwise).
The machine’s rapid prototyping begins by laying down a nylon filament, a lower-cost material ideal for printing trial and error. Once you’ve tweaked your design to its ideal specifications, you can bolster that nylon through Composite Filament Fabrication or CFF, reinforcement with continuous strands of Kevlar, fiberglass, or carbon fiber.
“Basically what separates us from a lot of the other companies is that the parts that come out of this machine are real functional parts,” Klein said, showing off his inability to bend the 3D-printed racecar part in his hand. Founder Greg Mark, aerospace engineer, actually worked with such composite materials during his former days as racecar-part designer.
The Mark One can produce objects with dimensions as great as 12 x 6.25 x 6.25 inches, ready immediately, with no curing time. It’s on view at the Consumer Electronics Show through January 9.