Architects: Want to have your project featured? Showcase your work by uploading projects to Architizer and sign up for our inspirational newsletters.
We live in a paradox. The impact of human development on the world has never been more apparent, but development continues and is gathering pace. More so, to a large extent, this is happening unabated — or certainly faster than regulations and legislation seem capable of keeping up.
In April, BloombergNEF published its fourth Zero-Carbon Policy Scorecard, and the numbers were troubling. Among the G20, the highest-ranking countries saw their net zero rating decline by an average of 1% year-on-year as funding fell across the board. The current trajectory shows none of the planet’s wealthiest nations are on course to meet their emissions targets by the intended deadlines — 2050 for most.
It’s easy to feel disheartened, given the vast sums of money pouring from public and private purses into environmental projects. Then you start digging into the details and begin to realize the poor performances not only emphasize the scale of change needed for the next stage of transition — we’re running out of ‘easy wins’ — they also cast in painfully sharp relief the monumental challenge of transforming our built environment, which is 40% of the carbon we pump out.
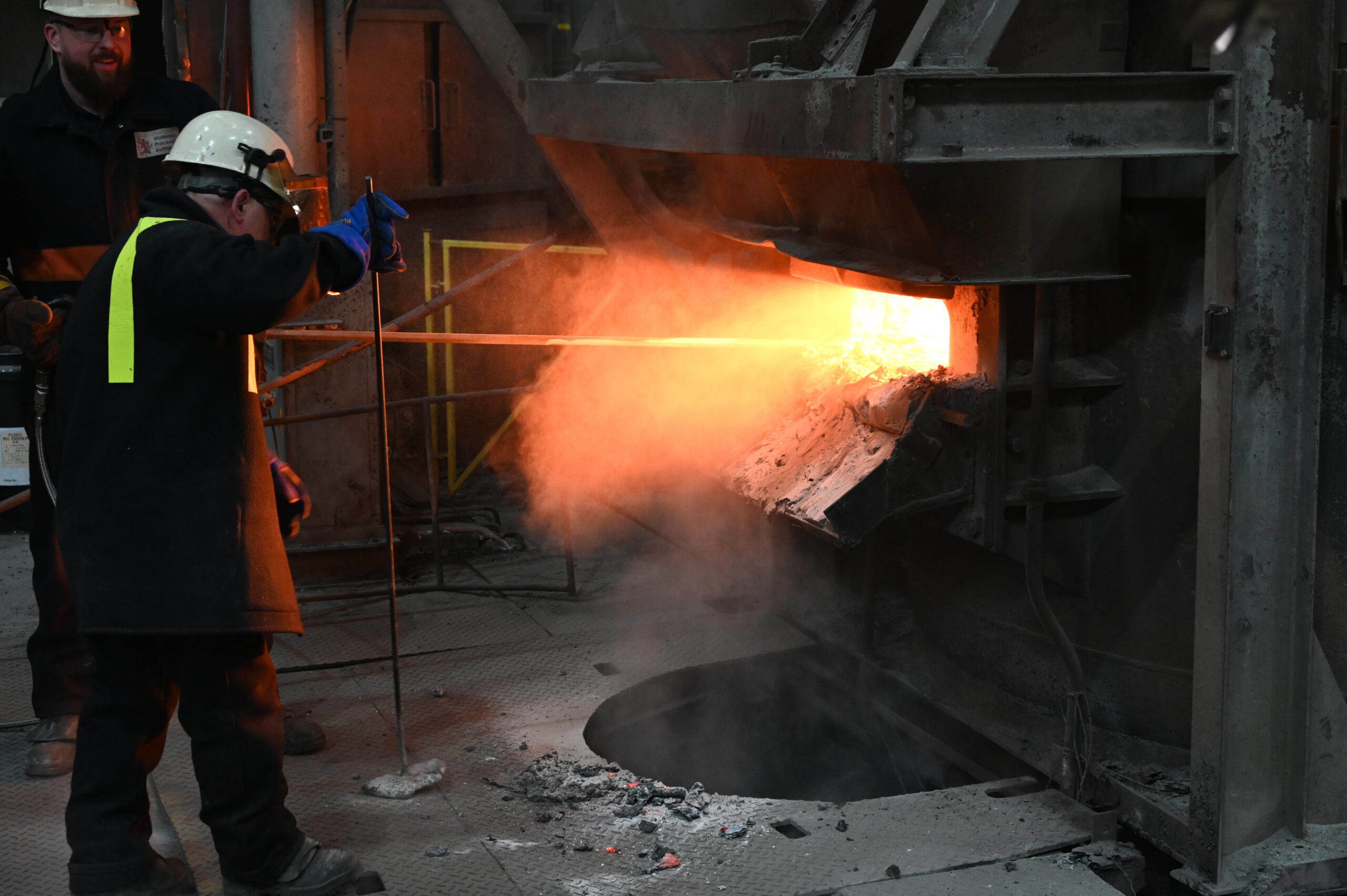
Researchers at the University of Cambridge have made a breakthrough in the development of low carbon cement, by University of Cambridge, Materials Processing Institute
Some countries have made progress. In the Netherlands, for example, greenhouse gas output from buildings has fallen by 36% in the past four years alone. This compares to the UK, which only managed 13% in a comparable period of time between 2018 and 2022. A target of 19% minimum had been set for this period.
But while Britain’s green credentials seem increasingly questionable, the country is still home to some of the most pioneering research in the fields of climate and the environment. This is most recently evident in news out of the University of Cambridge suggesting a major breakthrough in the development of a more sustainable cement. A material which, the BBC argues, “forms the foundation of the modern economy, both literally and metaphorically.”
Putting that claim into perspective, cement produces around 7.5% of all human-made CO2 emissions. If this was a sovereign state, it would be the third biggest source after China and the US. For every tonne made, a tonne of carbon dioxide escapes into the atmosphere, and our appetite is phenomenal.
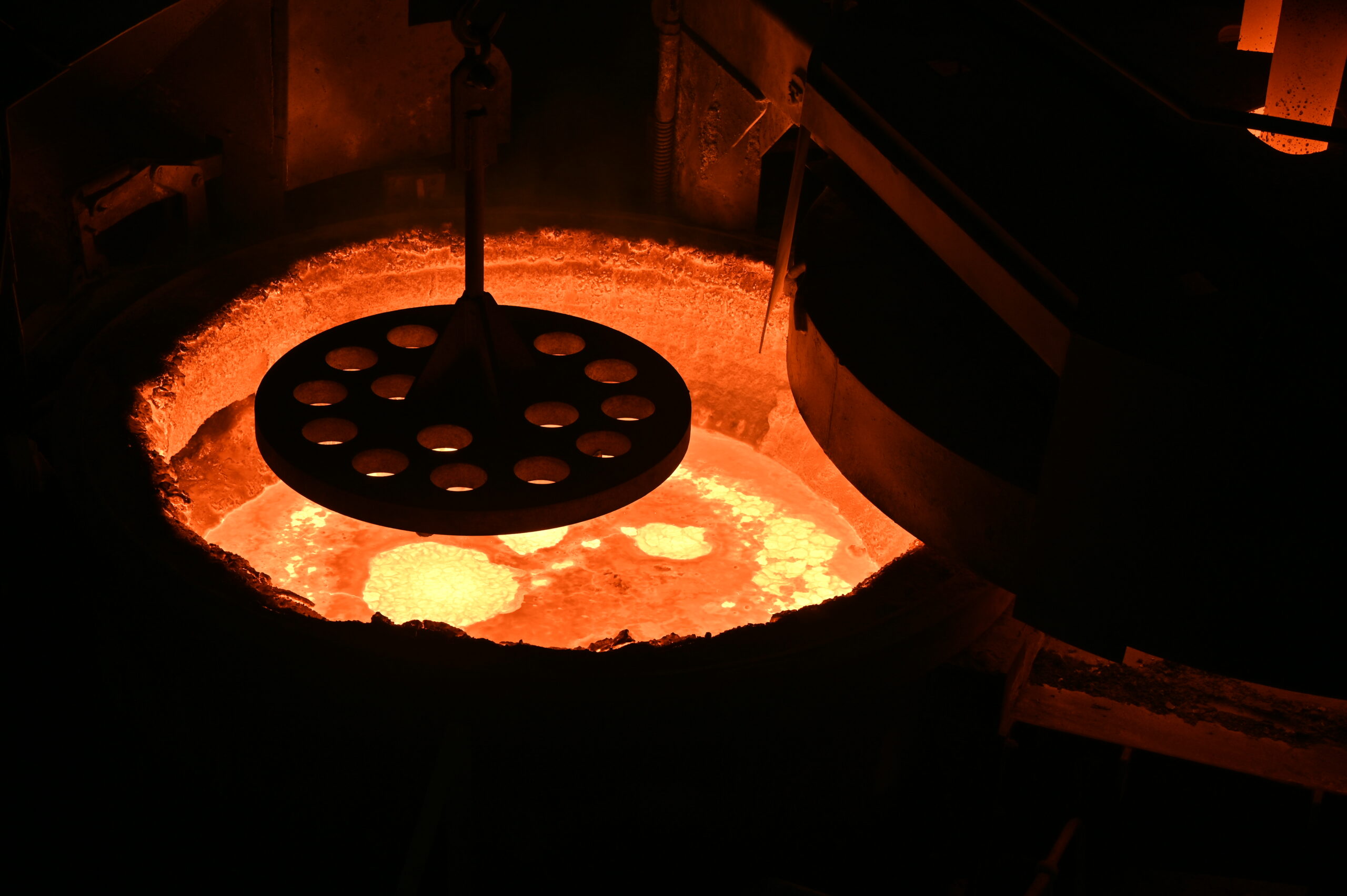
Used cement is fired to around 1600C using ‘waste heat’ from the production of recycled steel in order to make the University of Cambridge’s ‘green cement’, by the University of Cambridge Materials Processing Institute
In 2023 alone, the world produced 4.1 billion tonnes, a significant markup on the 1.39 billion recorded in 1995. We now consume more cement than any other resource except water, and the situation is escalating. Markets are growing; sub-Saharan Africa is expected to see a 77% increase in demand this decade, India is projected for 42%, and North America’s needs are likely to rise by around one-fifth.
The Cambridge project helps to mitigate some of cement’s footprint in two separate ways. Firstly, the input stream is used cement, which can be reactivated at high temperatures — a balmy 1600 degrees Celcius. Secondly, the team are “piggybacking” on the heat generated through steel recycling to fuel the process.
Dubbed “electric cement”, and billed as a “world first”, the test has essentially proven high grade Portland cement can be made from old material in electric-arc furnaces, which can be powered by renewable energy. Given a significant proportion of CO2 produced in manufacturing traditional cement comes down to powering the infrastructure, this could be a huge step forward. The brains at the University of Cambridge are not alone, either.
Further north, researchers at Nottingham Trent University, in England’s East Midlands, have also been making headway. The team has been using waste foundry to substitute 30% of the sand involved in the production of concrete. In the end, the material they created offers 78% of the stability and durability of standard concrete. Although this has limitations, garden slabs, paving stones, cycleways and lighter load-bearing products could now be made from this ‘sustainable’ resource.
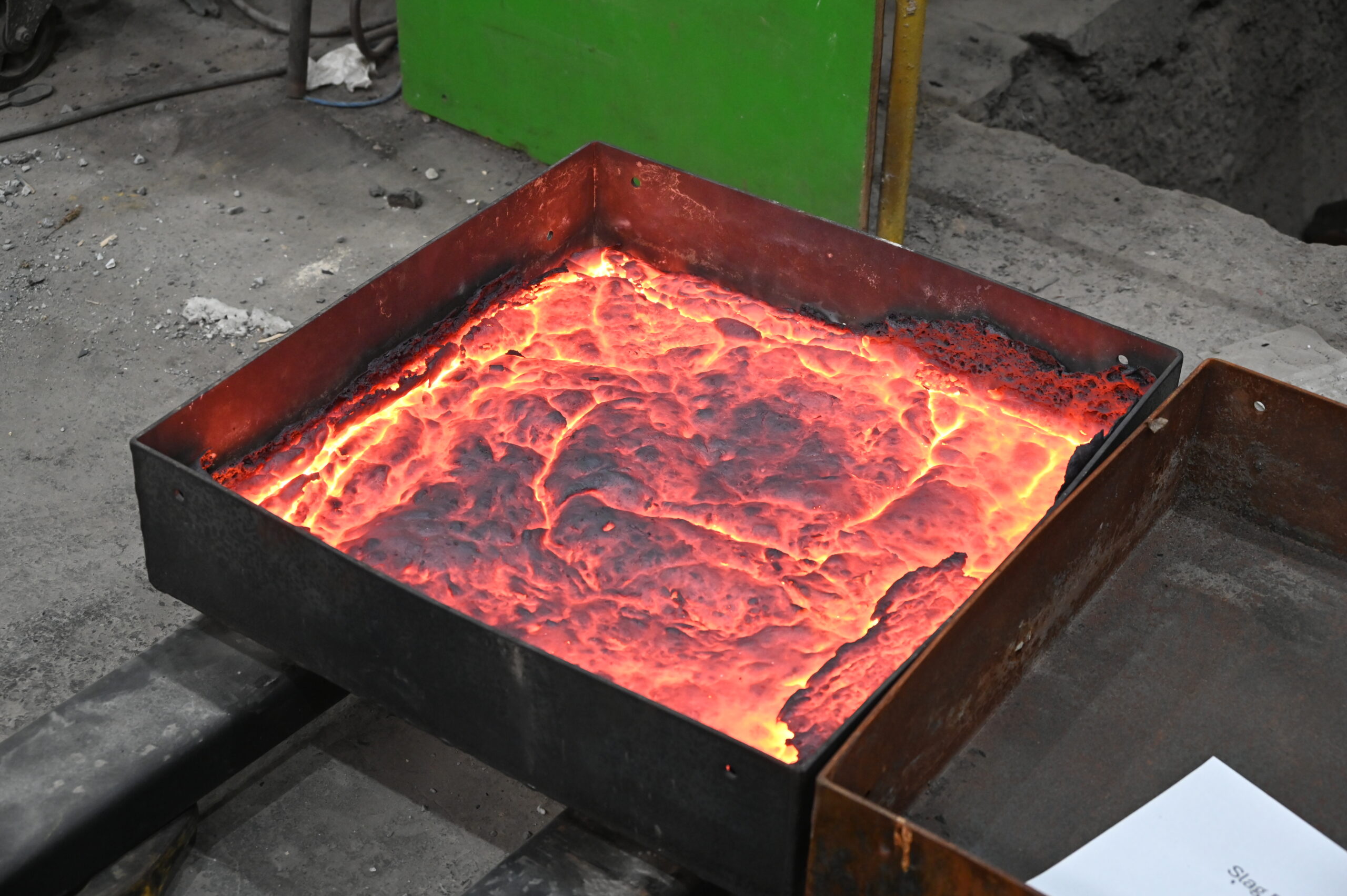
Image by the University of Cambridge Materials Processing Institute
Emissions savings come from supplementing energy-intensive ingredients for leftovers and waste streams, which also reduces transportation footprint. Tides are turning elsewhere, too. In the EU, regulations like the Carbon Border Adjustment Mechanism and the EU Emission trading system are just two examples whereby the net is tightening around high emitters. In the long run, any operation with a large carbon output will be forced to overhaul its processes or face serious penalties.
At this point, it could become cheaper to use low and zero carbon techniques than traditional approaches to producing cement. Or at least that’s the hope of green startup CemVision. In December last year, the company announced it had reach industrial-scale production of ‘green cement’ at its demo plant in Poland, which now has an annual capacity of 4,000 tonnes.
Remarkably, the material has 95% less environmental footprint compared with the standard material. And again the focus is as much on what you’re heating as how. In this instance, limestone—- the core ingredient in cement — is replaced by slag products from steel and mining, cutting the need for expensive transportation from quarries and finding a new use for old materials which would otherwise have posed an ecological challenge in themselves.
Each of these solutions is different, but they all share some traits. Not least their reliance on a more circular approach to resource management. More than anything, this serves as a stark reminder of just how wasteful the 20th Century approach to construction and development has been, emphasizing the staggering volumes of valuable materials we must have discarded in the past. If nothing else, that’s surely the big takeaway — our future has to be much less throwaway.
Architects: Want to have your project featured? Showcase your work by uploading projects to Architizer and sign up for our inspirational newsletters.