In line with our new content direction, Architizer is highlighting a different building-product and how to specify it. One of our previous topics was Metal Cladding. If you’re looking for the perfect metal for your next project, search for it on Architizer’s new network marketplace for building-products. Click here to see if you qualify. It’s free for architects.
As architects become even more conscious of the ways in which sustainable design benefits the Earth, many are choosing building-products that specifically cater to enhancing the green performance of their designs. When it comes to specifying the various parts of an architectural project, choosing recycled materials is one way to ensure that the building is giving back to both the community and the world.
For example, a temporary installation on Governors Island in New York City is calling into question the future ways in which recycled aluminum can be incorporated into architectural design. Cast & Placewas created with 300,000 molten aluminum cans and turned into an earthy sculptural pavilion. The project was dreamt up by a New York–based group that included Josh Draper from PrePost, Lisa Ramsburg, Powell Draper and Alexandra Cheng from schlaich bergermann partner, Edward M. Segal from Hofstra University, Max Dowd from Grimshaw Architects, artist Scot W. Thompson and sculptor Bruce Lindsay.
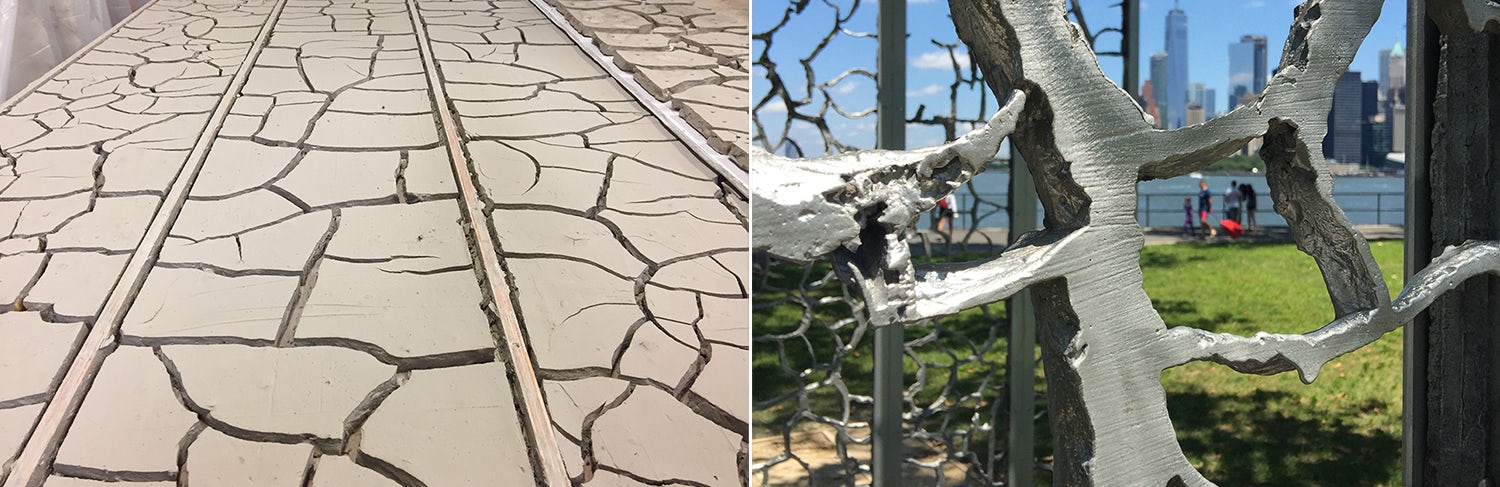
The multi-panel structure features an intricate design thanks to the innovative prefabrication method made up by the design team. They used wooden trays of cracked clay, sourced from a local glacial deposit in Queens, and poured the hot aluminum through the natural crevices formed within the dry clay.
It took many experiments for the team to achieve a sturdy seamless structure without incoherent crevices or a problematic amount of inclusions or porosity within the metal. But once the pavilion was finished and stood as a shading device for public use on a hot summer’s day, it was clear that the project was a huge success. More importantly, it showed that this unconventional yet simple casting process could create something that’s not only beautiful and functional, but also strong enough to stand on its own and challenge the ways in which architects think about reusing waste materials.
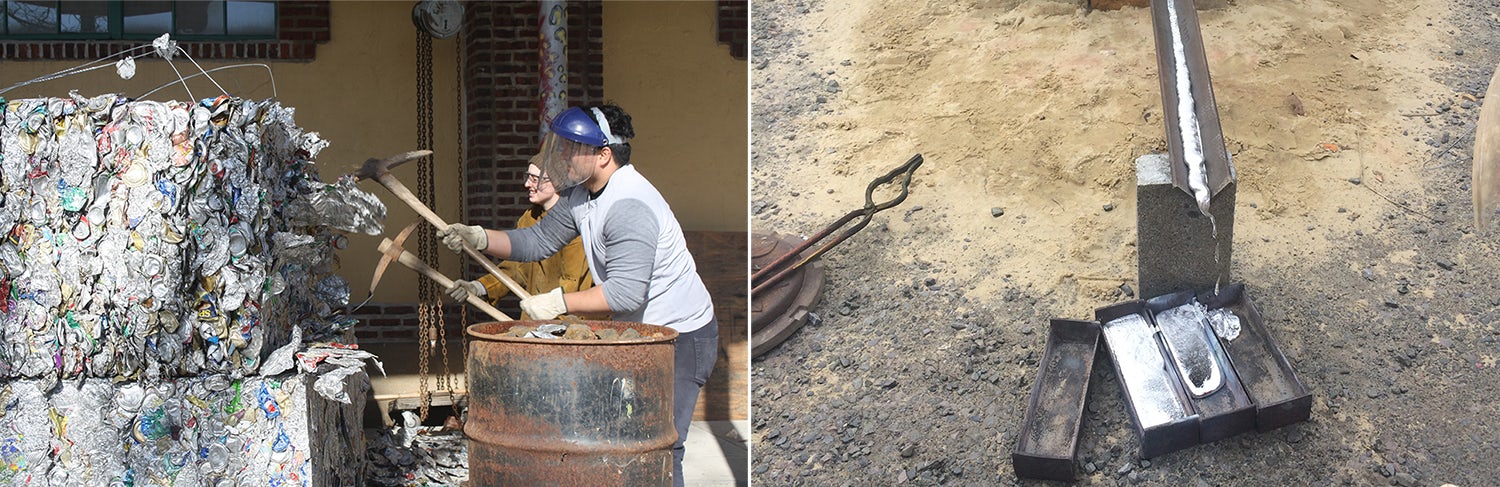
“We thought to ourselves,” Draper said, “at what point does an architect take the risk into making something that may or may not work? If an architect can get to the bottom of a process — meaning learning how things are actually made — then you have more control or more possibilities of what things can become.”
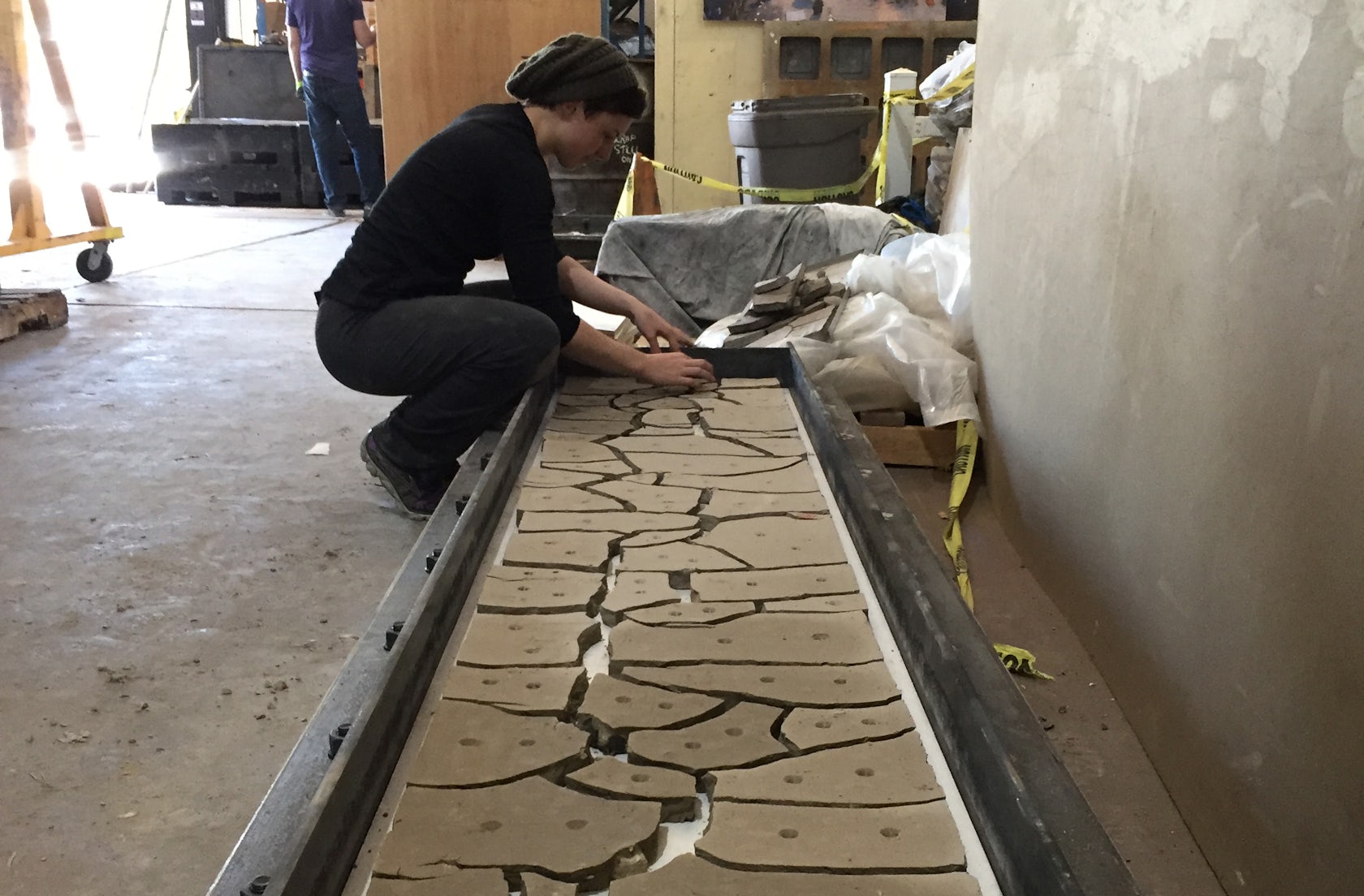
The Cast & Place team ended up producing a series of incredibly strong tangible panels that are as exquisite to feel as they are to look at. Imagine these bespoke panels lining the interior walls of a corridor inside a commercial building or covering a glazed ceiling that exposes daylight coming directly from the sky. Placed in front of or behind glass would create a unique dappled effect of light streaming into a space throughout the day. Glass could even be set inside it.
The panels could also serve as partitions in a garden or a public park as an entrance to an amphitheater or seating area. The possibilities are endless, and Draper’s team knows it because they conceived the casting method and watched the panels come to life with their own eyes.

“Recycled aluminum panels as a structural skin could also be breathtaking,” he said. “It’s possible to create a façade where every single panel is different. It has known quantities and known performance standards, but leveraging the emergent behavior of the materials is entirely up to the fabrication process. I think that’s something that’s a holy grail for designers. How do you get sameness in difference?”
Situated in the right context, this kind of architectural object could generate a calm and creative atmosphere while simultaneously showcasing the strength behind the building process. Something like this is architecture, but it’s also a product, and it’s also art.
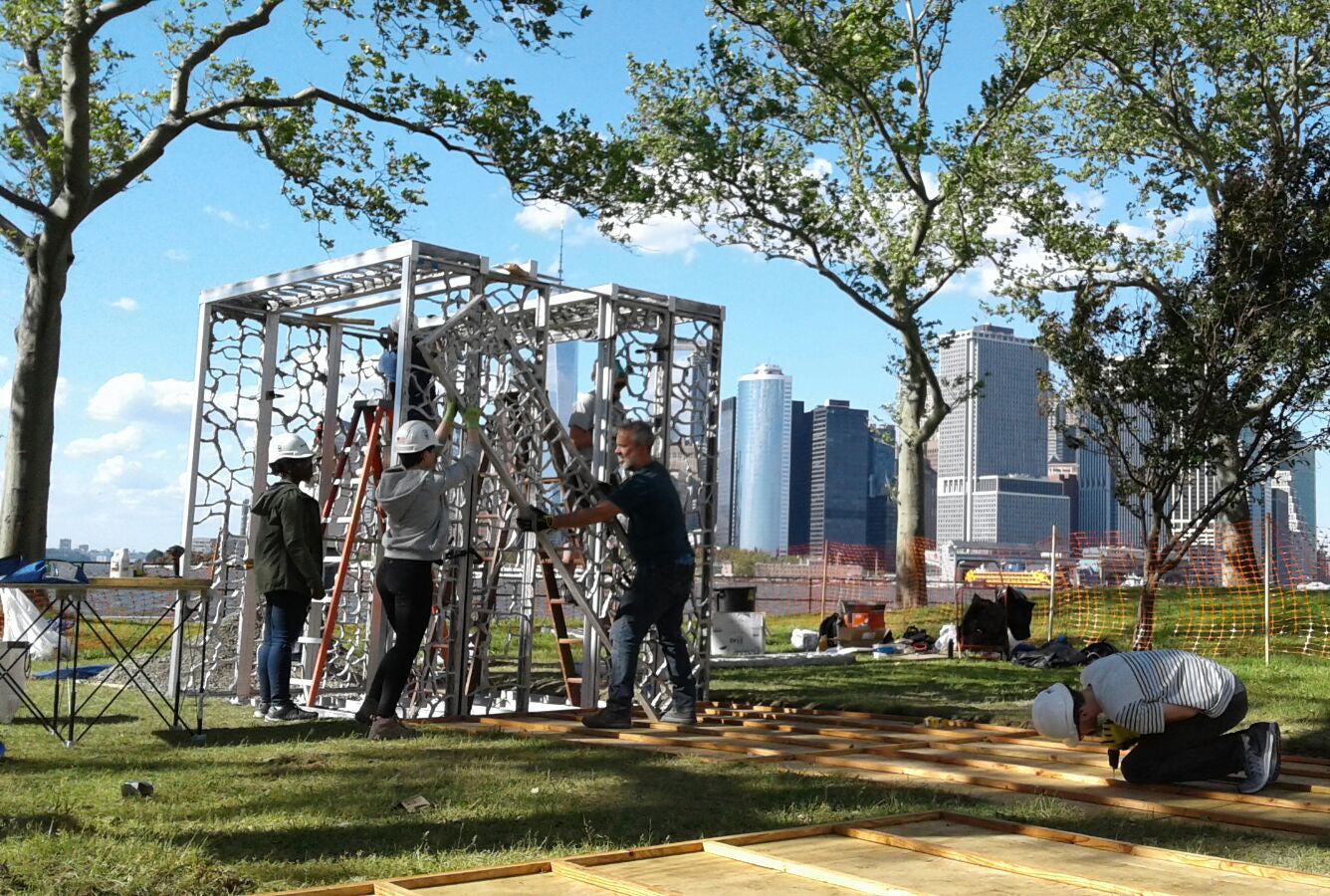
Isn’t that what building-products are in most cases? They live at the intersections of function, detail and aesthetics. From hidden hinges and expansion joints to metal cladding and fiber-cement exterior panels, these materials contribute to the look and feel of a piece of architecture while ultimately helping it achieve a high standard of performance.
When it comes to creating a building-product, it’s truly all about the manufacturing process. That’s why the team behind Cast & Place sought to introduce a new method of fabrication — one that promoted experimentation, encouraged failure and inverted what a visible error, like the cracking of clay, meant for the end result.

“This project uses cracking as a design tool,” Draper said. “Here we’re looking into structural optimization. What’s going to make this the strongest product? Where the material wants to break is where we can explore the optimal patterns in the creation of the panels.”
Draper believes this idea can challenge some preconceptions that engineers have about structure. “This isn’t something that can merge computationally,” he said. “It’s doing it through its own inherent materiality.” In other words, it could be enlightening for the industry to explore the nascent processes of natural materials and how that might bring forth surprising structural outcomes.

If it’s not obvious already, a product inspired by Cast & Place could be part of the future of sustainable architecture. Its unprecedented prefabrication process, yielding a one-of-a-kind end result, is the kind of radical thinking that makes great building-products truly standout. But according to the design team, there are some serious questions to consider before embarking on such a feat. How do you deal with risks in a supply chain? How do you get consistency from product to product? How can you make sure your source for the clay material, let’s say, is the same as when the project’s complete as it was when specified?
In the world of product design — and architecture, of course — things happen slowly. When working with organizations that offer products made out of reusable materials, it’s often hard to trace back to the original source of that particular material. But as architects, engineers and product-manufacturers become more and more aware of the ecological impact that materiality has on an overall building project, it’s easy to foresee people more closely following these details.
Images courtesy Josh Draper and Lisa Ramsburg
Looking for the perfect metal siding for your next project? Find it on Source, the definitive network marketplace for building-products. Click here for more information on the best all-in-one specification platform for architects.