Ema is a trained architect, writer and photographer who works as a Junior Architect at REX in NYC. Inspired by her global experiences, she shares captivating insights into the world’s most extraordinary cities and buildings and provides travel tips on her blog, The Travel Album.
Model making has always been a cornerstone of architectural practice, serving as a tangible representation of our visions and designs. Reflecting on my journey in the architecture industry over the past six years, I’ve witnessed an incredible evolution in the techniques and technologies we use to bring our concepts to life. From the meticulous hands-on crafting of physical models to the integration of advanced digital tools, model making has undergone a remarkable transformation, reshaping the way we design and communicate our ideas.
The Lazy Way?
Thinking back to my time in undergraduate studies, there was always a clear distinction between the students who excelled at handcrafting models and those who struggled. I remember the countless hours spent waiting for access to the laser cutter just to ensure our floor plates and façade screens were cut with precision. One vivid memory stands out: a friend telling me that using the laser cutter was the “lazy way” of making models.
But was it really lazy? Or was it a smart approach to leveraging technology to expedite the model-making process? Using the laser cutter taught us to prepare, model and create accurate files — all skills that have become crucial in the industry. Embracing this technology wasn’t about avoiding hard work; it was about adapting to new tools that enhance our ability to bring our designs to life with greater efficiency and precision. At the time, we didn’t even really realize it.
A Hands-On Craft
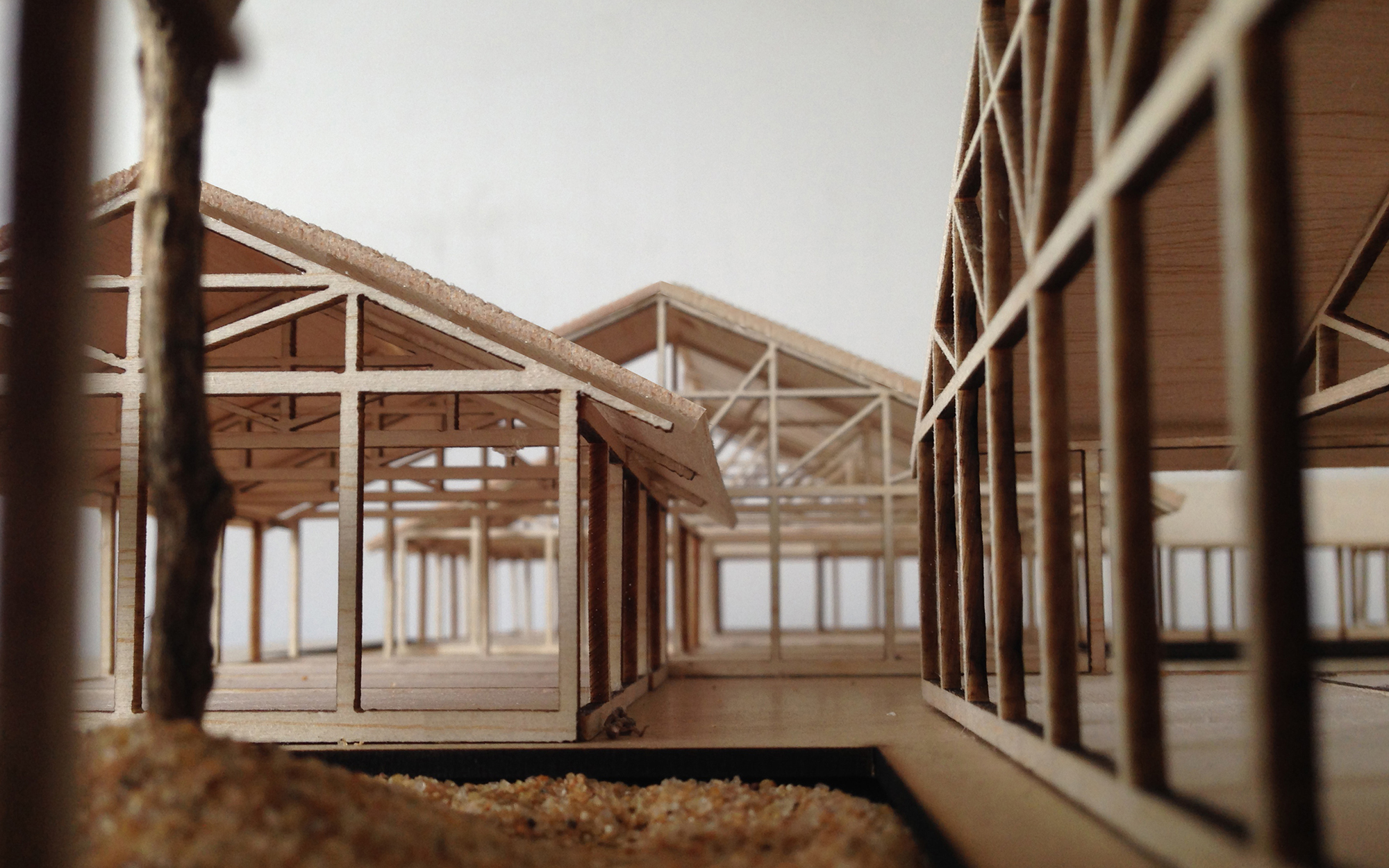
Organic Farm by ARCHSTUDIO, Hebei, China
Model making in architecture has its roots deeply embedded in manual craftsmanship. Historically, architects relied on simple tools and materials like cardboard, balsa wood and foam board to create detailed physical models. These models were not only essential design aids but also powerful communication tools, enabling architects and clients to visualize and interact with proposed spaces. Clients often find physical models more engaging than renderings and drawings, as they can touch, examine and better understand the design. This tactile experience brings them closer to the reality of the design, making model making an incredibly effective way to involve clients in the architectural process.
In architecture school, the art of model making was a cornerstone of our education. We spent countless hours in the workshop, meticulously cutting, gluing and assembling intricate models by hand. This hands-on approach instilled in us the values of precision, patience and spatial thinking. There was something uniquely satisfying about watching our ideas materialize in three dimensions, even if it meant occasionally gluing our fingers together or nicking a fingertip with an X-Acto knife. At the time, creating those hand-crafted models involved a great deal of blood, sweat and tears — quite literally.
Cutting By Hand
Over the past decade, the landscape of model making has transformed dramatically. When I entered the workforce as an intern over six years ago, my primary responsibility was model making. The firm I worked for was renowned for producing countless models to express their vision, but I imagine many interns had similar experiences. I spent hours in the model shop, meticulously cutting thousands of tiny contextual houses out of foam, trying my best to be as accurate as possible. I came up with methods to ensure every stick of balsa wood was precisely the same length so columns would stand uniformly. I often found myself holding pieces together for long periods of time, waiting for the glue to set… How things have changed since then…
At that time, we had just started using laser cutters, but they weren’t very advanced. To be honest, it wasn’t very safe or healthy either. The spaces housing the laser cutters were so poorly ventilated that we would sit in rooms filled with fumes for hours, not giving it much thought… No wonder we all felt dizzy by the end of the day.
The Arrival Of The 3D Printer
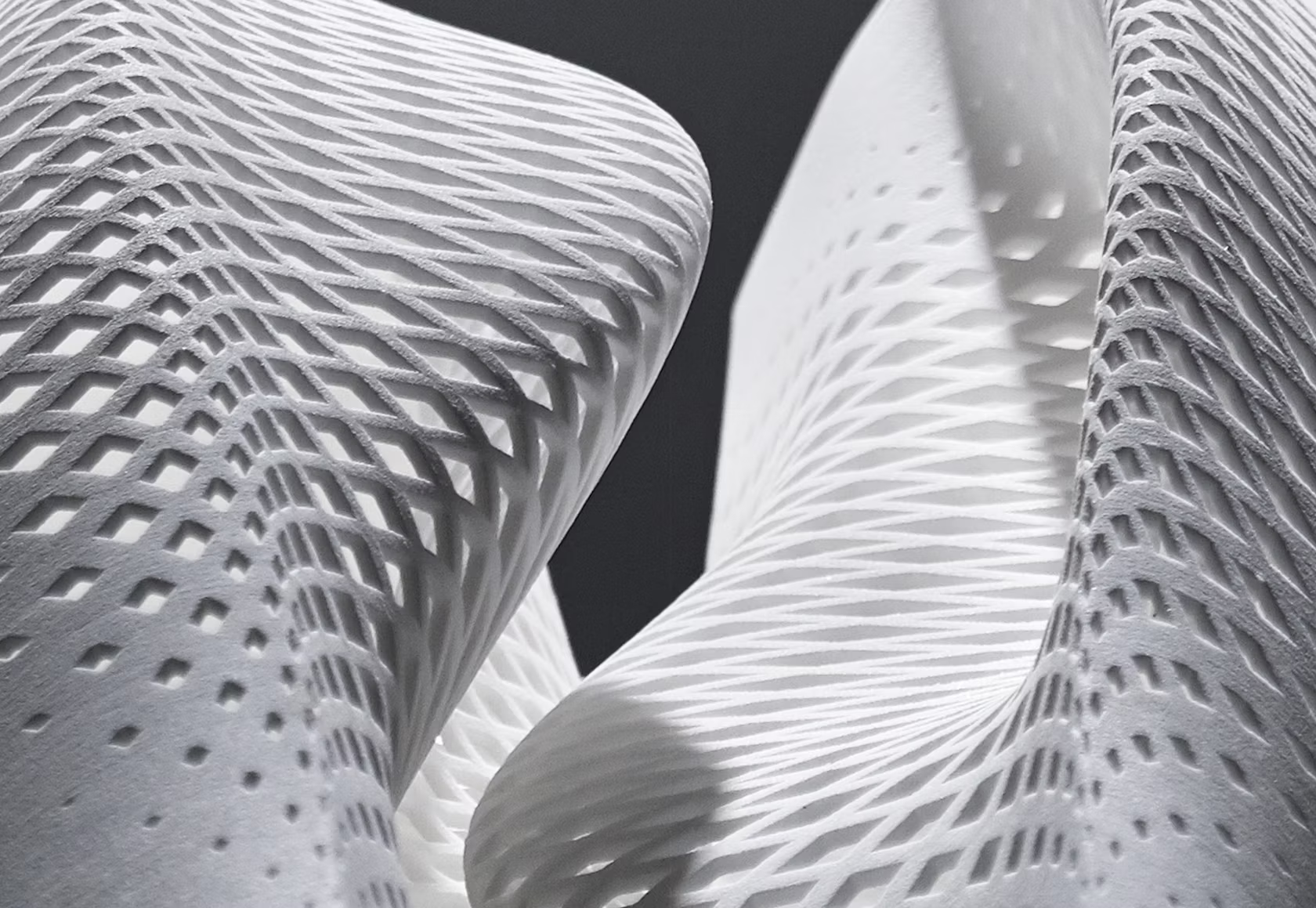
Interstice by Alessandro Isola Ltd., London, United Kingdom
It wasn’t until five or six years later that the 3D printer truly came into its own, revolutionizing model making and prototyping. Suddenly, the hundreds of tiny houses we used to painstakingly cut by hand over weeks could be printed in a day. The introduction of 3D printing was a game-changer for model making. This technology has allowed us to create highly detailed and accurate models with unprecedented ease. Complex geometries, such as curved surfaces and intricate details that were once difficult to achieve by hand, can now be printed with precision, and within minutes. The ability to quickly iterate and produce multiple versions of a model has significantly enhanced our design process, enabling us to explore various options and refine our concepts more effectively.
Programs like Rhino, SketchUp and Revit have revolutionized the design and modeling process, allowing us to create and manipulate digital models with exceptional accuracy. These programs seamlessly integrate with 3D printing technologies, making it easy to print designs directly from the software. They have bridged the gap between the virtual and physical realms, enabling us to convert digital models into physical ones through 3D printing, laser cutting and even CNC milling with remarkable precision.
Combining the Physical and Digital
The integration of digital and physical model making has unlocked new possibilities for architects. Hybrid models, which blend traditional craftsmanship with digital fabrication, have become increasingly popular. For example, we can 3D print a complex structure and then enhance it with hand-crafted details, achieving a level of detail and realism that was previously unattainable. In fact, I believe those are the best models — the ones with perfectly printed contextual buildings, precisely laser-cut roads and sidewalks, and detailed touches like trees and other small elements added by hand.
It’s amusing to hear how those who used to make models by hand often look back with a sense of nostalgia and say, “You should have seen how tough we had it back in the day.” Of course, modern model making comes with its own set of challenges. You still need to understand how to construct a model, know what goes where, and carefully plan the building process. While new technologies streamline the process, they also introduce their own complexities. The craft of model making is still something that must be learned and not everyone masters it easily. Nowadays, the room for error lies more in the 3D modeling phase; once you input the correct design into the printer, the model will typically come out as expected (assuming the printer functions properly). The challenge has shifted from physically creating the model to ensuring the accuracy of the digital design and assembling the components rather than creating them.
The Incredible Transformation
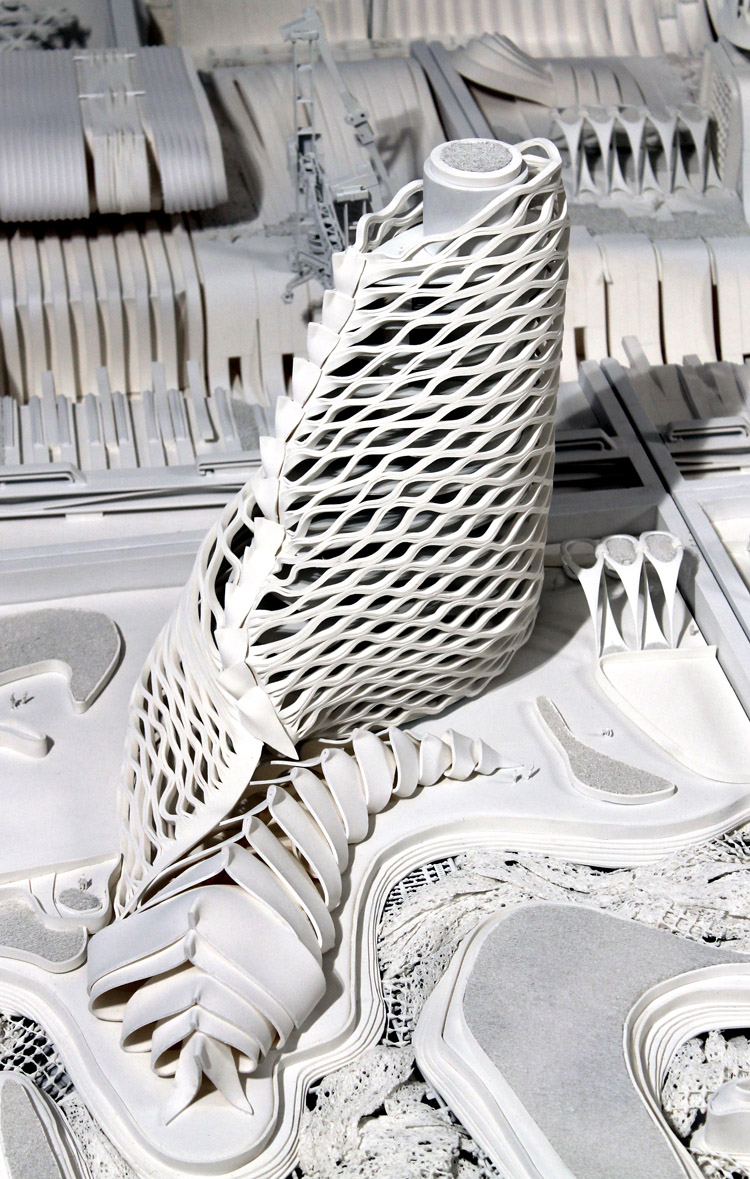
Super Docking – Brooklyn Navy Yards by Planetary ONE, New York City, New York
Having observed the architecture industry evolve over the past six years, I find it fascinating to witness and be part of this transformation. We are still evolving, but the rapid shift from hand-made models to the current level of precision and sophistication is incredible. The transition from traditional to digital model making has not only enhanced our design capabilities but also expanded our creative horizons. While I still deeply appreciate the tactile experience of crafting models by hand, I embrace the efficiency and precision that modern technologies offer.
Indeed, you can often pinpoint when a model was made just by looking at it. There’s a clear distinction between those that were hand-crafted in the past and those produced with modern technology. Looking ahead, I’m excited about the ongoing advancements in model making. The evolution over the past decade has been truly transformative. From its origins as a hands-on craft to the integration of cutting-edge technologies, model making has continuously adapted to meet the evolving needs of the modern architect.
If you’re a student or a young professional, what are your thoughts on this topic? Did you find handcrafting models challenging or enjoyable? How do you feel about the ease that modern technologies bring to model making? And despite these advancements, what new challenges have emerged with having such sophisticated tools at your disposal?