VIATechnik specializes in technology for the architecture, engineering and construction industries and works with clients in the realm of virtual reality, BIM services and artificial intelligence.
When it comes to using prefabrication technology in the industry, we’re facing the same issues we saw during the adoption of BIM.
Namely, the industry is vastly scattered, knowledge is siloed out — designers, engineers, builders, and fabricators all have different expertise and processes that don’t always play well together, especially when insufficient communication is happening. This is all slowing down the uptake of prefab. As a report from global consulting firm McKinsey put it, “much of construction has evolved at a glacial pace.”
“Where we do see a lot of success, however, is when prefabrication is intended from the start of the project — as early as when an owner decides to invest in it at the beginning of the design of a project and has full control over the project” said Tyler Gancarz, Project Development at VIATechnik.
Using prefab technology when building projects — especially if you’re already using VDC (virtual design and construction) and BIM (building information modeling) — is a no-brainer. We’ve written before about the great ROI that prefabrication brings to a project, but as a refresher, here are three simple reasons why:
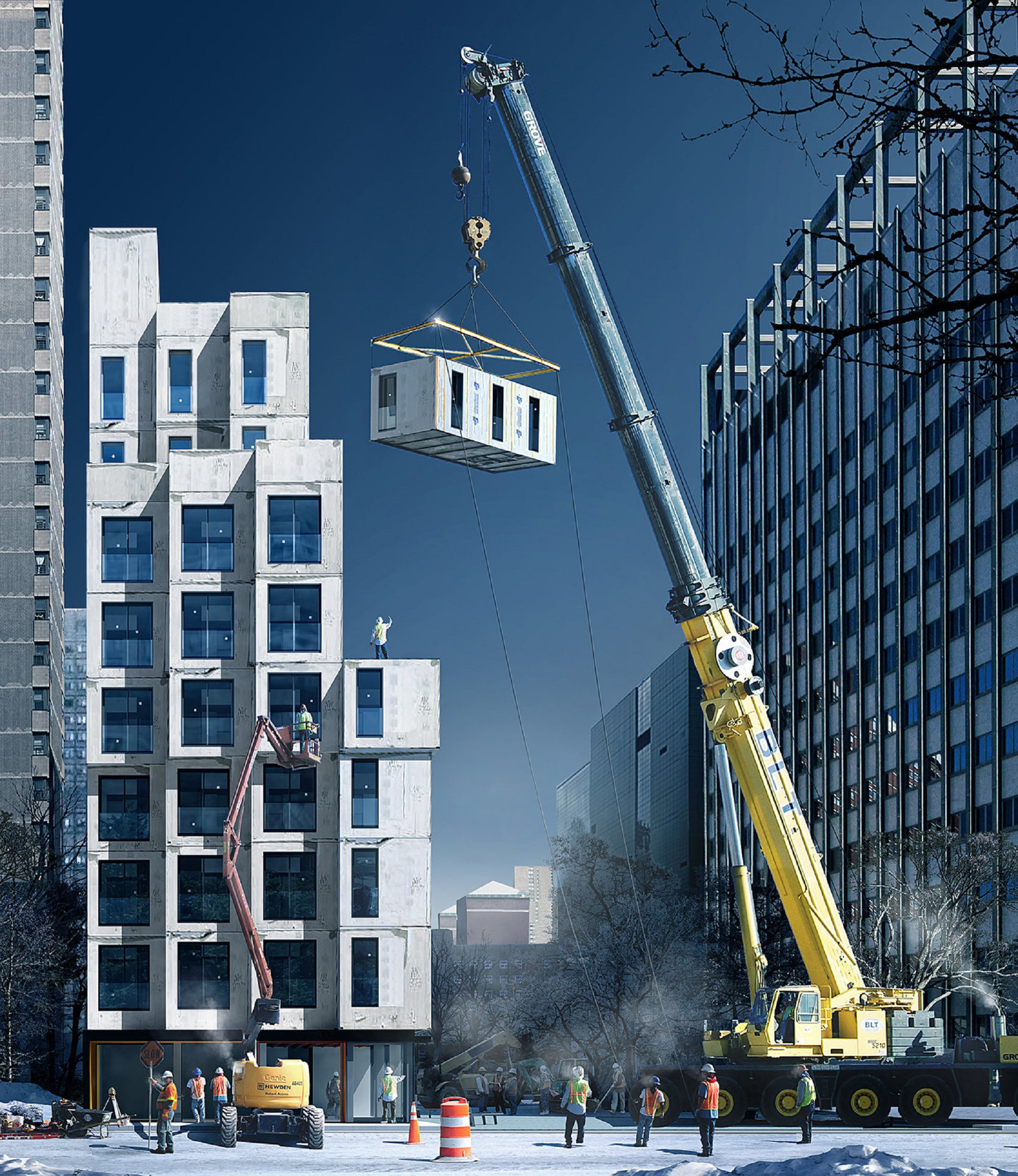
Designed by nARCHITECTS, the prefabricated units of Carmel Place feature generous ceiling heights, ample glazing, Juliet balconies, and numerous shared amenities.
Boost the quality of every detail in a project in record time
A majority of production is done in a controlled environment specifically designed to manufacture and assemble the individual prefabricated components. This allows for quality checks and review–much more thorough than can be done if these components were to be assembled directly at a jobsite.
Unlike a project site, warehouses and factories where prefab components are built aren’t subject to the limitations of geography, so going prefab can be especially beneficial for projects in dense urban areas. Prefab production lines also allow for an optimized workflow and process, because the objects are being built by the same staff in a controlled line.
And as a bonus point, prefab helps keeps the site safe and organized. Because components were already individually assembled at a separate warehouse, this keeps the actual project site clean and clutter-free, and a tidy working space not only increases productivity, it also reduces the risk of accidents.
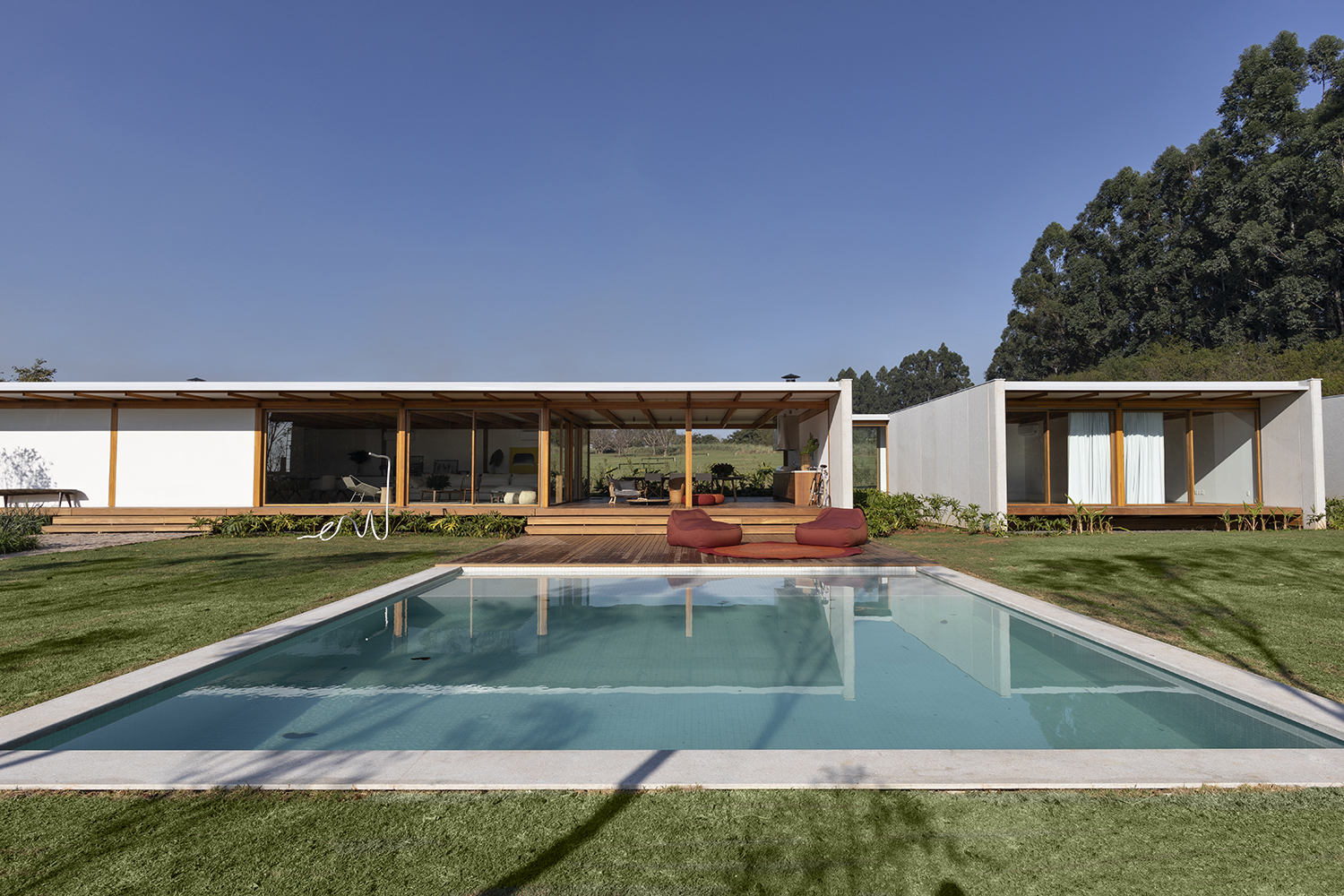
Pipa House by Bernardes Arquitetura, Porto Feliz, SP, Brazil, winner of the 2019 Popular Choice A+Award in the Architecture +Prefab category. The prefabricated concrete house was designed for building efficiency “through an industrialized system that allowed its rapid execution and very low waste production.”
Address the labor shortage issue
The prefabricated production process frees up time for field workers (who are generally more expensive) to cover more projects, which can help mitigate the skilled labor shortage issue the industry faces. We recently visited a project site where workers were in the process of building hundreds of bathroom pods for a hospital using prefabricated technology.
They were able to install the tile in bathroom pods before shipping to site. Imagine the amount of field work avoided, the number of tiles saved from breaking on site, and the amount of time saved from not having to go back and forth because of a small measurement miscalculation (though if you’re already using BIM, this should be unlikely to happen).
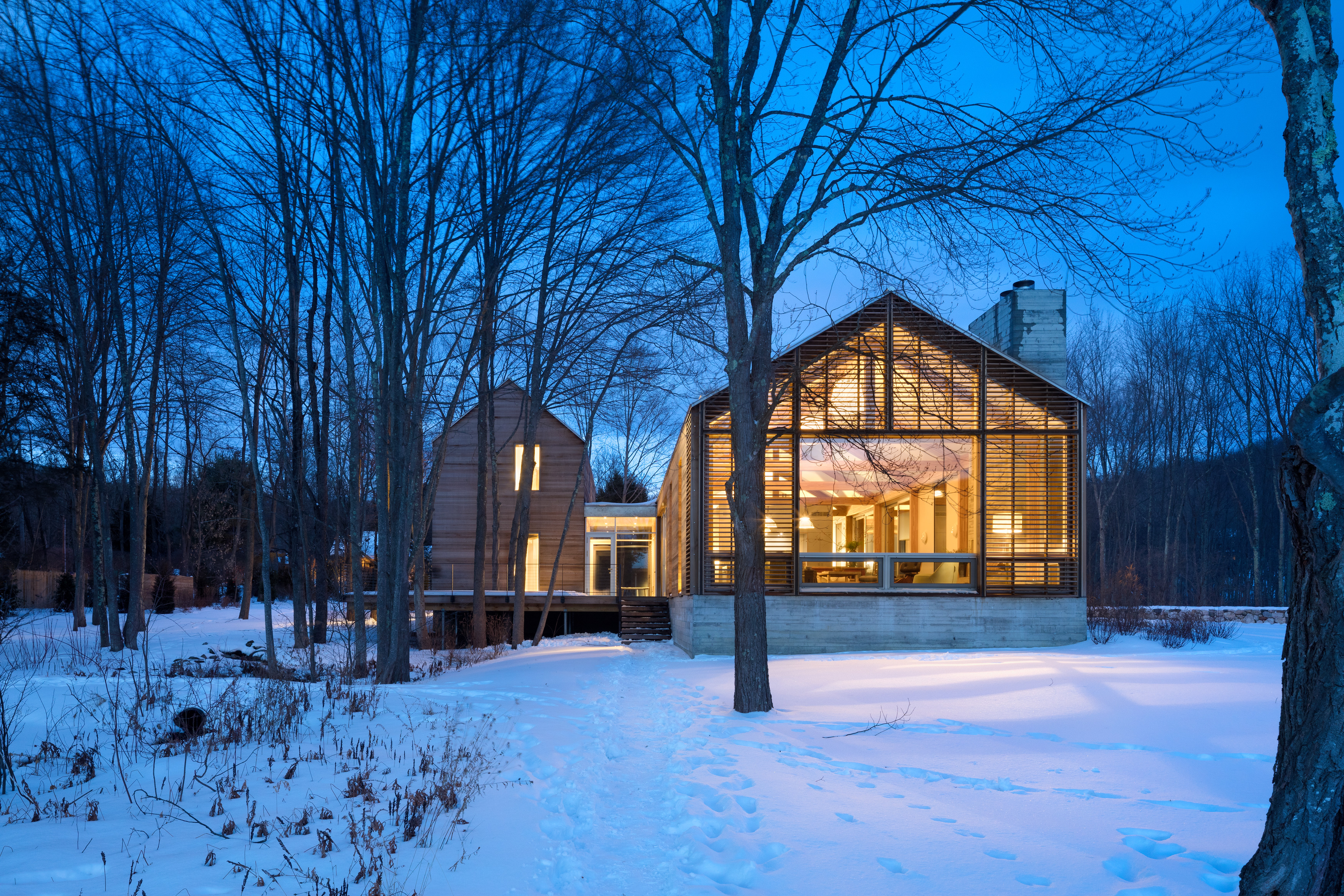
Clinton Corners by Lake|Flato Architects, Clinton Corners, NY, winner of the 2019 Jury A+Award in the Architecture +Prefab category. Fabricated in a nearby facility, the exposed heavy timber frame and super insulated wall panels were delivered to the site and assembled in less than three weeks.
Save time and money by standardizing components
Pairing prefab construction with VDC is an intelligent process that limits project variability and allows for one to manage schedule and budgets better.
And what else helps save time? The opportunity to standardize. If more project owners embrace prefab, then the industry together can establish standards, whether its the building components, or the combination of components. With less unique parts floating around, this means more efficiency for more projects in the long run.
Architects: Showcase your next project through Architizer and sign up for our inspirational newsletter.
Top image via Empa