The Extended Entry Deadline for Architizer's 2025 A+Product Awards is Friday, February 21st. Get your brand in front of the AEC industry’s most renowned designers by submitting today.
Metal cladding has hugged the twists and turns of architecture for decades. From the punched tin of Louis Sullivan to the titanium swoops of Frank Gehry, designers have embraced metal cladding for its formal flexibility and finish. Its popularity is primarily down to its incredible versatility, both avant-garde and off-the-shelf.
However, this material’s greatest strength also makes it a challenge for architects specifying it for a building envelope — the number of different finishes, forms and methods of attachment can seem endless. In this guide, we break down the options to help you decide which metal cladding product is the perfect fit for your next project.
Search for Metal Cladding Manufacturers
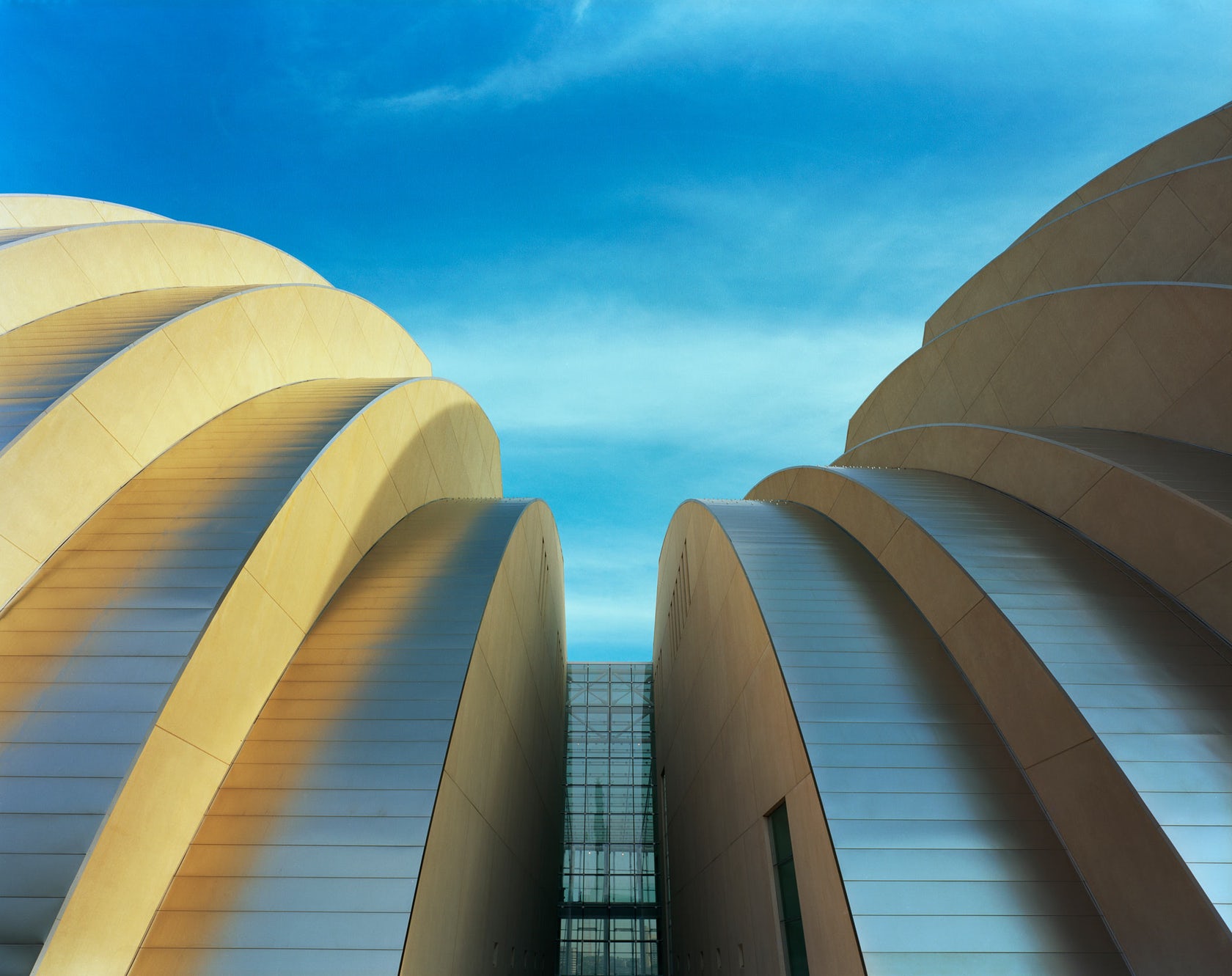
Kauffman Center for the Performing Arts by Safdie Architects in Kansas City features metal siding by GKD-USA
Metal Cladding Systems
Metal is commonly used for non-structural, rain-screen cladding systems, where the priority is to provide protection from the elements as well as a striking external finish. Thanks to its foldable, malleable nature, metal panels can be connected together and attached to a building in a wide variety of ways, each system offering different benefits in terms of construction complexity and aesthetic finish. Some of the most widely-utilized systems are as follows:
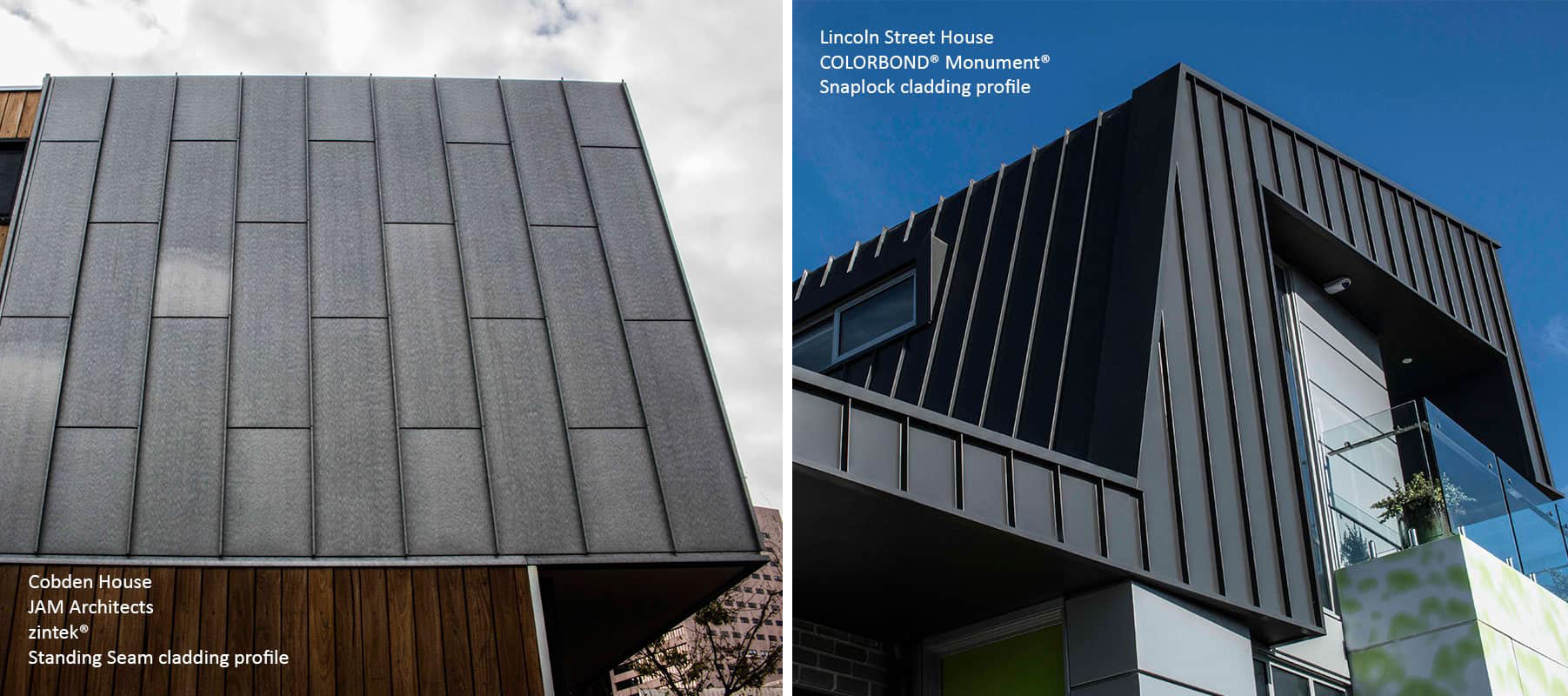
Via Metal Cladding Systems
Standing seam: One of the most recognizable systems, standing seam cladding is characterized by robust folded connections between each panel. Its concealed fixing details allow for sleek architectural exteriors, making it a popular choice across typologies. Standing seam systems can be used with many different types of metal, including aluminum, galvanized or stainless steel, titanium, zinc and weathering (Cor-ten) steel.
Snaplock: A simpler alternative to standing seam, snaplock displays a similar ribbed profile but does not require specialist closing equipment to install it. Snaplock panels are designed to “snap” together, offering a low-fuss installation.
Via Metal Cladding Systems
Interlocking: An interlocking system offers up a smoother appearance with dramatic, express joints. Interlocking metal cladding panels can vary in width, and can be detailed to run horizontally, vertically or even diagonally.
Flatlock and shingle: Flatlock panels lock together to create a flush, flexible, thin façade. The system can also be installed in reverse, creating deeper express lines; this is called “Reversed Flatlock.” For a striking variation on the flatlock system, a shingled metal façade can be created using panels folded into interconnecting tile shapes.
Via Metal Cladding Systems
Cassette: Ideal for large cladding areas, the open-jointed cassette system can be used with huge panels up to 13 feet in length. The cassettes are bent and fixed with invisible clips, usually to an aluminum framework, and result in a contemporary, flat appearance.
Custom: If none of the above options are a fit for your specific project, a bespoke system can be developed by a specialist manufacturer, altering an existing system or creating something completely new. Project budget will need to be considered in the case, since customization will increase the cost substantially.
Search for Metal Cladding Manufacturers
Materials
Metal cladding encompasses a plethora of different materials, each with its own unique strengths and weaknesses. Your material choice will be influenced by a number of project-specific factors, including desired aesthetic, climatic conditions, chosen structural system, the nature of adjacent materials and the construction budget. The following are among the most common material options for metal cladding:
Left: Stainless steel; via Ideal Spec. Right: galvanized steel; via Wild Textures
The façade of Elevon Campus by Ehrlich Yanai Rhee Chaney Architects is clad in weathering steel by Dissimilar Metal Design
Stainless steel: Steel coated in a thin layer of chromium oxide is commonly referred to as stainless steel. The chromium helps prevent the oxidization process of corrosion occurring, so the material is resistant to rusting. Stainless steel is also popular for its clean, polished finish.
Galvanized steel: Galvanized steel is coated in a thin layer of zinc, and helps to prevent rusting in a similar manner to stainless steel’s chromium layer. Visible crystallites in the coating give galvanized steel a mottled aesthetic feature known as “spangle”.
Weathering steel: Often referred to as COR-TEN steel, weathering steel is designed to form a protective layer over time that displays a consistent rust-like appearance. This layer acts as a barrier against corrosion and eliminates the need for painting. Its earthy, industrial aesthetic is striking, but COR-TEN cladding must be detailed correctly to ensure it retains a consistent patina over time.
Left: The aluminum façade of Essex Crossing by SHoP Architects, New York. Right: The titanium skin of Guggenheim Bilbao by Gehry Partners, Bilbao, Spain; via Condé Nast Traveler
The stunning zinc roof of Ga On Jai by IROJE KHM Architects was manufactured by VMZinc
Aluminum: Aluminum is naturally resistant to rusting or blistering, making it a popular cladding choice for contemporary projects. It also possesses an excellent strength-to-weight ratio, meaning aluminum façade attachment systems can be less bulky than those for steel panels. That said, the material is prone to denting and scratches, and may corrode under certain environmental conditions without proper care. Read about SHoP’s detailing of a striking, torqued aluminum façade for Essex Crossing in New York.
Titanium: Titanium is favored by architects for its light weight, high strength and glossy, reflective appearance. Over time, a protective oxide film forms on the material’s surface, increasing its resistance to corrosion. That said, maintenance is key with titanium cladding, as Frank Gehry will attest — his iconic Guggenheim Bilbao was left with brown staining when it was not properly cleaned after construction.
Zinc: Lauded for its weatherproof, corrosion resistant qualities, zinc is immune to the harmful effects of UV rays and even possesses self-healing properties, meaning that if scratched, the material can recover itself with time.
Copper cladding at the Columbus Museum of Art, Margaret M. Walter Wing by DesignGroup; photos by Brad Feinknopf
TECU® brass cladding at the Transfer Centre for Adaptronics (Fraunhofer Institute), Darmstadt, Germany; via MIXX Cladding
Copper: Another lightweight cladding option, copper is very durable compared to other materials, and at the end of the building life is also 100% recyclable. Its subtly reflective appearance evolves over time due to oxidization, turning the metal a distinctive green color.
Brass: Striking a balance between the cool hue of zinc and the warmth of copper, brass is a highly malleable cladding material that makes it well suited to decorative sheet metal work. Over time, brass takes on a golden-brown patina as its surface oxidizes.
Search for Metal Cladding Manufacturers
Performance
One of the primary reasons metal is a popular cladding material is its resiliency. When the right material is combined with well-considered detailing, a metal building envelope can help a structure last for years or even decades longer than it otherwise would have. That said, there are a number of performance factors to consider in order to use metal’s strengths to your advantage in a project:
Durability: While metal is generally highly durable, some metals are softer than others and can be scratched or dented by hale and other objects. The geographic location and intended lifespan of a building should therefore be considered with respect to a material’s resilience. Be sure to let manufacturers know the durability requirements of the building envelope so they can assist you in identifying the right material for your project.
Fire resistance: Metal is generally very resistant to fires, but it is still advisable to consult with manufacturers on the fire-resistance rating requirements of your cladding. It is also important to consider how the metal cladding relates to other materials within a building envelope to avoid unforeseen consequences. The recent Grenfell Tower disaster was a tragic reminder of the importance of specifying safe building-products for high-rise construction, and the need for open communication by all parties — architects, manufacturers, contractors and regulators — on this subject.
Typical section through a metal-clad rainscreen façade; via Alucobond
Thermal insulation: Metal cladding systems often contribute little to overall wall insulation values, so it’s likely necessary to attach a sheathing board to the external face of the infill walls for weather and thermal resistance. If your building has a minimum U-value and you need the cladding to help reach it, talk to a specialist metal cladding manufacturer to find the ideal system. The U-value defines the thermal transmittance of a building envelope, which is the energy in Watts (W) passing through a square meter of construction per degree temperature difference from inside to outside.
Acoustic insulation: Metal cladding generally provides limited sound insulation between the external and internal environments. Suppliers often calculate whole-of-wall ratings, factoring in the Rw rating (weighted sound reduction index) or STC (sound transmission class) of the insulating infill-wall products.
Environmental factors: Particularly for large scale projects, it is important to consider the environmental impact of a building material over its entire life cycle, including the manufacturing process, installation process and long-term maintenance requirements. A life cycle assessment provides a rigorous method for measuring each of these factors when deciding which cladding system is most appropriate for your client’s needs.
Wind Action: Building cladding systems are required to sustain wind actions and transfer them to the main building structure. The guidance given in chapter 30 of the ASCE 7-10: Minimum Design Loads for Buildings manual can be used to determine the natural wind actions to be considered during the design of cladding.
Expansion & Contraction: Some metals contract and expand with changes in temperature, humidity and pressure, and if the wrong material is specified, this can lead to permanent building damage. Consult with your manufacturer to establish which metal cladding product is most appropriate for the climate in which your project is to be located.
Search for Metal Cladding Manufacturers
Finishes
Almost as important as the selection of the metal itself, finishes can have a significant effect on both aesthetics and performance of metal cladding systems. There is a virtually unlimited range of finishes for metal façade panels — enquire with your manufacturer to find the perfect one for your project. The following are among the most common:
Left: Typical sand blasted metal finish; Right: Typical brushed metal finish
The high-gloss finish of Extension Primary School by Bonnard Woeffray, Bovernier, Switzerland
Sand blasted: Sand blasting lends metal a smooth, matte surface, virtually free from texture. Sandblasted steel can be vulnerable to rusting and should be protected with specialty paint or other coating.
Brushed: Brushed or dull-polished metal displays a unidirectional satin finish with a subtle grain that varies in intensity depending on the level of abrasive action during manufacturing.
Mirrored: The most reflective of all finishes, highly polished finishes offer a striking aesthetic but require a high level of maintenance to ensure their glossiness remains.
Left: Typical engine turned metal finish; Right: Typical powder coated metal finish
Patterned metal finishes by Marcel Wanders and PURE + FREEFORM
Engine turned: Engine turned finishes feature a fine geometric pattern inscribed into the metal, offering a swirled appearance with varying reflective qualities.
Powder coated: Powder coating gives metal a protective layer and a uniform matte aesthetic. Powder coated finishes are available in an unlimited choice of colors.
Patterned: Intricate patterns and complex color combinations are possible — PURE + FREEFORM’s Chameleon Collection is a standout example. Ask manufacturers about the possibilities of even more unique finishes.
Search for Metal Cladding Manufacturers
Case Studies
Given the range of different metals and cladding systems available, precedent studies can form a vital part of an architect’s research during the design development and specification stage of a project. Covering innovative material applications, great performance qualities and unique aesthetic effects, the following features should inform and inspire you as you search for the ideal metal cladding product:
Sherbourne Common Pavilion by Teeple Architects Inc., Toronto, Canada
Pushing the Envelope: 7 Bold Buildings Clad in Metal
Seven projects explore metallic façades, skins and building envelopes that are particularly fascinating. Spanning specialty box-rib metal to shockingly affordable and standardized sheets, together these projects form an indispensable catalog for inspiring any stunning metal façade design. Check out the full collection here.
Lillehammer Art Museum and Cinema Expansion by Snøhetta, Lillehammer, Norway
Silver Lining: 7 Lustrous Buildings Clad in Stainless Steel
Thanks to Frank Gehry’s endless sweeping forms, stainless steel’s ubiquity throughout the art deco period and its widespread usage as a contemporary decorative and ornamental material, each and every one of us has feasted our eyes on a luminous stainless steel structure. While the material’s widespread usage may not be new, through strong execution and modern application, the following projects retain a novel beauty. Check out the full collection here.
Bloom; via dOSu-Arch.com
Metal in Motion: What If Building Skins Resembled Human Skin?
Breathable and self-sustaining, there is no façade more dynamic than the “first” skin — our own. And so, what if building skins moved toward intentionally mirroring human skin? Imaginative biologist-turned-architect Doris Kim Sung is urging designers to think about thermobimetal, an experimental alloy with the unique ability to move and expand when heated. Check out the full story here.
COBE’s The Silo under construction; photo by Rasmus Hjortshooj
Architectural Details: COBE Transforms The Silo With a Complete Metal Makeover
Copenhagen’s coolest metal-clad construction was recently completed by innovative Danish design studio COBE. The firm’s highly anticipated project, The Silo, is an old industrial grain storage facility–turned–apartment complex set within the city’s redeveloping Nordhavn district. With four new galvanized-steel façades featuring faceted balconies, the building’s monolithic concrete-clad past is utterly unrecognizable. Check out the full story here.
From left to right: Villa Criss Cross Envelope, Football Stadium Arena Borisov, Winter Kabin on Mount Kanin; images via OFIS arhitekti
Architectural Details: 3 Cladding Concepts by OFIS Arhitekti
Ambition and expertise come together harmoniously in the otherwordly projects of Slovenian studio OFIS Arhitekti. Not only has the Ljubljana-based firm produced some of the most daring architecture seen over the last few years — think the prefab Alpine Shelter Skuta set 6,562 feet over the Slovenian Alps — they also possess a thorough knowledge of materiality. More specifically, they boldly maneuver metal with an unparalleled mastery and grace. Check out the full story here.
Search for Metal Cladding Manufacturers
The Extended Entry Deadline for Architizer's 2025 A+Product Awards is Friday, February 21st. Get your brand in front of the AEC industry’s most renowned designers by submitting today.