Architects: Showcase your next project through Architizer and sign up for our inspirational newsletter.
At their best, glazed façades are one of the most recognizable and glamorous components of buildings today. However, characterized by endless iterations and customizations, they are not exactly a simple architectural solution to parse out. We spoke with Marc Simmons, Principal at design and façade consulting group Front, who assured us that “the question of how to specify just isn’t that easy.” Occupying a position at the forefront of building envelope and façade consultation, Front boasts an unmatched portfolio of custom-designed curtainwall systems, bespoke cladding systems and geometrically challenging building forms.
According to Simmons, “Every project is unique for its geography, climate, client, user groups and so forth. So, the beginning of the project is all about looking around all these corners to identify the criteria, which can be really extensive. Simple ones include solar control, thermal comfort, glare and the ability to withstand wind and seismic conditions.”
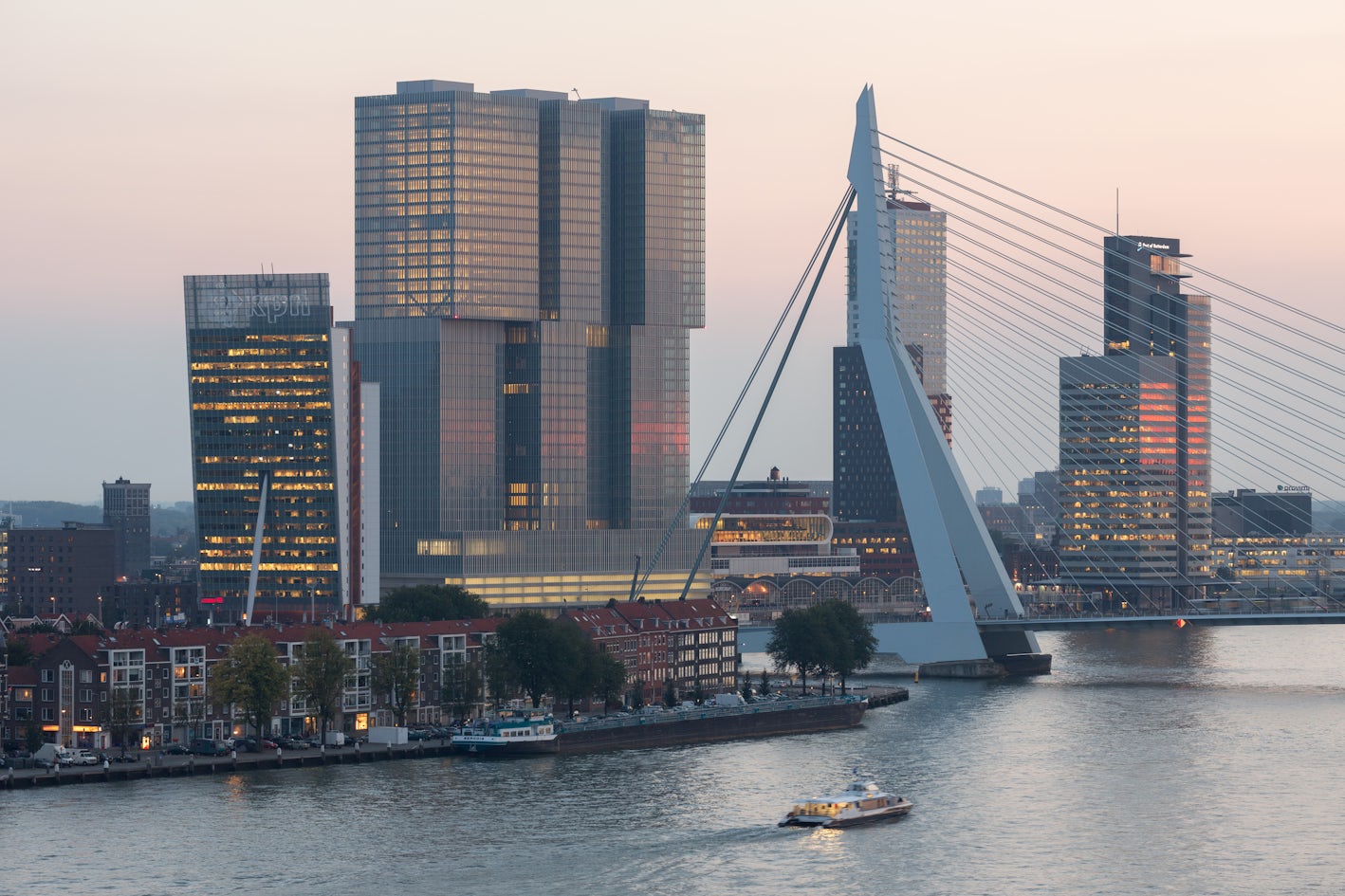
© OMA
De Rotterdam by OMA
Basic Categorization
Curtain wall: A curtain wall is a non-load bearing exterior wall that hangs off the structure like a curtain and is typically attached to the building’s floor slabs. A curtain wall does not carry any dead load weight imposed by the building and therefore only has to support its own weight. The wall transfers wind loads onto the main building structure through connections to the building’s columns and floors.
Both beautiful and highly functional, curtain walls are designed to resist air and water infiltration, withstand sway induced by wind and seismic forces and provide a thermal barrier between inside and out. When designed for large buildings, curtain walls are almost always customized to an individual project’s needs.
Storefront wall: Located on the ground floor, a storefront wall is a non-load bearing glazed wall that spans between the floor slab and the building structure above. “Today, generic storefronts with aluminum extrusions and glass that is 5-feet x 10-feet, are sometimes considered banal; people want an Apple cube. But in many ways, it’s kind of a miracle because it’s cost effective and quite nice,” Simmons said.
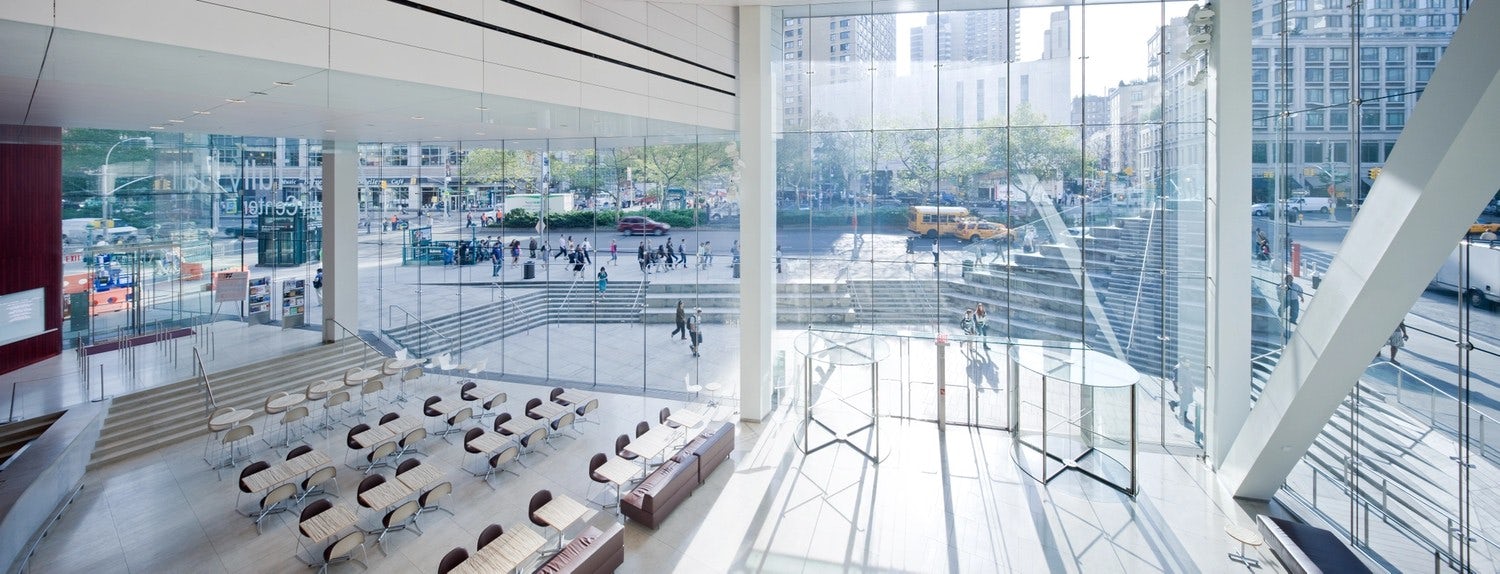
Alice Tully Hall at the Lincoln Center of Performing Arts by DS+R; image via DS+R
Framing Systems
Stick Systems: Stick system curtain walls are those completely assembled in the field. They are built from long vertical extrusions or support mullions that are attached to the building’s structure. Typically, shorter horizontal extrusions span between the vertical mullions, creating a rectangular frame that binds the glass on all four sides. The infill material — in this case glass — is then installed into these frames on site.
© Iwan Baan
Designed in consultation with Front, Grace Farms by SANAA features a frameless stick system glazed façade
Mullions are commonly composed of aluminum, steel, — which is stronger but more expensive than aluminum — wood and concrete. Stick systems can also be created using glass that is vertically frameless, but captured in the horizontal direction, as pictured at Grace Farms.
Sticks systems, which are associated with more costly and specialized on-site labor, are most common amongst low and mid-rise glazed buildings. “There are four key ways to secure a piece of glass to a frame,” Simmons said. “It’s either attached using structural silicone, toggle locked, bolted or pressure capped.”
Unitized Systems: Unitized curtain wall systems are composed of large glass units that are assembled to frames in a factory, and thus arrive to the construction site as an already continuous system. These units can be designed to span multiple floors or horizontal modules, and can incorporate multiple cladding elements, including operable vents and windows. One of the hallmarks of unitized systems is that because they are assembled in a climate-controlled environment, manufacturers can ensure high-performance quality, including air and moisture protection. Completed in factory, units are then shipped to the project site and lifted onto the building face, typically using floor-based equipment, monorails, mobile street cranes or tower cranes.
© Skidmore, Owings & Merrill (SOM)
Closed Cavity Façade by Skidmore, Owings & Merrill LLP (SOM)
Semi-Unitized Systems: Semi-unitized systems combine some of the advantageous features of both stick and unitized curtain wall systems. Unlike stick systems, where glass delivered to the construction site on its own, each piece of glass is pre-bonded into a smaller metal cassette that is eventually locked into a larger frame on site. As a result, on-site assembly includes connecting metal-to-metal frame components, mediated with gaskets, which is fast and safe. It also precludes the need for site-applied structural silicone. “Nobody really likes working with structural silicone on site; it does happen, but when you can avoid it, you should,” Simmons said. “Structural silicone is always best done in climate-controlled factory conditions by experienced technicians.”
Spandrels: Since curtain wall systems span across floor slabs, there is a need for an opaque cladding material that will conceal the slab edge, columns and any mechanical systems located between each floor. This is where spandrel glass comes into play. To achieve opacity, spandrel glass is treated with a frit, film or is incorporated into an assembly called a shadow box. Spandrels can be harnessed to create complete harmony with the building or render visually contrasting effects. Functions such as thermal insulation, sound insulation and protection against fire should also be considered when detailing spandrels.
Designed in consultation with Front, Stavros Niarchos Cultural Foundation Center by Renzo Piano Building Workshop features a 24-meter-high composite steel and structural glass wall with motorized exterior blinds; image via Dezeen
Building Performance
Energy Efficiency: Building an air-tight, highly insulated glazed façade requires careful detailing and precise material selection. As explored in a previous article, How Long Until We See Quadruple-Glazed Windows Become the Norm?, the Passive House Institute posits that for a building to achieve the highest levels of efficiency, it must be fitted with low-e glazings filled with argon (most common) or krypton gas (most expensive).
Today, glazing systems are manufactured to transmit an adequate amount of visible light while minimizing heat gain. When browsing glass products for exterior applications, manufacturers will offer several values that will help you parse out a particular product’s thermal performance. Here are a few to keep in mind:
- Low-E Glass: Low-E glass has a microscopically thin, transparent coating that reflects long-wave infrared energy and thus has lower emissivity. This thermally reflective material reflects both heated and cooled air back into the interior of a building, rather than allowing it to flow out.
- Solar Heat Gain Coefficient (SHGC): The SHGC is the fraction of solar radiation that is admitted through a glazed façade or more traditionally, window panes. The SHGC is expressed as a number between 0 and 1. The lower a window’s solar heat gain coefficient, the less solar heat it transmits.
- Visual Light Transmittance (VLT): VLT is the percentage of transmitted visual light that passes through the glazing. When good daylighting is important, a higher VLT is desirable.
- Building Integrated Photovoltaics (BIPV): BIPV are an increasingly popular approach for using the building skin as a means to harvest solar energy. Leading manufacturers of photovoltaic glass include Onyx Solar and PolySolar.
Acoustics: With the proliferation of high-rise glazed buildings in noisy urban areas, prescribed acoustic requirements have become a prevalent concern in designing building envelopes. Several classification indices, including Sound Transmission Class (STC) and Outdoor-Indoor Transmission Class (OITC), are used to evaluate the acoustical performance of architectural products.
Security: According to Simmons, “Around one-in-five projects that we do has explicit security concerns that are dominant over other considerations.” Involving protection against human-initiated and natural catastrophic events, façade consultants in collaboration with security consultants can make several recommendations if you are designing a high-threat facility.
IAC Building by Frank Gehry; image via Richard Kohler
Aesthetics
The type of glass you select for your cladding is one avenue through which you may create a bespoke glazed face. These include — but are not limited to — colored glass, fritted glass, etched glass, mirrored glass, reflective glass, patterned glass and channel glass.
“One thing to remember is that reflective glass does not mean better energy performance. These days, the spectral selectivity of the coatings is engineered at a molecular level. So, coatings can be engineered very well while still remaining relatively clear. Others are engineered to deliver a broad range of reflectivity and color, giving people more aesthetic choices.”
Low-iron glass: Low-iron glass is manufactured with a lower iron content than standard clear glass and is often used to avoid the noticeable green tint that sometimes results from multi-layered glass constructions.
Transparency and Switchable Glass: Glass can range from virtually transparent to nearly opaque. Front is now deploying switchable glass, which uses electrochromic technology to interchange between a transparent and opaque state. Today, two of the world leaders in electrochromics are View Glass and Sage Glass.
© Zaha Hadid Architects
Guangzhou Opera House by Zaha Hadid Architects
Geometric Customization: Many firms, including Zaha Hadid Architects and Gehry Partners, have created complex geometric glazed façades that demonstrate that the possibilities for aesthetic customization are endless. If you are a smaller firm hoping to create bespoke, twisted profiles, it is best to consult with a glazed façade specialist, as they will be able to expand beyond standard specification and thus help you coordinate design, installation and budget.
When it comes to most medium to large-scale projects, it is often best to work with a building envelope consultant or façade consultant. However, as a Professor at Princeton and Georgia Tech, “one thing I tell my students is to not diss off-the-shelf stuff,” Simmons said. “Basically everything that is off-the-shelf was originally custom. It was invented by somebody for very specific reasons at a very specific time and then the benefits of whatever that system was, became popularized.”
“Even though they’re not fancy, they’re often a testimony to the survival of the fittest in a kind of building technology war.”
Case Studies
Emporia by Wingårdh Arkitektkontor AB features glazing by CRICURSA and Vanceva
Mind-Benders: 5 Unbelievable Curved Glass Façades
Glass is not the delicate, inflexible material that it used to be. Improvements in the manufacturing process have made it stronger, purer and thinner than ever before. These high-strength sheets can be shaped by machines, in specialized furnaces or on site, without breaking; enabling architects to create sculptural glass buildings. These façades bend, twist and undulate, proving that in our parametric present, curved glass is the wave of the future. Check out the full story here.
JTI Headquarters by Skidmore, Owings & Merrill LLP (SOM) features curtain walls made with Josef Gartner GmbH
Building Transparency: 6 Extraordinary Curtain Walls
Layering space, curtain walls balance conditions along the envelope to control thermal expansion, movement, cooling, lighting and water diversion. Taking a sampling of innovative curtain wall systems, the following projects illustrate different framing and installation types. Collectively, they begin to show how curtain walls can be specified and realized through collaboration between architects and manufacturers. Check out the full story here.
Architects: Showcase your next project through Architizer and sign up for our inspirational newsletter.
Header image features Closed Cavity Façade by Skidmore, Owings & Merrill LLP (SOM)