The Extended Entry Deadline for Architizer's 2025 A+Product Awards is Friday, February 21st. Get your brand in front of the AEC industry’s most renowned designers by submitting today.
Oftentimes, bespoke materials found in iconic design projects are mimicked in other architectural applications. What is one building’s beautifully textured cladding might end up as another’s interior wall paneling. Such inspired design choices can be considered inherently flattering. It makes sense to adopt successful design details and material specifications and reinterpret them in fresh ways. If architects never attempted to reimagine older design ideas and material methodologies, then we’d be stuck with the same boring buildings across the world.
That’s why it’s important to understand the unique ways in which inspired design has opened up new doors for certain age-old materials over the last few years — specifically, terrazzo. Though it was once a widely specified building-product in cultural institutions, schools and hotels across the United States, it’s not been a highly coveted contemporary material — but that’s changing. Terrazzo adds a luxurious component to both interior or exterior designs and can be used in truly innovative, sustainable ways, yet architects often don’t choose it because it can be expensive and difficult to detail.
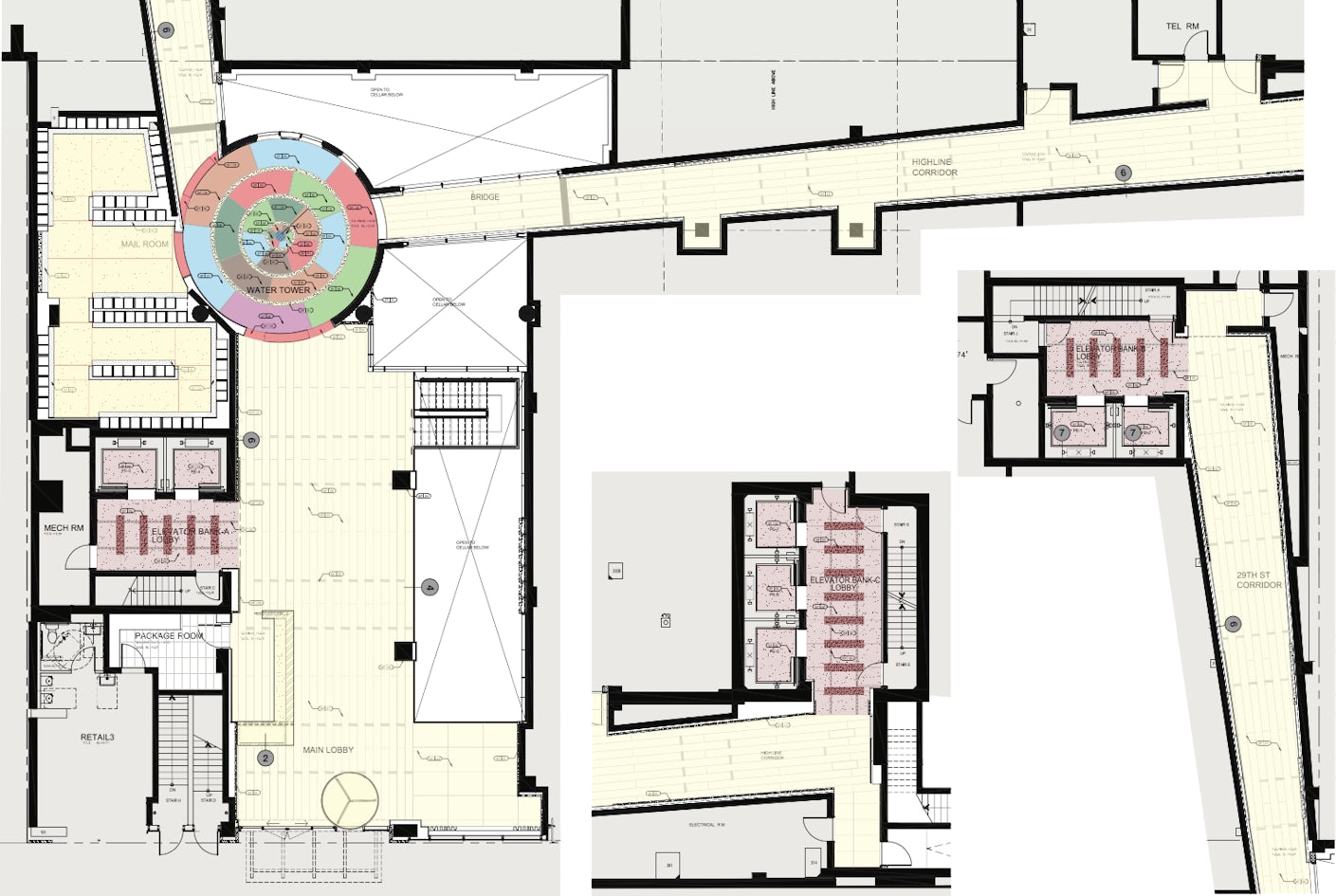
Detailed plan of the interior lobby at 507 West Chelsea featuring terrazzo flooring; courtesy Durite
One design firm, however, recently specified a custom terrazzo mixture for the floor of one of Manhattan’s newest tower developments after being influenced by a popular park nearby. Designed by Ismael Leyva Architects, 507 West Chelsea features a stunning flooring system made to look like the lengthy concrete pavers found on the world-renowned High Line, which it sits adjacent to. Using a matrix binder of varying gray tones, small brown and blue aggregates and metal insets, the terrazzo panels appear as if they were plucked right off the linear park itself and smoothed down to a shiny polished finish.

Rendering of interior lobby of 507 West Chelsea; courtesy Ismael Leyva Architects
The designers partnered with Durite, a surfaces manufacturer based out of Great Neck, New York, to fabricate the custom terrazzo flooring in the High Line’s signature subtle palette. To get the details and colors correct, the architects produced a map — similar to a paint-by-number diagram — that outlined the desired relationship between the varying aggregate sizes, metals and the concrete mixture.
Installed terrazzo flooring at 507 West Chelsea; courtesy Ismael Leyva Architects
Throughout the project, it’s easy to see the design influence that resides just outside the lobby doors. Even the silver Schluter strips evoke the panel dividers and joints found on the High Line itself. In the elevator lobby, Ismael Leyva created an even more blatant nod to the famous man-made parkland with a design pattern drawn from the repetitious abandoned train tracks.
Achieving such a custom look using terrazzo is what makes the material so valuable. Rarely will you find terrazzo flooring that perfectly matches a finish found in another structure. While prefabricated panels do lend themselves to a more exact design from panel to panel, poured-in-place terrazzo systems require a bit more finessing because it’s more difficult to control the aggregate placement.
Above video unveils the complex installation process for poured concrete flooring.
For 507 West Chelsea, the architects chose to pour an epoxy resin terrazzo because of the large-scale expanse of the lobby — it totals more than 5,500 square feet. This resulted in a mixture made from Durite’s patented Durazzo process, an innovative cutting and mapping system that ensures a low tolerance of 1/16 of an inch on each panel poured. The High Line inspired metal insets (manufactured in Ohio by National Metals) as well as specially sourced Quartz aggregate that Durite sells as a “concrete polymer” contributed to the paver-like look of the lobby’s terrazzo floor panels. They also used a blue stone from Turkey that ranges inside from 1/2 of an inch to 3/8 of an inch.
Detail of typical lobby terrazzo flooring pattern with metal insets; courtesy Durite
In addition, Durite incorporated a 2-inch-wide Zinc strip, instead of actual metal Schluters, to act as control joints between the panels, which allows for thermal expansion and prevents cracking. Cracking more commonly occurs in monolithic cement-based matrixes that don’t have an underbed membrane or layer of sand, which is used as a base structure for epoxy terrazzo systems.
Left: CAD drawing of standard, epoxy terrazzo base flooring; right: diagram of standard epoxy terrazzo system with vapor barrier; courtesy National Terrazzo and Mosaic Association
Cutaway model showing a typical poured-in-place cement terrazzo system with metal divider underbed; courtesy National Terrazzo and Mosaic Association
Typical dividers such as these are often an alloy of zinc, brass or plastic and vary in width from 18 gauge to ½ inch, 16 gauge or ⅛ inch. According to the National Terrazzo and Mosaic Association, dividers must be located directly over concrete joints, which should occur a maximum of three times the depth of the concrete in inches. Concrete joints should also be detailed to run off all corridor intersections and corners and never be spaced more than 1.5 times the width of the concrete pour. When detailing poured terrazzo staircases, the rules are similar, but most manufacturers also offer precast stair products to match their terrazzo flooring collections.
Left: CAD drawing of poured-in-place terrazzo stair; right: cutaway model of a typical stair detail; courtesy National Terrazzo and Mosaic Association
Though this is a lot to take in, companies like Durite can provide incredibly helpful details and diagrams for architects to better understand the seamless — but admittedly complex — process behind creating poured terrazzo floors. If given well-drawn details, experienced contractors can quickly achieve the architect’s desired look with little to no issues — resulting in a poured floor that can last for decades. In other words, it’s utterly possible, thanks to the durability of terrazzo, that Ismael Leyva’s design for 507 West Chelsea might outlast the actual concrete pavers found on the High Line itself. Who knew that design legacy could be carried out in different materials?
The Extended Entry Deadline for Architizer's 2025 A+Product Awards is Friday, February 21st. Get your brand in front of the AEC industry’s most renowned designers by submitting today.